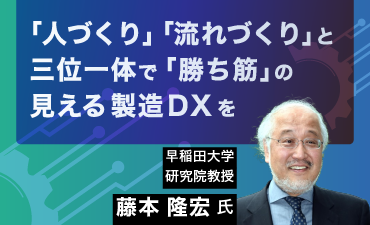
生産性向上に取り組まなければ、生き残れない時代に
早稲田大学 研究院教授 藤本 隆宏 氏
付加価値の良い流れを作る
DXという言葉がよく聞かれる。このような言葉は次々と新しいものが生まれ、すぐに変わってしまうが本質は変わっていない。それは良い流れを作ることであって、トヨタ生産方式を作った大野氏の言葉を借りれば、付加価値の良い流れを作るということになる。
学者の立場から掘り下げると、付加価値は設計情報に宿るという原理がある。トヨタ的な言い方をすれば、良い設計の良い流れ、つまりものづくりとは良い設計の良い流れを作ることだと考えている。現在のスマート工場やDXの話も、あくまでその流れの中にある。ものづくりは流れ作りであり、流れ作りは流れを作れる人づくりだ。したがって、ものづくりは人づくりと言い換えることもできる。人づくりがあり、流れ作りがあり、その上にDXやスマート工場といったものが乗ってくる。そうでなければうまく進めることはできない。
私は工場によく足を運ぶがこれまで、年間で数十カ所、世界中で千何百カ所もの工場を見てきた。流れの良い工場も悪い工場も見てきたが、基本は産業の現場、つまり付加価値の流れが流れている場所の観察から始まり、理論と現場の流れがどう一致するかに注視している。
“DXのためのDX”では失敗する
今日は制御の方が中心だと思うが、現在の日本の製造業のGDPは約557兆円で、この30年間ほとんど伸びていない。そのうち、製造業が占める割合は22%の約122兆円で一見、少なく感じるかもしれないが、G7・主要先進国の中で20%を超えているのはおそらく日本とドイツだけとなる。
この30年間、特に1990年代あたりは、中国の賃金がほぼ1万円だったのに対し、日本の賃金は約20万円だった。20倍もの賃金格差があり、隣には当時2億人もの従業員を抱える製造業が東西の壁崩壊によって突如として現れ「私たちも世界市場に出るのでよろしく」と言ってきたのが1992年頃だ。これは大変なことで、当時から日本は若い人でも大体20万円くらいの賃金だったが、その後は全く上がらなくなる。これは当然のことで、多大な苦労を強いられたわけだが、その割に統計を詳しく確認しないマスコミが「結局、製造業はダメだろう」と言い続けた結果、製造業の人たちまで「マスコミが言っているからダメかもしれない」と誤解してしまい、間違った議論が繰り広げられた。国の統計を見るだけでも、色々なことが分かるので、しっかりと見てほしいものだ。
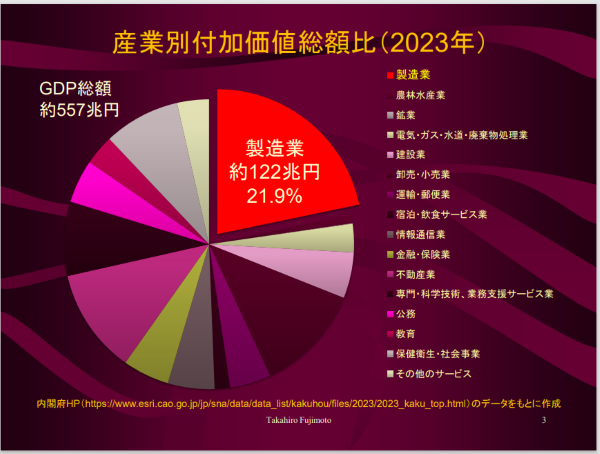
【グラフ】産業別付加価値総額費(2023年・藤本氏提供)
そこで、国の統計を見ながら製造業の30年間を話したい。結論を先に言うと、これからの時代、生産性を上げないと生き残ることができない状況となっている。経済計算上、今までは上げる人はどんどん上げていき、上げない人もなんとか生き残ることができたのがこの30年であったが、これからはそうはいかなくなる。
DXやスマート工場の活用、あるいはデジタル製造でも構わないが、とにかくそういった種のものを当然やらなければならないのだが“DXのためのDX”を進めた企業はみな失敗している。うまく進んでいるところもいくつか見ているが、そういった企業はやはり、流れ作りから入っている。流れ作りから人づくりへ、あるいは人づくりから流れ作りへ進み、そのベースをしっかり固めた上でDXやデジタル技術を取り入れている。たとえば、愛知県のD社や静岡県のW社、Y社など、様々な企業があるが、基本は「流れ作り」、「人づくり」、そして「ある種のデジタル化」が三位一体で動いており、うまく進んでいると実感している。その辺も含め、少し話をしようと思う。
その前に、なぜ生産性の時代になってしまったのか、つまり生産性底上げの時代になってしまったのかという話をしたい。今までは、5年で5倍、10年で8倍といった驚異的な生産性向上を達成した企業も多くあった。たとえば、トヨタ方式を導入して5年で5倍とし、2010年当時ですでに、コストで中国に追い付いたという猛者も日本には多く存在した。このような人たちは黙々と仕事をこなすため、あまり目立たないが、全国でみるとこのような会社は多くあった。また、何も取り組んでいない企業も多くあり、どちらも生き残れたのがこの30年だった。
デフレの中、賃金も価格も売上も上がらない状態が続けば、実は何もしていなくてもわずかな利益で長く続けることができる。全国を歩いてみても、甲府盆地や諏訪、北関東、浜松などで両タイプの会社があった。驚くほど生産性を上げると、今度は余剰人員が出るため、社長が各地を奔走して仕事を取ってくるという、需要創造と生産性向上を同時に行う積極的な素晴らしい企業、中小企業も数多く存在した。日本の製造業はすごいと感心させられるばかりだったが、残念ながらそうでない会社もかなり見受けられた。会社規模は関係なく、少々厳しい会社も多...
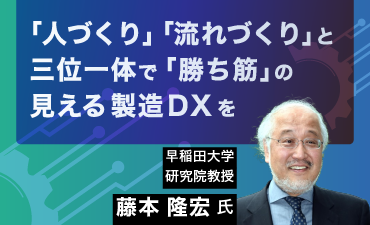
生産性向上に取り組まなければ、生き残れない時代に
早稲田大学 研究院教授 藤本 隆宏 氏
付加価値の良い流れを作る
DXという言葉がよく聞かれる。このような言葉は次々と新しいものが生まれ、すぐに変わってしまうが本質は変わっていない。それは良い流れを作ることであって、トヨタ生産方式を作った大野氏の言葉を借りれば、付加価値の良い流れを作るということになる。
学者の立場から掘り下げると、付加価値は設計情報に宿るという原理がある。トヨタ的な言い方をすれば、良い設計の良い流れ、つまりものづくりとは良い設計の良い流れを作ることだと考えている。現在のスマート工場やDXの話も、あくまでその流れの中にある。ものづくりは流れ作りであり、流れ作りは流れを作れる人づくりだ。したがって、ものづくりは人づくりと言い換えることもできる。人づくりがあり、流れ作りがあり、その上にDXやスマート工場といったものが乗ってくる。そうでなければうまく進めることはできない。
私は工場によく足を運ぶがこれまで、年間で数十カ所、世界中で千何百カ所もの工場を見てきた。流れの良い工場も悪い工場も見てきたが、基本は産業の現場、つまり付加価値の流れが流れている場所の観察から始まり、理論と現場の流れがどう一致するかに注視している。
“DXのためのDX”では失敗する
今日は制御の方が中心だと思うが、現在の日本の製造業のGDPは約557兆円で、この30年間ほとんど伸びていない。そのうち、製造業が占める割合は22%の約122兆円で一見、少なく感じるかもしれないが、G7・主要先進国の中で20%を超えているのはおそらく日本とドイツだけとなる。
この30年間、特に1990年代あたりは、中国の賃金がほぼ1万円だったのに対し、日本の賃金は約20万円だった。20倍もの賃金格差があり、隣には当時2億人もの従業員を抱える製造業が東西の壁崩壊によって突如として現れ「私たちも世界市場に出るのでよろしく」と言ってきたのが1992年頃だ。これは大変なことで、当時から日本は若い人でも大体20万円くらいの賃金だったが、その後は全く上がらなくなる。これは当然のことで、多大な苦労を強いられたわけだが、その割に統計を詳しく確認しないマスコミが「結局、製造業はダメだろう」と言い続けた結果、製造業の人たちまで「マスコミが言っているからダメかもしれない」と誤解してしまい、間違った議論が繰り広げられた。国の統計を見るだけでも、色々なことが分かるので、しっかりと見てほしいものだ。
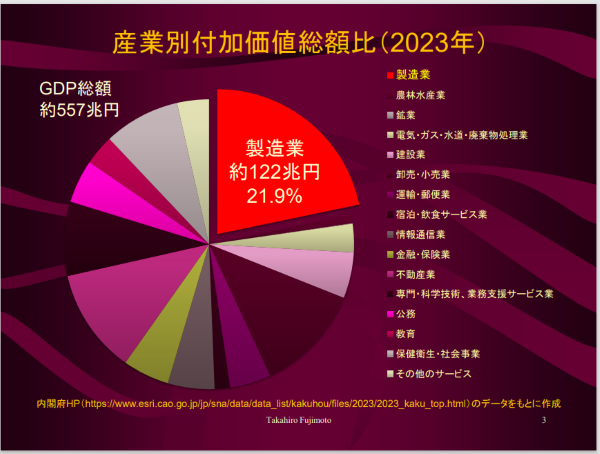
【グラフ】産業別付加価値総額費(2023年・藤本氏提供)
そこで、国の統計を見ながら製造業の30年間を話したい。結論を先に言うと、これからの時代、生産性を上げないと生き残ることができない状況となっている。経済計算上、今までは上げる人はどんどん上げていき、上げない人もなんとか生き残ることができたのがこの30年であったが、これからはそうはいかなくなる。
DXやスマート工場の活用、あるいはデジタル製造でも構わないが、とにかくそういった種のものを当然やらなければならないのだが“DXのためのDX”を進めた企業はみな失敗している。うまく進んでいるところもいくつか見ているが、そういった企業はやはり、流れ作りから入っている。流れ作りから人づくりへ、あるいは人づくりから流れ作りへ進み、そのベースをしっかり固めた上でDXやデジタル技術を取り入れている。たとえば、愛知県のD社や静岡県のW社、Y社など、様々な企業があるが、基本は「流れ作り」、「人づくり」、そして「ある種のデジタル化」が三位一体で動いており、うまく進んでいると実感している。その辺も含め、少し話をしようと思う。
その前に、なぜ生産性の時代になってしまったのか、つまり生産性底上げの時代になってしまったのかという話をしたい。今までは、5年で5倍、10年で8倍といった驚異的な生産性向上を達成した企業も多くあった。たとえば、トヨタ方式を導入して5年で5倍とし、2010年当時ですでに、コストで中国に追い付いたという猛者も日本には多く存在した。このような人たちは黙々と仕事をこなすため、あまり目立たないが、全国でみるとこのような会社は多くあった。また、何も取り組んでいない企業も多くあり、どちらも生き残れたのがこの30年だった。
デフレの中、賃金も価格も売上も上がらない状態が続けば、実は何もしていなくてもわずかな利益で長く続けることができる。全国を歩いてみても、甲府盆地や諏訪、北関東、浜松などで両タイプの会社があった。驚くほど生産性を上げると、今度は余剰人員が出るため、社長が各地を奔走して仕事を取ってくるという、需要創造と生産性向上を同時に行う積極的な素晴らしい企業、中小企業も数多く存在した。日本の製造業はすごいと感心させられるばかりだったが、残念ながらそうでない会社もかなり見受けられた。会社規模は関係なく、少々厳しい会社も多くあったが、それでも生き残れていた。
確かに製造業の数はこの30年で半分くらいに減ってしまったが、残っているところは残っている。しかも、全体で見ると、GDPに占める製造業の付加価値の割合は20%程度で約120兆円となる。1990年から見てみると、中国や韓国、アメリカのデジタル材の成長と比べると情けないほどの低成長だが、決して衰退しているわけではない。「日本は空洞化した」、「昔の製造業はすごかったが今はダメだ」と話している人たちは国の統計を見ず、言っているに過ぎない。
1990年代、日本の製造業就業者数は1,500万人だったのに対し、中国は約2億人だった。現在は減り始めているがそれでも3億人が働いている。ハンデが20倍あったころ、つまり日本の若者の賃金が20万円、中国は1万円だが、生産性同様の中国の工場に対し、生産性10倍でも負けてしまうため、どうしてもリストラせざるを得ないというプレッシャーがものすごくあったわけで、残念ながら就労者も1,500万人から1,000万人に減っていった。日本の就業者数自体はそんな減っていないため、非製造業に500万人ぐらいが移ったことになる。当然、非製造業の方が生産性も賃金も低いため、日本全体として賃金が上がらない状況になった。製造業だけをみれば、そんなに悪かったわけではない。今や日本の製造業は1,000万人で支えている一方、対する中国は3億人ぐらいと思われる。つまり、中国の製造業と正面から戦うなんて話ではない。これから、国際的な製造業は得意なところに特化し、勝負していくことになると考える。
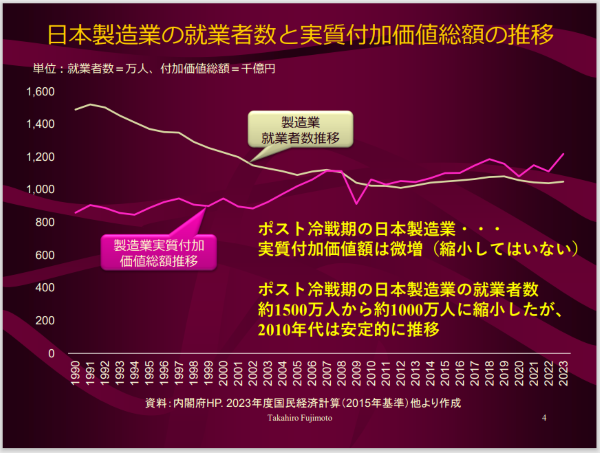
【グラフ】日本製造業の就業者数と実質付加価値総額の推移・1990~2023年(同氏提供)
一人1年間あたりの付加価値生産性推移をみると、製造業は30年で600万円から約1,200万円にまで上がっている。これは、町工場をはじめ、地場の工場から中小企業、トヨタの工場など、すべてを含めた平均となる。ほとんど、非製造のように全く生産性が上がっていないが、雇用は続けている。私は、利益もほとんどなく、不況で調子が悪くなったら雇用調整助成金でつないでいるといった製造業をたくさん見てきているが、実はこの半分ぐらいの製造業の平均は非製造業に近いような数字になってしまっているのかもしれない。そうすると、仮に半々とすれば、頑張った工場の付加価値生産性はこの数値の2倍、3倍程度のスピードで上がっており、それぐらい差が出てしまっているとみている。しかし、日本の生産性は低いかもしれないが、それは非製造業に引っ張られているだけであって、製造業だけをみれば悪い数値ではないことが分かる。生産性も2倍となっており、伸びている企業はこれよりもはるかに速いスピードで付加価値を上げていっていると思う。
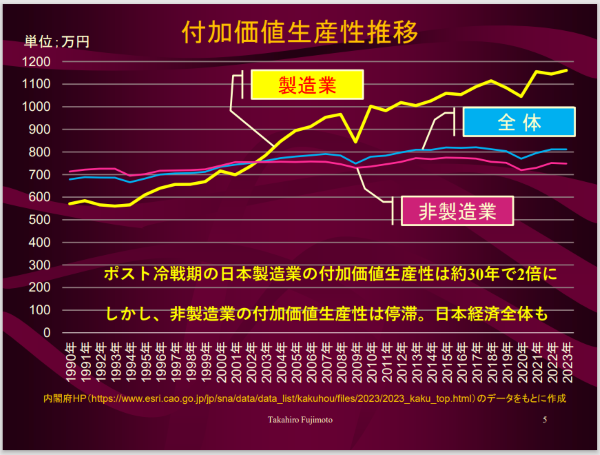
【グラフ】付加価値生産性の推移・1990~2023年(同氏提供)
ものづくり現場DX DAY 2025記事一覧へ戻る
良い設計で付加価値率を上げ、喜んで買ってもらえる価格設定を
付加価値生産性は価格×付加価値×物的労働生産性で算出できる。物的労働生産性を上げるというのは、まさにトヨタ方式の世界だ。ラインによっては5年で5倍、10年で8倍など、すさまじい取り組みを進め、生き残ってきた。ただ、一生懸命に物的労働生産の向上、つまり生産改善を進めても、場合によっては浮かばれないケースもある。なぜかというと、商売改善と設計改善の二つがついてこないからだ。去年、岐阜県内で粉砕機を作っている老舗企業を訪ねた。30人程度の中小企業だが、電気自動車関係で大量の需要があり売り上げも十何億だった。名前は出さないが、確実にこのような会社が存在しており、日本国内にも同様の企業は多数ある。
付加価値生産性は、価格から直材費引いたものであるため、直材費を節約していく、つまりトヨタ的に言えばバリューエンジニアリングに当たり、この部分で良い数字が出ると思ったら設計改善を行う。次に一番左側の価格だが、価格を上げていけば付加価値も上がっていく。ただ、設計上、何も改善も行わず、お客を全く喜ばせることもないまま、価格だけが上がっていく“価格転嫁”は許されるものではない。仮に日本の場合、設計はほっといても良くなっていく。設計が良くなった分ぐらいは、お客から喜んで払ってもらえる金額で買っていただくといった流れになれば、設計が良くなっていくということは価格も少しずつ上がってくる。自動車に例えると、私の感覚では昔、200万円で買えた自動車が今は300万円となっている。それでも世界中で1億人の人たちが平均300万円の価格でも買ってくれている。つまり、それは納得して買っているわけであって、良い流れで物的労働生産性を上げていくと同時に、良い設計で付加価値率を上げ、価格を上げる。つまりお客さんが喜んで買ってもらう物を作っていることとなる。自動車の場合、これができているため、自動車の付加価値生産性は比較的良い結果が出ている。一方、家電になると価格の据え置きであったり、中国と競う中、強気の価格設定で挑んだため、結局うまくいかなかった。そのような中でもたとえば、ドラム式洗濯機は設計も素晴らしく、価格も30万円以上するが売れていることをみても、お客が本当に喜ぶ設計を行い、それを喜んで買ってもらえる価格設定をしなければならない。ここで据え置きのまま進めてしまうと、無駄な値下げとなり、デフレ状態を生み出した。
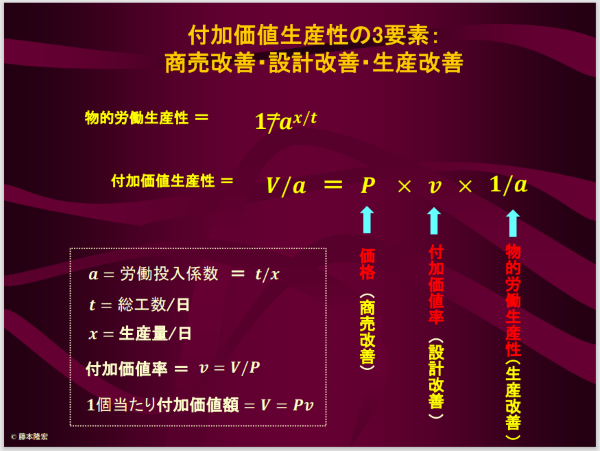
【図】付加価値生産性の3要素(同氏提供)
商売改善、設計改善、生産改善の3つが頑張り、会社中が一丸となって初めて付加価値生産性が上がる。そして、付加価値生産性が高ければ賃金も上げられ、雇用も守ることができる。また、社会貢献費用の捻出、設備投資、アブランディ投資も可能となるため、とにかく生産性を上げることに注目すべきと考えている。
最近は、付加価値生産性に注目する人たちが増えてきており、良い傾向にあると思っている。日本全体が赤字になったといった話になると、日本の貿易赤字は製造業が弱いからだと言う人がいるが、事実ではないので気にしないでほしい。
みなが生産性向上に取り組まなければ、生き残れない時代に
工業製品貿易収支の推移をみると、実は輸出額が史上最高であることが分かる。かつて無敵と言われた1990年頃の工業製品輸出額は約40兆円だったが、現在は約100兆円を記録している。自動車関連が占める割合が大きいが、それ以外の分野でも輸出している企業は多く存在する。ただし、工業製品を中心に輸入が増加しており、中国以外にアメリカのソフトウェアなども含めると、日本は大量に輸出し、大量に輸入している国となっている。そうなると、何が得意で何が苦手なのかを考える必要が出てくる。一次産品の価格上昇が貿易赤字の要因であるのは事実であって、工業製品が弱くなったから赤字になったという話は全くのうそだ。
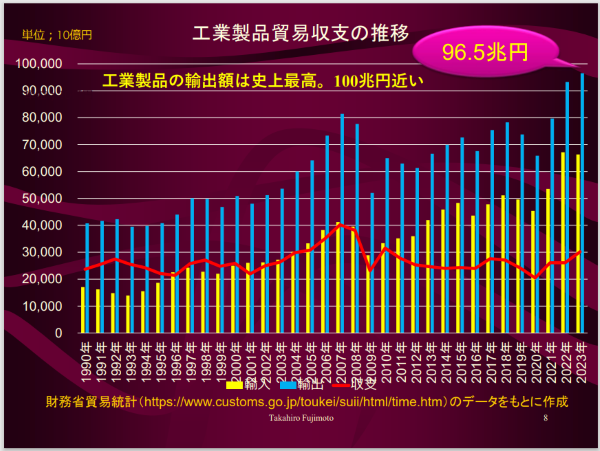
【グラフ】工業製品貿易収支の推移・1990~2023年(同氏提供)
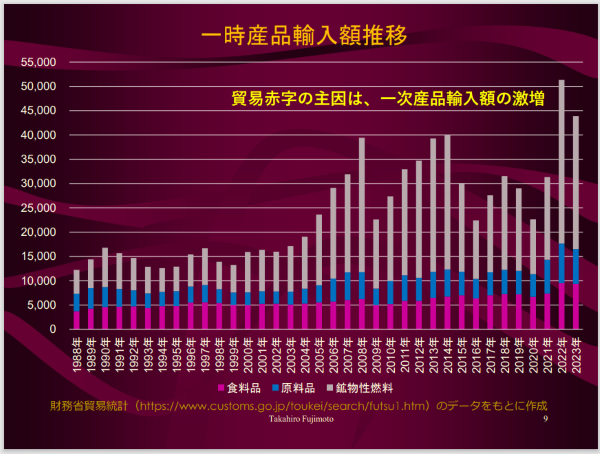
【グラフ】一次産品輸入額の推移・1990~2023年(同氏提供)
これからも、賃上げの基調はしばらく続くと考えられる。物価・賃金・価格のスパイラルと、賃金・生産性サイクル二つの要因が働いているからだ。1992年は中国が世界市場に参入した年で、当時の中国の賃金は若手中心に約1万円、日本は約20万円だった。中国の参入後、日本の賃金は上がらなくなったが、これはどうみても中国に因果関係があるといえる。ここから30年続くわけだが近年、ようやく上がり始めており、長く続いたデフレの時代が終わりつつある。デフレが終わるとどうなるのかというと、生産性向上しかない時代となり、賃金が上がり続けると、生産性を上げなくてもなんとか生き残れた企業は生き残れなくなる。競争が激しく、賃金が上がっても価格を上げられない状況では、労働生産性を上げるしかない。30年ぶりにみんなが生産性向上に取り組まなければいけない時代になった。
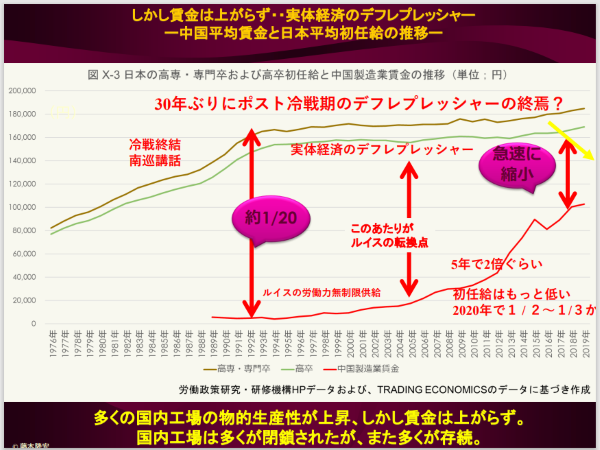
【グラフ】日本の高専・専門卒および高卒初任給と中国製造業賃金の推移・1976~2019年(同氏提供)
私は20年間、東京大学で生産性向上のインストラクター育成に努めていた。様々な場所で指導してきたが、分かったことは、生産性向上と需要創造に積極的な企業とそうでない企業が存在し、両方とも同じ地域で生き残れた30年だった。しかし、もうそうはいかないと考えている。
これから、生産性向上に取り組めないところは淘汰される。価格転嫁できる緩い産業にいればラッキーだが、厳しい産業で生産性を上げられない、上げたくないと言っていると、地域全体で生産性向上に取り組む時代となったため、生き残ることはできない。我々は腹をくくって色んなことに取り組む必要があるが、まず改善マインドが浸透していないところは難しくなる。いきなりDXのためのDXに取り組んでも失敗することは目に見えている。言い方がかっこいいからDXに取り組むのではなく、もっと根本的なところから入っていく必要がある。
これまでも、改善意識を持つ企業は多く見てきたが、残念ながら自分の目の前の工程しか見ておらず、全体の流れを意識できていないところが多かった。全体の流れを良くしなければ給料は上がらない。流れが良くならないのに「生産性を上げたのに給料が上がらない」というのは当然だ。
本日、旭鉄工の木村さんも話されていたが、旭鉄工は最初から流れに集中してDXを進めていた。現状維持志向の人が多く、負け癖がついている工場や企業が多いのも事実で、これをなんとかしなければならない。今、一番のライバルは中国やアメリカではなく、自分の中にある負け癖を克服できるかどうかだと思う。そのためにも、監督層、スマートファクトリー時代の改善リーダー層の育成が重要だ。まずは改善意識を持ってもらい、現場で因果関係を突き詰める「現場サイエンティスト」を育てると同時にデジタル教育を行い、改善の先頭に立ってもらいたい。しかし、こういう人たちは潰されやすいので、上の人たちがしっかり管理していかなければならない。
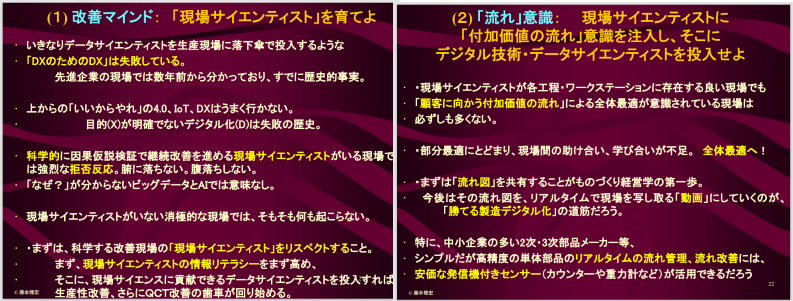
【図】改善意識を持ってもらい、現場で因果関係を突き詰める「現場サイエンティスト」を育てると同時にデジタル教育を(同氏提供)
「勝ち筋の見えるデジタルものづくり」、それは、話の繰り返しになるが、まず競争優位を確立すること。「流行っているからDXをやりました」では必ず失敗する。まずはどうやったら勝てるのかという勝ち筋を読み切ることが重要で、それを支えるのは、付加価値の流れ作りや設計情報の流れ作りであって、そこを徹底的に取り組むことが重要となる。流れを作ることを忘れ、箱物(システム)中心のDXや改善意識を高めていないDXでは失敗してしまう。また、人づくりも重要で、人づくりと流れ作りを両立させなければならない。せっかく若手の人たちが頑張っていても、周りが冷ややかな目で見て潰してしまう例も残念ながらあるため、モチベーションを下げるようなDXも潰すべきだ。
取り組みが楽しい、改善サイクルが速く回る、会社に来て工場で働くのが面白い、そして賃金も上がっていく。このあたりを目指し、三位一体のデジタル化ができている企業が成功している。積極的な企業や消極的な企業が生き残れた時代は終わり、経済計算上、生産性向上に取り組まなければ長期的に生き残れない時代が来た。ここは腹をくくって、三位一体で良い流れを作り、良い流れから生産性向上へ持っていくことが、勝ち筋だと私は考えている。
ものづくり現場DX DAY 2025記事一覧へ戻る