品質の作りこみには、スペックどおりに作られているかという「製品品質の作りこみ」と、使ってみないとわからないという「技術品質の作りこみ」があります。このうち、不確定要素の多い「技術品質の作りこみ」が、近年、開発システムの大型化、開発の分業化や細分化による効率化追求によって、ますます不確実さを増してきました。
この打開策として、プロジェクトマネージメントを中心とした欧米流のリーダーシップによる確実な「技術品質の作りこみ」が主流となりつつありますが、その一方、全世界が注目する“トヨタ”において行われている全員参加で確実なものづくりを実践していく手法「トヨタ式未然防止手法GD3-DRBFM手法」が脚光を浴びているのです。
具体的には、<全員参加><現地現物><なぜなぜを繰り返す>といった、トヨタ流の「技術品質の作りこみ」であり、極めて日本流の素朴な活動と言えます。DRBFMは、旧来のデザインレビューの良さと体系的理論的分析手法であるFMEAを効果的に複合した手法であり、いいところは変えず、変化点のみに注目し、徹底的に「なぜなぜ」を繰り返し、全員参加のもとに、帳票の一元管理化を行う手法なのです。
トヨタ自動車で生まれた未然防止手法であるDRBFMは、トヨタ自動車の手法であるから素晴らしいわけではありません。その本質は、国際標準の安全性評価の考え方であるシステム安全の概念に合致しているからこそ、効果を発揮します.故障解析手法をシステム安全の概念から見直すことで、既存手法がなぜ形骸化するのか、形骸化に対応するためにどのような対応が必要なのかを考えます。
「FMEAをやっているのだけれども効果があがらない」という声もよく聞きます。「過去の事故や不良についてFMEAに記載している」といった間違った認識もあります。重点化できずに広く浅いことや、実施時期も適切でないことから効果がでていないこともあります。検査合格品が市場でクレームとなる、客先で不具合が発見されるなど品質問題に悩まされている工場では、一体何が課題となっているでしょうか?時代は急激に変化しています。厳しい品質要求とともに、多品種少量・短納期開発環境下で、従来型の品質管理手法では流出防止対策が不十分とな...
品質の作りこみには、スペックどおりに作られているかという「製品品質の作りこみ」と、使ってみないとわからないという「技術品質の作りこみ」があります。このうち、不確定要素の多い「技術品質の作りこみ」が、近年、開発システムの大型化、開発の分業化や細分化による効率化追求によって、ますます不確実さを増してきました。
この打開策として、プロジェクトマネージメントを中心とした欧米流のリーダーシップによる確実な「技術品質の作りこみ」が主流となりつつありますが、その一方、全世界が注目する“トヨタ”において行われている全員参加で確実なものづくりを実践していく手法「トヨタ式未然防止手法GD3-DRBFM手法」が脚光を浴びているのです。
具体的には、<全員参加><現地現物><なぜなぜを繰り返す>といった、トヨタ流の「技術品質の作りこみ」であり、極めて日本流の素朴な活動と言えます。DRBFMは、旧来のデザインレビューの良さと体系的理論的分析手法であるFMEAを効果的に複合した手法であり、いいところは変えず、変化点のみに注目し、徹底的に「なぜなぜ」を繰り返し、全員参加のもとに、帳票の一元管理化を行う手法なのです。
トヨタ自動車で生まれた未然防止手法であるDRBFMは、トヨタ自動車の手法であるから素晴らしいわけではありません。その本質は、国際標準の安全性評価の考え方であるシステム安全の概念に合致しているからこそ、効果を発揮します.故障解析手法をシステム安全の概念から見直すことで、既存手法がなぜ形骸化するのか、形骸化に対応するためにどのような対応が必要なのかを考えます。
「FMEAをやっているのだけれども効果があがらない」という声もよく聞きます。「過去の事故や不良についてFMEAに記載している」といった間違った認識もあります。重点化できずに広く浅いことや、実施時期も適切でないことから効果がでていないこともあります。検査合格品が市場でクレームとなる、客先で不具合が発見されるなど品質問題に悩まされている工場では、一体何が課題となっているでしょうか?時代は急激に変化しています。厳しい品質要求とともに、多品種少量・短納期開発環境下で、従来型の品質管理手法では流出防止対策が不十分となり、品質問題の流出が懸念されます。
今回のこの記事では、「FMEA・DRBFM基礎講座」などの講座名でセミナーでも話題の、トヨタ式DRBFMの概要、FMEAとの決定的な違い、DRBFMの進め方について解説します。
▼さらに深く学ぶなら!
「DRBFM」に関するセミナーはこちら!
※本記事を執筆した専門家「濱田金男」が提供するセミナー一覧はこちら!
1. 再発不具合を防ぐ手法としてのFMEA
未然防止活動の一環として、ある会社で発生した品質問題の原因を分析してみると、90%が再発(既知のメカニズム)不具合であることが分かりました。ということは、未然防止が可能だということです。世の中に知られていない新発見要因で起こることはまずありません。
品質問題は、技術開発後の設計変更、あるいは新規設計することにより発生しますが、どこを変えたのか、変更点をチーム活動で、参加者に知らせてなかったために、専門家も気づかなかったのがほとんどであることが分かりました。
理想は、良い設計をし(設計者が気づき)、良く物を観て、良い議論を皆で実施して気づくことなのですが、これだけでは、品質問題をゼロにできません。必ず抜け漏れがでます。各専門家がチェックシートで全ての図面をチェックしてくれれば、抜け漏れを防ぐことができますが、そのようなチーム活動を実施している所は少ないと思います。
このような再発不具合を防ぐ手法として、FMEA(設計段階で漏れなく不具合を予測し、その不具合が起きないように事前に手を打つための手法) が広く活用されています。FMEAはまず設計者が実施し、その後チーム活動で設計者の予測に抜け漏れがないか検討します。
2. DRBFMフォーマットとは
この表は、トヨタ自動車75年史で公開されているDRBFMフォーマットです。
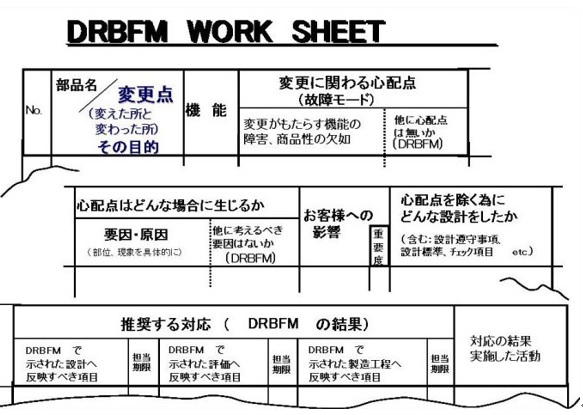
では「心配事」や「変更がもたらす機能の喪失、商品性の欠如」とはいったい何でしょうか。FMEAは設計変更を行った際、二次障害(設計ミスや漏れ)を洗い出すためのツールではなく、故障モードを基に、その影響解析を行うことが目的です。
この基本的な考え方を変えてはいけません。では分かりやすく事例を用いて説明します。
機能の喪失とは、例えばエンジンが掛からない、ブレーキが利かないなど装置の故障の種類を意味しています。故障原因を解析するのは、従来から行われているトップダウンの解析手法で、例えばFTAを用いて解析します。
しかし、FMEAは、原因解析のためには使いません。
例えば、材質を変更したため、錆(さび)が出やすくなるという心配があるとします。
では、その錆はどのような使用シーンの時に起きやすく、また影響が出るかを考えます。
故障モード「錆」ですが、心配点としては「もし錆が発生した場合、その部品はいずれもろくなって破損するだろう。その時、製品にどのような影響を及ぼすだろうか」と考えます。
「錆がどのようなプロセスで発生し、それが製品の故障につながり、事故を発生させる恐れがある」というように、一連の流れの中で、心配点を抽出する必要があるのです。これには、経験と知識が必要となり、漏れを防ぐために有識者を交えたディスカッションが欠かせないのです。
3. DRBFMとFMEAとの決定的な違いは何か?
FMEAは、すべての故障モードを列挙し、その発生原因を取り除く、または緩和する対策を講ずることを基本としています。
しかし、すべての部品、コンポーネントの故障モードを列挙すること、そして、その原因と対策を網羅的にリストアップすることは実際上困難な作業です。
例えば「錆の原因」は様々であり環境条件、使用条件によって変化点を無限に挙げることができます。この作業を一つひとつ設計者が検討し対策する事は問題で不可能に近いことになります。
しかし、DRBFMでは新規点・変更点における「故障モード」を意識した「心配点」を抽出し、さらにDR実施により漏れを防ぐことに重点を置いています。
心配点とは、上位のシステムへの影響(故障)とお客様への影響、そして心配点はどのような状況で起きるか?故障モードとその発生メカニズムを見つけることを狙っています。
つまり、大事なことは心配点のリストアップであって、故障モード単独のリストアップではないということです。
4. DRBFMの進め方
当研究所では、小規模な設計チームでも実施できるように、設計プロセスの中に、トヨタ式DRBFMの手順を落とし込み、実施するための様々なツールを準備しています。
まず設計者によって、心配点の抽出を行う際には「新規点変更点リスト作成」と「セルフFMEA」の実施が必要となります。そしてDR時にレビューアーが実施する「FMEAレビュー」と「簡易評価法」による評価を行います。
このフローは、従来からの設計フローにDRBFMを組み込んだ場合の手順を示しています。
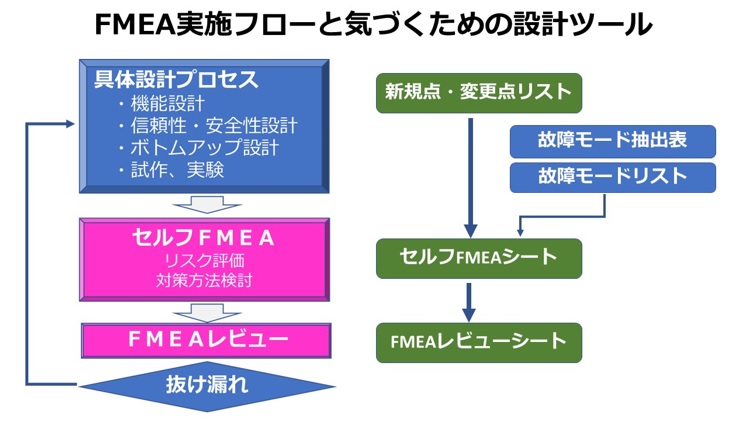
【参考文献】吉村達彦 想定外を想定する未然防止手法GD3 日科技連出版社 2011年
▼さらに深く学ぶなら!
「DRBFM」に関するセミナーはこちら!
※本記事を執筆した専門家「濱田金男」が提供するセミナー一覧はこちら!