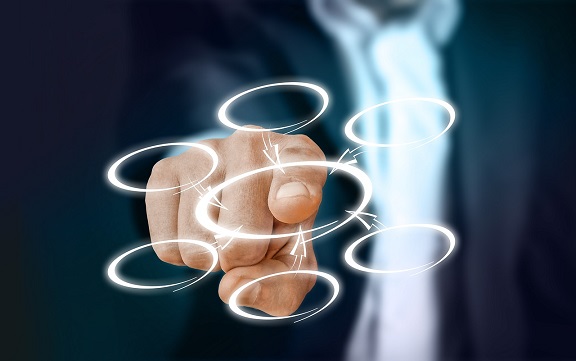
1. 物流改善は3現主義で検討
物流事業者はよく顧客から改善提案して欲しいと言われますが、改善を実施すると自社の売り上げが落ちる場合があります。このため多くの会社が改善の回答をできていない実態にあります。たしかにそういった現象が発生することはあるでしょうが、顧客を相手にビジネスを行っている会社の言い分としてはいかにも情けないものと思われます。
「荷主の効率化=自社の収入減」という構図が頭の中にある以上、提案は行えない、いや行わないという結果に陥ります。荷主はこのような会社とはいずれ付き合わなくなりますのでジリ貧に陥ることは避けられないのではないでしょうか。
もう一つの理由として本当に改善ネタが思い浮かばないということが挙げられるでしょう。顧客である荷主のために何とか改善案を考えたいものの改善の経験と知識に乏しくアイデアが浮かばないのかもしれません。物流改善は物流事業者が顧客向けに提供することだけがすべてではありません。むしろ物流業務に関わる全ての人が物流改善できなければならないはずです。
どうしても物流業にはかつてより人財育成や改善への取り組みが遅れており、先に記したような実態にあることは否めません。かといってこの状態をいつまでも続けていてよいはずがありません。これを機にぜひ改善に取り組んでいきましょう。
ではそのきっかけをどのように持てばよいでしょうか。やはり今自分たちの業務の品質を上げるためには、自分たちの業務を効率化するためには、というテーマを設け、その職場のメンバーで実際に現場を見ながら考えてみることが一番ではないかと思います。
会議室の中で机上の論議を行うよりも現場に出て3現主義で検討する方がよいアイデアが出ることは間違いありません。ではもう少し具体的に検討していきましょう。
2. 距離短縮と5S改善
物流といえば距離の短縮改善はつきものです。まず物流改善を実感していただくためにも距離の短縮をやってみるとよいかもしれません。輸送改善で距離を短縮することもありますが、まずは倉庫内や工場内でトライをしてみることをお勧めします。
倉庫ではロケーションを変更して運搬距離を短縮してみましょう。そんな難しいことではありません。一つも距離短縮改善の余地が無いという倉庫は無いと思います。ピッキング場での歩行距離の短縮でも構いません。これらの距離改善は明確にコストダウンに効いてきます。これを実感することで改善の楽しさを感じていただきたいと思います。参加メンバーも自分たちの実施した改善で実際にコストが下がったとすればやりがいも出てくるということです。
5S改善も当然のことながら立派な改善です。ロケーションに表示を付けることも大きな前進になると思います。5Sを甘く見る人がいます。5Sをやったところで儲からないだろうと知ったふりをしていますが、5Sは侮れません。これを日々繰り返すだけでも会社は大幅に儲かること間違いありません。コストだけではありません。何よりも品質が大幅に向上するのです。
それもそのはずです。物流では保管が重要な業務ですが、ものがどこに置かれているかを明確化する活動は5Sの一環です。決められた置場にわかりやすい表示を付けることも同様です。その結果として出庫間違いが減ることにつながります。
・・・・・・・・・・・・・
いかがでしょうか。職場が整然とされることで業務エラーも減り、安全衛生も向上します。これほどおいしい改善はありません。このような改善は現場ならではできる技です。とにかく置場を変えてみる、表示を付けてみる、要らないものを捨ててみる、床に線を引いてみる、等々。いくらでもやることが現場には転がっています。その問題を一つひとつ改善していくことを社内で競ってみてもよいかもしれません。
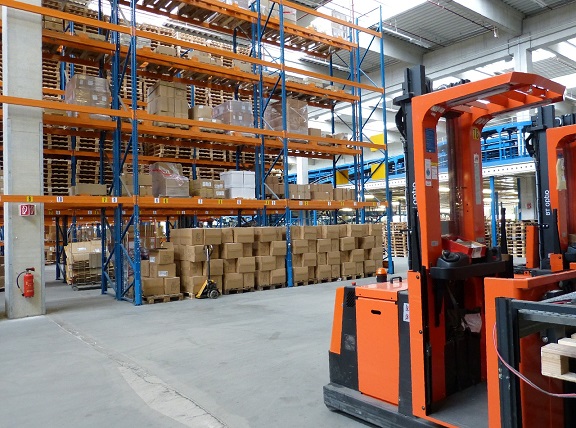
3. 改善実行と経験値の記録
物流担当者の改善力を向上させていくための最短ルートは、実際に現場に出て5S等の改善で職場環境を変えてみる、これを繰り返すことです。
改善するための時間が無いという話を聞くことがありますがそれは本当でしょうか。たしかに仕事を止めないと変更できないようなアイテムがあればそうかもしれません。しかし仕事の合間にものの置き方を変更してみたり作業の手順を変更したりするようなことは可能でしょう。
そして会社の中でこのような改善の結果を記録として残していくことをお勧めします。改善はノウハウです。担当者が変わったとたんにノウハウが消えてしまうことがいかにももったいないと思いませんか?その記録を使って教育していくことも望ましいでしょう。これを繰り返すことで物流改善はみるみると進んでいくことと思われます。
まず第一歩を踏み出すことです。全従業員がその経験をすることが理想的です。そしてこのようなしくみづくりを実施していくのは経営者のタスクです。製造業では歩行一歩を無くすための改善を行っています。...