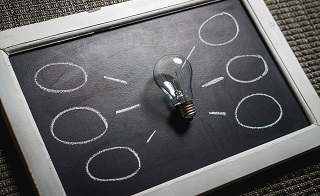
1.はじめに
今回から、下記の表2-1にある「喫緊の課題」の5番目「多品種少量生産がうまく行かない」の発生要因「段取り替えと生産の調整が難しい」に対する解決手段「キャラバン方式生産計画」についてのご説明に入ります。
表2-1 中小企業が抱える喫緊の課題12と課題発生要因17に対する解決策の概要と記載場所
説明は、キャラバン方式生産計画誕生のきっかけになった事例と、キャラバン方式生産計画を適用した成功事例の概要を今回、ご説明した上で、次回から「キャラバン方式生産計画作成手順」のご説明をさせて頂きますので参考にして頂ければと思います。
【この連載の前回:【快年童子の豆鉄砲】(その79)へのリンク】
2.「キャラバン方式生産計画」誕生のきっかけとなった事例
1)対象工程の概要
ドラムブレーキのバックプレートの半製品20数品種(日産数は数個から1,000数百個)を、30数台の溶接機を使って生産する工程で、多品種対応は、3人のセットマンが段取り替えをして対応します。
2)問題の発生
筆者担当工程の前工程の係長から、急激な増注のため午後10時12時まで生産する状況の中、不良品が多発して、混乱を極め、必要数が確保できない状況の説明があり、対処方法の相談を受けたのです。状況説明で分かったことは、生産管理係が作成した生産計画では、段取り替えが集中する時間帯があり、無理を押しての段取り替えが、品質確保に支障をきたし、不良発生を招いていました。
3)対策
対策は、セットマンが、最も効率よく段取り替えを行えることを最優先にする生産計画にすることでした。ただ、そのような生産計画を組むには、一日発生する数十種類の段取り替えが最も効率よくなされるケースを探すわけで、パソコンのない時代でしたので、筆者と担当係長は二週間位その日の内には帰れませんでしたが、その内に、一日の生産計画を幾つかのパターンに集約することができ、生産管理係から昼ごろ出される翌日の生産要求量を基にほぼ時間内に生産計画を立案することができるようになりました。
その係長が、この生産計画に名前を付けてほしい、と言うので、セットマンが機台を渡り歩くことから、とっさに付けた名前が「キャラバン方式生産計画」だったのです。
4)効果
セットマン主体の生産計画が確立できたことにより、生産が安定し、2時間位の残業で済むようになっただけでなく、品質も劇的に良くなりました。その理由は、セットマン主体の生産計画が、最終的に一人のセットマンで殆どけりが付き、二人目のセットマンの担当分は、短時間で終わるようになりましたので、完全フリーの三人目(最も優秀なセットマン)と、二人目の空いた時間を使って、段取り替え作業の改善を集中的に行うことができた結果、安定的に品質を確保することが出来る段取り替えが可能になったからだと言えます。
5)おわりに
これからは、市場ニーズの多様化を受けて、中小企業や、大企業の小規模部門に多品種少量生産が求められるようになることを考えますと、一般的な生産効率優先の生産計画体制ではこの事例が経験した混乱状態になる可能性が高いと思われますので、参考にして頂ければと思います。
3.化学プラントでの事例
1)はじめに
工場内に、ウレタンフォームの製造工場が新設されたのですが、メインラインが、1ヶ月経ってもまともに稼働しない状況打開のため、ブレーキ課長職務を午前中で終え、午後から応援することになり、キャラバン方式を導入して解決した事例です。
2)対象工程の概要
原液を投入してウレタンフォームが出来上がり切断するところまでの完全自動化学プラント(全長80メートル)が対象で、スタート前に、12人で3時間掛かる段取りが必要で、一旦スタートさせたラインをトラブルで停止させると莫大な損失が発生するというラインです。
3)問題の発生
その日の生産内容が必要とする段取り作業を、12人が数組に分かれて数か所での作業をするのですが、予定時間内に段取りが完了してラインがスタートする確率は、5~15%である上、スタート後、停止が必要となるトラブルが一日1~2回発生する状態で、とても予定された量の生産が出来ませんでした。(旧工場との並行生産だったので、納入先に迷惑を掛けることはありませんでした。)
4)対策
全ての段取り作業をリストアップしてカード化し、アロー・ダイアグラム法(注)に従って、並行作業、クリティカルパスが分かる形にアロー・ダイヤグラムを作成したところ、作業者が、キャラバン方式で作業すれば、全体的には結構余裕時間が取れることが分かったのです。
(注)新QC七つ道具: アロー・ダイヤグラム法の使い方(その1) 挑戦計画立案
...