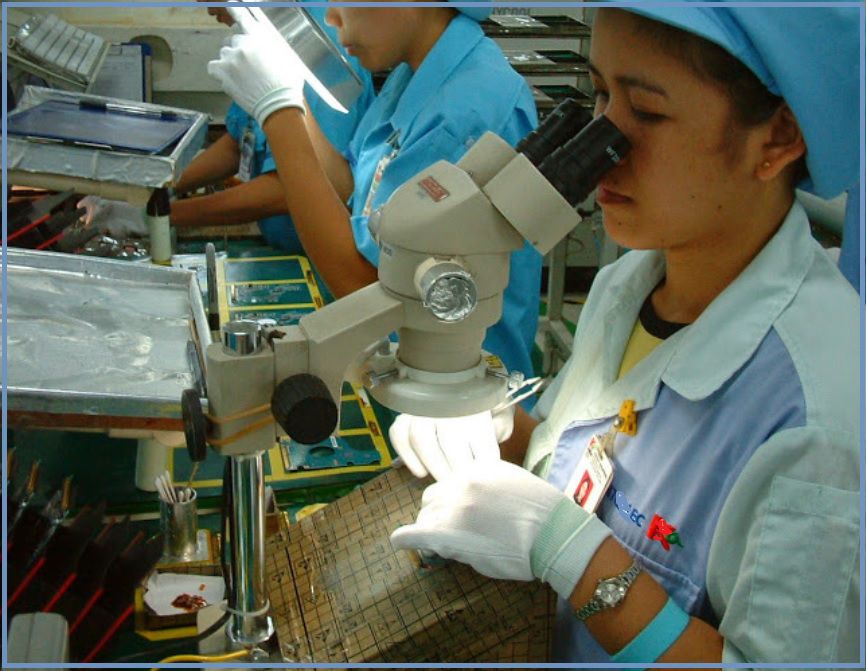
【不良原因解析2段階なぜなぜ分析法の目次】
1.工場の不良対策、検査の仕組みを設計する
2.クレーム対策方法、クレームをゼロにするには
3.不良原因解析と再発防止2段階なぜなぜ分析法
4.慢性不良対策の特性要因図による解析事例
5.不良原因解析と再発防止2段階なぜなぜ分析法の基本ステップ
6.是正処置の意味(クレーム対策書とは)
7.品質保証部長は最優先で不良の流出を止める事
◆ものづくり セミナー サーチ なぜなぜ分析へのリンク
◆工場の不良対策、検査の仕組みを設計する
品質改善、不良対策は、単発的に管理手法を導入しても効果は期待できません。品質保証部として最優先で取り組まなければならない事は「止血」です。そこで、検査の役割がクローズアップされてきます。検査は付加価値を生まないと言われていますが、顧客の立場に立った見方を工程へフィードバックする目的の検査は、一定の効果が期待されます。
1.流出防止策を講ずるとは
設計部門が悪い、品質システムが定着していないと言っても、品質は良くなりません。まず自部門の品質保証部内をしっかり固めることです。品質保証部としてできる事、外に不良を出さない対策から始めることが重要です。
ここで実績を上げたなら、社内への影響力を拡大し、本格的に本来の不良の発生源を止める対策に着手します。不良が止まったことで、まず顧客からの信頼が得られ、そして、社内改革実施のきっかけとなるのです。これは、企業に所属していた筆者自身の経験から得た事実です。
2.検査工程の設計と運用
冒頭で述べた通り、お客様に迷惑が掛からないように、まず市場への流出防止の重要性を認識し、対策を講じます。一時的にお金の掛かる手段もやむを得ないのです。これが今の工場の実力として理解し、一時的なコスト上昇はやむを得ないと考え、検査を強化して、社外への流出を止めます。
(1)検査工程を設計する
どの工程で何を検査するか、全数検査か、抜き取り検査か?または巡回検査か?など、製品や工程の品質状況に応じて決めます。常に効果を把握し、やり方を改善していく、現場の管理者との情報共有は重要です。検査の工程の種類としては、次のものがあります。
①受け入れ検査
②工程内検査(自主検査)
③工程巡回検査
④出荷検査
⑤最終抜取検査
⑥立会検査、出講検査
⑦協力工場工程監査
検査の方式としては、次の5種類に分かれます。
①抜取検査
②片側検査
③両側検査
④順次検査
⑤全数・全長検査
検査の意義としては、次の3つがあります。
①不良品の流出防止
②モノの品質を見て、工程管理の仕組み改善へ反映
③顧客の立場でモノを見て出荷品質を保証する
また、検査工程を入れるもう一つの目的として、工程STOP、出荷停止処置を取るための情報を素早く入手することです。そのために品質保証部門の「出荷停止」権限を明確に規定します。
(2)検査工程を運用する
検査工程を設計し、検査員を配置したら、当たり前のことですが、継続的に運用し、その検査の効果を図る必要があります。検査数量、検出した不良数量、不良内容を毎日記録し、前工程に対して不良が発生しないように情報をフィードバックし、翌日の検査で効果を見ます。この作業を継続して行うことは大変な根気と熱意がいります。管理監督者は、よくこの仕組みを理解し協力しあって、品質を良くしていこうとする雰囲気を作って行かなければ続きません。検査部門(品質保証部門)の役割を整理すると次の通りです。
①検査工程設計
②出荷品の検査による品質保証
③出荷指示、出荷停止指示
④検査技術の改良
⑤検査員の資格認定
⑥立会検査
(3)検査の位置づけ
実は、効率的な検査工程、検査員のあり方について、流出防止の重要性を理解しながらも、ほとんど有効な手が打たれていない状態となっています。
①検査を行っているが、不良流出は止まらず、目的や方法が形骸化している
②人材を検査員として教育し、有効に機能させる方策が打たれていない
③検査工程をどこに、どんな手段で配置するか、考慮されていない
以上の3点について、品質保証部長の正しい現状認識と決断が必要で、もっと与えられた権限を充分に活用すべきです。検査は、お客様の立場で品質確認をするという「保証検査」の役割を十分に果たすことが求められます。特に官能検査と言われる、アナログ的な判定では、自工程検査ではどうしても甘くなりがちです。そこは、しっかりと顧客と取り交わした「限度見本」で、訓練された検査員が判定する体制を取ることです。
(4)全数検査の限界
良く行われる人海戦術で、工程の最後に検査員を置いて、全数検査を行う場合を想定してみます。これは、人件費の安い新興国の工場で良く行われている手法です。しかし、この方法も安心できないのです。検査員は、指示された箇所の検査は一生懸命まじめに行います。ところがそれ以外の検査はしません。
工程ではあらゆる不良が発生する可能性がありますが、ここは良く不良がでるから注意しようとか、あの作業者は良くミスをするので、検査もしっかり見ないとダメとか、仕事に応用が利かないのです。
また、始めた当初は緊張感を持って検査しますが、時間が経つにつれ、見逃しが起きる様になり、全数検査を入れれば安心という考えを持っていると、思わぬ失敗をすることになります。全数検査は緊急時を除き、人手による方法は避けるべきです。
「自動検査機」など、機械化を検討すべきです。既製品は高価なため、できれば自社で、簡単な専用装置を考案して導入します。顧客との契約上、あるいは顧客の信頼を得るために必要と判断した場合に導入を検討します。
(5)検査員の待遇
検査員として教育するためには、検査員は待遇面での優遇や生産現場での権限付与などを制度化し、一般労働者とは違うという意識を本人や周りの労働者に対して植え付けることが重要です。優秀な人材を労働者の中から発掘し、会社を長期間辞めずに検査員として熟練度を積み上げられるように環境を整えることが有効です。
検査員ごとの不良の発見数、改善提案数の工場内掲示、毎月ごとの表彰、報奨金など、たとえ僅かでも検査員へのインセンティブを与え、意識高揚を図ることも有効な手段です。逆に、不良流出させた検査員に対する再教育制度なども併せて制度化します。
(6)重要な現場監督...