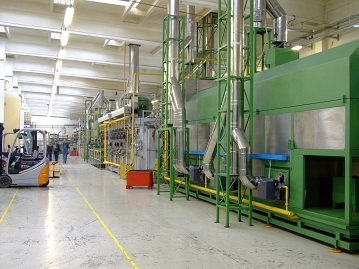
なぜTPMなのか?この記事では、急速に産業界に広がるTPMについて、TPMの定義について学び、その基本的な考え方、そのねらいをとらえて解説します。また、TPMの実際の進め方として小集団活動の重要性も述べます。
トランスファーマシンや電子制御など、いわゆるメカニカルオートメーションの進化にともない保全費は増大しています。さらに更新設備投資費の抑制のために、老朽化した設備の有効活用にかかる保全費と保全工数が増え続けているのが実状ではないでしょうか。今やTPMの導入は不可欠です。
予防保全は部品の交換周期を決めて、早めに交換し設備停止にならないようにする手法です。従って、交換周期が実績データに基づく適正なものでないと、故障しなくても交換することになってしまいます。予知保全は下記の手順で実施します。
- 数値パラメータによる連続監視をする。
- 設定したパラメータ(例えば温度等)がある一定の水準に到達したら設備が故障に至るか経験則により、その水準値を定める。
- 監視データに基づき水準値に到達したときに設備のどの部分を修理又は部品交換するが標準化する。
このように予知保全では監視機器などが必要になるため予知保全のための初期コストはかかりますが、有効な予知保全にすると設備を故障する寸前まで使用し、設備停止の管理ができる有効な手法です。
関連記事:TPM、総合生産的な保全とは
1. TPMの思想
結果の管理に没頭していては、儲からない会社になります。
発生している問題は氷山の一角です。潜在している問題も含めて、再発防止、予防できる体制、仕組みに変えることが重要です。儲ける仕事の仕方は未然防止にあるのです。
QC活動はロスを減らす活動であり、品質を対象とします。不良が発生してから分析、対策、改善 を実施しているので、不良がゼロになることはありません。
TPM活動の思想はロス発生前の活動であり、設備を対象として不良が発生する前に分析、対策、改善をする攻めの活動です。TPM活動の思想で不良をゼロにする事が可能になります。
2. TPMの種類
・TPM(Total Productive Maintenance)経営用語 総合的設備管理
企業の継続的繁栄の基礎条件を確立する事を目的にした、新しい経営モデルを構築する手段の事。
・TPM(Trusted Platform Module) IT、コンピューター用語 トラステッドプラットフォームモジュール
コンピュータのマザーボードに直付けされているセキュリティに関する各種機能を備えたデバイスもしくはチップの事。
本稿ではTPM(Total Productive Maintenance)について取り扱います。
3. TPM(Total Productive Maintenance)とは
日本語では総合的設備管理と表される経営用語です。
TPMは企業などにおいて、製造設備の保守管理を総合的に行い、設備停止時間の減少を目指し、生産性の向上を計る活動です。
4. TPMの歴史
1971年に日本プラントメンテナンス協会(...
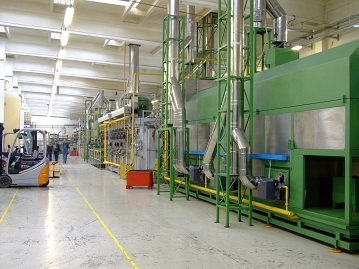
なぜTPMなのか?この記事では、急速に産業界に広がるTPMについて、TPMの定義について学び、その基本的な考え方、そのねらいをとらえて解説します。また、TPMの実際の進め方として小集団活動の重要性も述べます。
トランスファーマシンや電子制御など、いわゆるメカニカルオートメーションの進化にともない保全費は増大しています。さらに更新設備投資費の抑制のために、老朽化した設備の有効活用にかかる保全費と保全工数が増え続けているのが実状ではないでしょうか。今やTPMの導入は不可欠です。
予防保全は部品の交換周期を決めて、早めに交換し設備停止にならないようにする手法です。従って、交換周期が実績データに基づく適正なものでないと、故障しなくても交換することになってしまいます。予知保全は下記の手順で実施します。
- 数値パラメータによる連続監視をする。
- 設定したパラメータ(例えば温度等)がある一定の水準に到達したら設備が故障に至るか経験則により、その水準値を定める。
- 監視データに基づき水準値に到達したときに設備のどの部分を修理又は部品交換するが標準化する。
このように予知保全では監視機器などが必要になるため予知保全のための初期コストはかかりますが、有効な予知保全にすると設備を故障する寸前まで使用し、設備停止の管理ができる有効な手法です。
関連記事:TPM、総合生産的な保全とは
1. TPMの思想
結果の管理に没頭していては、儲からない会社になります。
発生している問題は氷山の一角です。潜在している問題も含めて、再発防止、予防できる体制、仕組みに変えることが重要です。儲ける仕事の仕方は未然防止にあるのです。
QC活動はロスを減らす活動であり、品質を対象とします。不良が発生してから分析、対策、改善 を実施しているので、不良がゼロになることはありません。
TPM活動の思想はロス発生前の活動であり、設備を対象として不良が発生する前に分析、対策、改善をする攻めの活動です。TPM活動の思想で不良をゼロにする事が可能になります。
2. TPMの種類
・TPM(Total Productive Maintenance)経営用語 総合的設備管理
企業の継続的繁栄の基礎条件を確立する事を目的にした、新しい経営モデルを構築する手段の事。
・TPM(Trusted Platform Module) IT、コンピューター用語 トラステッドプラットフォームモジュール
コンピュータのマザーボードに直付けされているセキュリティに関する各種機能を備えたデバイスもしくはチップの事。
本稿ではTPM(Total Productive Maintenance)について取り扱います。
3. TPM(Total Productive Maintenance)とは
日本語では総合的設備管理と表される経営用語です。
TPMは企業などにおいて、製造設備の保守管理を総合的に行い、設備停止時間の減少を目指し、生産性の向上を計る活動です。
4. TPMの歴史
1971年に日本プラントメンテナンス協会(のちの日本プラントメンテナンス協会)により提唱されたもので、米国のPM(Productive Maintenance)を起点に日本独自で生み出された手法です。
1971年にトヨタ自動車のグループ企業である日本電装(のちのデンソー)がTPM推進団体である日本プラントメンテナンス協会のPM賞を受賞したことをきっかけにトヨタ自動車グループ各社からTPM普及が始まり、協力会社も含めた広い範囲でのTPM推進が始まりました。
TPMが国内外で普及した背景
TPMは、製造業の生産性を向上させるための手法として日本で発展しました。では、なぜこれが世界中で広まったのでしょうか。以下に主な理由を説明します。
1. 日本の製造業の成功
1970年代、日本の製造業は高品質の製品を低コストで生産する能力を持っていました。これが、世界中の企業の注目を集め、その秘訣としてTPMが浮上しました。
2. 全員参加型のアプローチ
従来の保全手法はエンジニアや技術者が中心でしたが、TPMは「全員が参加」することを重視。これにより、組織全体の力で生産設備の問題を解決する文化が根付きました。
3. JIPMのプッシュ
日本の生産保全協会(JIPM)は、TPMの普及のためのリーダーシップをとった。彼らのガイドラインや認定制度は、企業がTPMを導入する際のスタンダードとなりました。
4. リーン生産とのシナジー
TPMは、リーン生産システムやトヨタ生産方式(TPS)と相性が良い。これらの生産効率改善手法と組み合わせることで、より大きな効果を引き出すことができます。
5. 全員参加の文化の普及
グローバル化の進展とともに、多くの企業が「全員参加」の文化の重要性を認識。TPMは、その理念を具体的に実践する手法として受け入れられました。
TPMに関する今後の展望
TPM(Total Productive Maintenance)は、製造業の中で非常に成功した生産効率向上手法として広まってきました。しかし、現代のデジタル変革の波を受けて、TPMも進化しつつあります。今後の展望を以下に整理します。
まず、IoT(Internet of Things)の導入がTPMの未来を大きく変える要因となるでしょう。製造機械や設備がネットワークに接続されることで、実際の動作データや状態をリアルタイムで収集することが可能になります。これにより、機械の故障を予測する「予知保全」が進化し、生産のダウンタイムをさらに削減することが期待されます。
次に、AI(人工知能)の活用が進むでしょう。データ分析の能力を持つAIは、膨大な量のデータから異常の兆候や最適な保全タイミングを予測します。また、過去のデータから最適な生産条件を学習し、品質の向上や生産効率の最適化に貢献することが期待されます。
さらに、AR(拡張現実)やVR(仮想現実)技術の活用も拡大する可能性があります。
例えば、ARグラスを使用して、作業者がリアルタイムで設備の情報や修理手順を表示させることで、迅速かつ正確な保全作業をサポートするシステムが普及してくるでしょう。
しかし、これらの技術の導入は、新しいチャレンジももたらします。データのセキュリティやプライバシーの問題、高度な技術スキルの必要性、そして新しい技術への適応能力を持つ人材の育成など、企業にとっては大きな課題となることでしょう。
結論として、TPMはこれからも製造業の中心的な役割を果たしつつ、デジタル技術の導入と統合によって新しい局面を迎えるでしょう。この変革を成功させるためには、従来のTPMの考え方を継承しつつ、新しい技術や手法を柔軟に取り入れる姿勢が求められます。
5. TPMとPMの違い
PMという言葉は米国から日本に入ってきた頃(1950年頃)には、予防保全(Preventive Maintenance)の意味で使われていた。
その後、1960年頃までの間に、日本は米国からにかけてこの予防保全に続き、
- 改良保全(CM:Corrective Maintenance)
- 保全予防(MP:Maintenance Prevention)
- 信頼性工学(Reliability Engineering)
- 保全工学(Maintenability Engineering)
など数多くの手法や理論が入ってくるなかで、米国流PMが日本に普及しました。
このような米国流のPMとは別に、日本流に工夫を加えて、日本式PMともいえる手法として生み出されたのが、TPM(Total Productive Maintenance)であると言えます。TPMは日本で生み出した日本独特の全社的設備管理方式ですが、それ以前に米国から日本へ入ってきたPM手法がベースになっています。
6. TPMの特徴
TPMの特徴は以下の通りです。
・トップから第一線まで全員で参加する全社活動である点
・オペレーターの自主保全を重要視している点
7. TPMの内容
TPMは、設備の効率を最高にすることを目標にして、設備のライフサイクルを対象としたPM(予防保全)のトータルシステムを確立し、設備の計画部門、保全部門、使用部門などのあらゆる部門にわたって、経営陣から第一線従業員にいたるまで全員が参加し、動機づけ管理(小集団活動※(参考))によりPM(予防保全)を推進する事をいいます。
参考記事:OEE(設備総合効率)とは
- 個別改善(ロス削減を目的にした設備の改善)
- 自主保全(オペレーターによる保守作業取り組みによる保全業務の分担)
- 計画保全(保守作業の適切なスケジュール管理)
- 教育訓練(保全技能に関する教育と訓練)
- 初期管理(開発・設計段階での手順の明確化)
- 品質保全(設備の保守管理による製品の品質確保)
- 管理間接部門活動(事務部門や開発部門の生産部門への支援など)
- 安全・環境管理(無事故・無災害・環境への配慮)
参考:小集団活動
QC(Quality Control)サークルとも表現される企業内の活動です。
基本的には3〜7人ほどでグループを作成して、共通のテーマや議題となる話題を決めて、メンバーで話し合いをしながらプロジェクトを進行し、改善を進めて行く活動です。
8. まとめ
TPM(Total Productive Maintenance)の取り組みは、現代の生産設備の複雑さや高度なオートメーションに対応するための重要な手段となっています。
メカニカルオートメーションの発展による保全費の増大や老朽化した設備の有効活用の必要性は、TPM導入の背景として浮き彫りにされています。
予防保全と予知保全の2つのアプローチは、設備の継続的な運用とその長寿命化を目指すもので、それぞれの特性や実施手法によって、設備停止のリスクを最小化することが目的とされています。
特に予知保全は、最新の監視技術を利用して設備の予期せぬ停止を防ぎ、生産効率の最大化を追求します。TPMの取り組みを始める際には、明確な方針や目標の設定が欠かせない要素として位置付けられています。
このような背景を持つTPMは、企業が持続的な競争力を維持するための鍵となる戦略的取り組みと言えるでしょう。