不具合対策書・不具合報告書、クレーム対策書など、呼び方は様々ですがその内容書き方、手順について解説します。作成するに当たっては、その前提である是正処置の意味について、良く理解する必要があります。
▼さらに深く学ぶなら!
「クレーム対策書」に関するセミナーはこちら!
※本記事を執筆した専門家「濱田金男」が提供するセミナー一覧はこちら!
1. そもそも対策書とは?
正しい品質対策書・クレーム対策書とは何でしょうか。
クレーム対策書を見れば、その工場の品質管理レベルが分かります。クレーム対策書を作成するには、いくつかの前提条件をクリヤしないと正しい対策ができません。作成に当たって品質管理の基本を理解する必要があります。又、問題解析手法、未然防止の手法を理解する必要があります。対策書フォーマットを準備しただけでは、それを正しく埋めることはできません。
不良や、クレームの発生を抑えるには、最初に直接の原因(因果関係)を解明し対策します。例えば、加工機械の精度が不足したために、加工寸法が規格外となったとします。対策は、その原因となったその加工機械での加工をやめ、精度の高い加工機械で加工するように変更します。
次に、管理上の原因(しくみの不備)を解明し対策します。なぜ、加工精度の不足する加工機械で加工したのか?が問題となります。これは、品質管理(未然防止)が正しく行われていなかったことになります。
では、未然防止のしくみとはどのようなものでしょうか?そしてそのしくみは、どのような手順で、いつ、だれが責任をもって運用すれば、「加工寸法規格外」は防げるのでしょうか?
原因を究明するには、事実の把握が必須です。現場の状況、現物をよく観察し、現状を把握します。この作業は経験と知識を要します。決してブレーンストーミングなどの思い付きに基づく原因の特定を行ってはなりません。
そして原因が特定できたら、次に未然予防のしくみを適用し、適切な加工機械で、正しく加工し、継続的に品質が維持できるよう管理することが求められます。このように、クレーム対策書を作成するには、上記の前提条件(現場の物理的原因究明と対策、しくみの原因究明と対策)を実施して、はじめて満足できる対策書が書けるのです。
2. クレーム対策書の位置づけ
ISO9000の要求事項である「
是正処置」では「文書化された手順」が求められています。その手順は次のようであり、不適合が発生したら、同じ不適合が二度と起こらないように、不適合の発生原因を取り除く処置のことと規定しています。
- 不適合(顧客の苦情を含む)の内容確認
- 不適合の原因の特定
- 不適合の再発防止を確実にするための処置必要性の評価
- 必要な処置の決定および実施
- 処置の結果の記録
- 是正処置において実施した活動のレビュー
クレーム対策書は「処置の結果の記録」と位置付けられます。顧客から要求があろうとなかろうと、ISO9000では、結果を記録してそれを残しなさいと規定しているのです。
3. 是正処置の目的
是正処置の目的を考えてみましょう。単なる「処置」だけの場合、結局「モグラたたき」で終わってしまい、その時だけ(或いはその物だけ)の処理で終わってしまうので、暫くするとまた不適合が再発してしまいます。是正処置とは再発防止のために、不適合の原因を除去する処置であり、モグラを全滅させると同時に二度ともぐらが入って来ないように仕掛けを行う作戦のことです。
しかし、実際に行われる是正処置は不適合を取り除くだけ、つまり、もぐらを叩いて終わりにしている場合が多いのです。例えば人がミスをした時「ミスをしたのは仕方ない、次からは気を付けるように」と終わりにしてしまいます。これでは、是正処置を行ったことにはなりません。不適合の原因を除去する処置が出来ていないのです。
4. 人的ミスの原因と是正処置
是正処置とは再発防止のために不適合の原因を除去する処置であり、そこにいるモグラを全滅させ、さらにもう二度と現れないようにすることです。例えば人的ミスとして、モノを間違って梱包して、顧客に届けてしまったため発生した顧客クレームは、たまたま処理していたその作業者にすべての原因があるでしょうか?人が起こすエラー、単純ミス(ポカミス)の...
不具合対策書・不具合報告書、クレーム対策書など、呼び方は様々ですがその内容書き方、手順について解説します。作成するに当たっては、その前提である是正処置の意味について、良く理解する必要があります。
▼さらに深く学ぶなら!
「クレーム対策書」に関するセミナーはこちら!
※本記事を執筆した専門家「濱田金男」が提供するセミナー一覧はこちら!
1. そもそも対策書とは?
正しい品質対策書・クレーム対策書とは何でしょうか。
クレーム対策書を見れば、その工場の品質管理レベルが分かります。クレーム対策書を作成するには、いくつかの前提条件をクリヤしないと正しい対策ができません。作成に当たって品質管理の基本を理解する必要があります。又、問題解析手法、未然防止の手法を理解する必要があります。対策書フォーマットを準備しただけでは、それを正しく埋めることはできません。
不良や、クレームの発生を抑えるには、最初に直接の原因(因果関係)を解明し対策します。例えば、加工機械の精度が不足したために、加工寸法が規格外となったとします。対策は、その原因となったその加工機械での加工をやめ、精度の高い加工機械で加工するように変更します。
次に、管理上の原因(しくみの不備)を解明し対策します。なぜ、加工精度の不足する加工機械で加工したのか?が問題となります。これは、品質管理(未然防止)が正しく行われていなかったことになります。
では、未然防止のしくみとはどのようなものでしょうか?そしてそのしくみは、どのような手順で、いつ、だれが責任をもって運用すれば、「加工寸法規格外」は防げるのでしょうか?
原因を究明するには、事実の把握が必須です。現場の状況、現物をよく観察し、現状を把握します。この作業は経験と知識を要します。決してブレーンストーミングなどの思い付きに基づく原因の特定を行ってはなりません。
そして原因が特定できたら、次に未然予防のしくみを適用し、適切な加工機械で、正しく加工し、継続的に品質が維持できるよう管理することが求められます。このように、クレーム対策書を作成するには、上記の前提条件(現場の物理的原因究明と対策、しくみの原因究明と対策)を実施して、はじめて満足できる対策書が書けるのです。
2. クレーム対策書の位置づけ
ISO9000の要求事項である「
是正処置」では「文書化された手順」が求められています。その手順は次のようであり、不適合が発生したら、同じ不適合が二度と起こらないように、不適合の発生原因を取り除く処置のことと規定しています。
- 不適合(顧客の苦情を含む)の内容確認
- 不適合の原因の特定
- 不適合の再発防止を確実にするための処置必要性の評価
- 必要な処置の決定および実施
- 処置の結果の記録
- 是正処置において実施した活動のレビュー
クレーム対策書は「処置の結果の記録」と位置付けられます。顧客から要求があろうとなかろうと、ISO9000では、結果を記録してそれを残しなさいと規定しているのです。
3. 是正処置の目的
是正処置の目的を考えてみましょう。単なる「処置」だけの場合、結局「モグラたたき」で終わってしまい、その時だけ(或いはその物だけ)の処理で終わってしまうので、暫くするとまた不適合が再発してしまいます。是正処置とは再発防止のために、不適合の原因を除去する処置であり、モグラを全滅させると同時に二度ともぐらが入って来ないように仕掛けを行う作戦のことです。
しかし、実際に行われる是正処置は不適合を取り除くだけ、つまり、もぐらを叩いて終わりにしている場合が多いのです。例えば人がミスをした時「ミスをしたのは仕方ない、次からは気を付けるように」と終わりにしてしまいます。これでは、是正処置を行ったことにはなりません。不適合の原因を除去する処置が出来ていないのです。
4. 人的ミスの原因と是正処置
是正処置とは再発防止のために不適合の原因を除去する処置であり、そこにいるモグラを全滅させ、さらにもう二度と現れないようにすることです。例えば人的ミスとして、モノを間違って梱包して、顧客に届けてしまったため発生した顧客クレームは、たまたま処理していたその作業者にすべての原因があるでしょうか?人が起こすエラー、単純ミス(ポカミス)の背後には下記のような要因が考えられます。
- 作業不慣れ
- 一度に記憶できる量の限界
- 中断作業からの復帰(昼休み、電話応対、来客など)
- 分かりにくい表示・名称・類似サイズなど
- 集団圧力(間違っていると思いつつ集団の行動に従うこと)
- 作業環境の悪さ(温湿度、明るさなど)
またモノ違いがその作業に不慣れな新人で、教育・訓練不足にあったと仮定すると次のような要因が考えられます。
- 教育後のスキル判定方法の不備
- 教育・訓練担当者の教え方のばらつき
- 教育・訓練計画と実績管理の不備
作業ミスが多発するのは、そこに多くの管理的な要因が絡んでいると考えられます。適切な教育訓練、現場でのOJTにより、知識不足、スキル不足によるミスは発生しなくなります。しかし、教育訓練では防ぐことができないミス(ポカミス)もある一定の確率で発生します。作業の熟練者でもポカミスは発生します。下表は、作業ミスの2つのタイプと4つの要因と解決策を表しています。
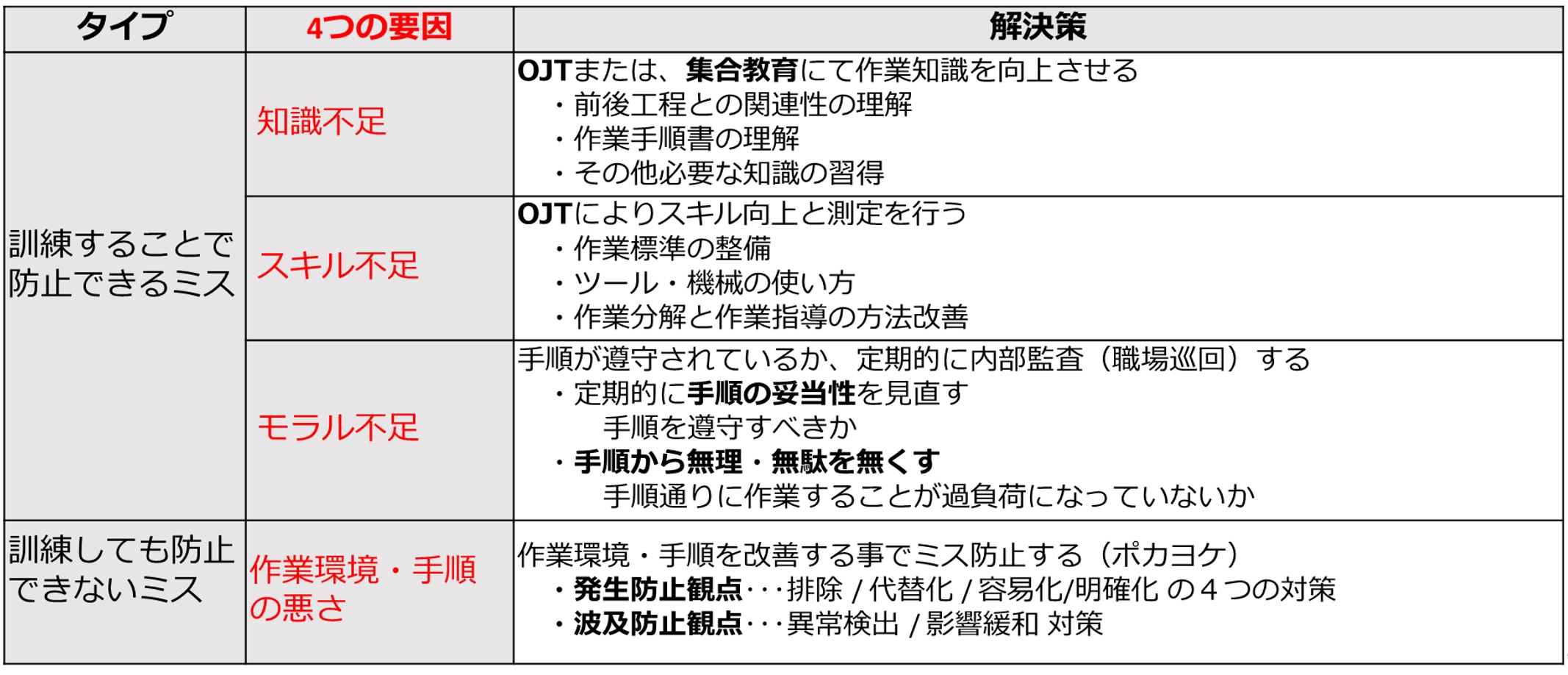
このことを踏まえたうえで、『誰の責任で、何を、いつまでに、どのように行うのか』という管理の基本を明確に既定しておく必要があるのです。不適合発生に至った管理のしくみの不備や欠陥を突き止め対策することが正しい「是正処置」なのです。ちなみに「予防処置」は、あらかじめ物事を行う前に、不適合を予測してそれが発生しないように対策を講じておくことを言い、行動開始後に発生した不適合に対する「是正処置」とは区別されます。
5. クレーム対策書の書き方
以上のことを理解した上で対策書を作成します。顧客から求められて作成する場合もありますが、社内においても再発防止の目的で関係者と情報共有を行い周知徹底を図ること、また対策の経緯を文書で残す事でノウハウの蓄積と共有化につながり、固有技術力と管理技術力の向上にも寄与します。では、具体的な作成手順と注意点を下記の事例研究1に沿って説明します。対策書は「なぜ起こったのか」そのメカニズムと「なぜ防げなかったのか」管理の不備を指摘し、その2段階の原因と対策内容を記入します。
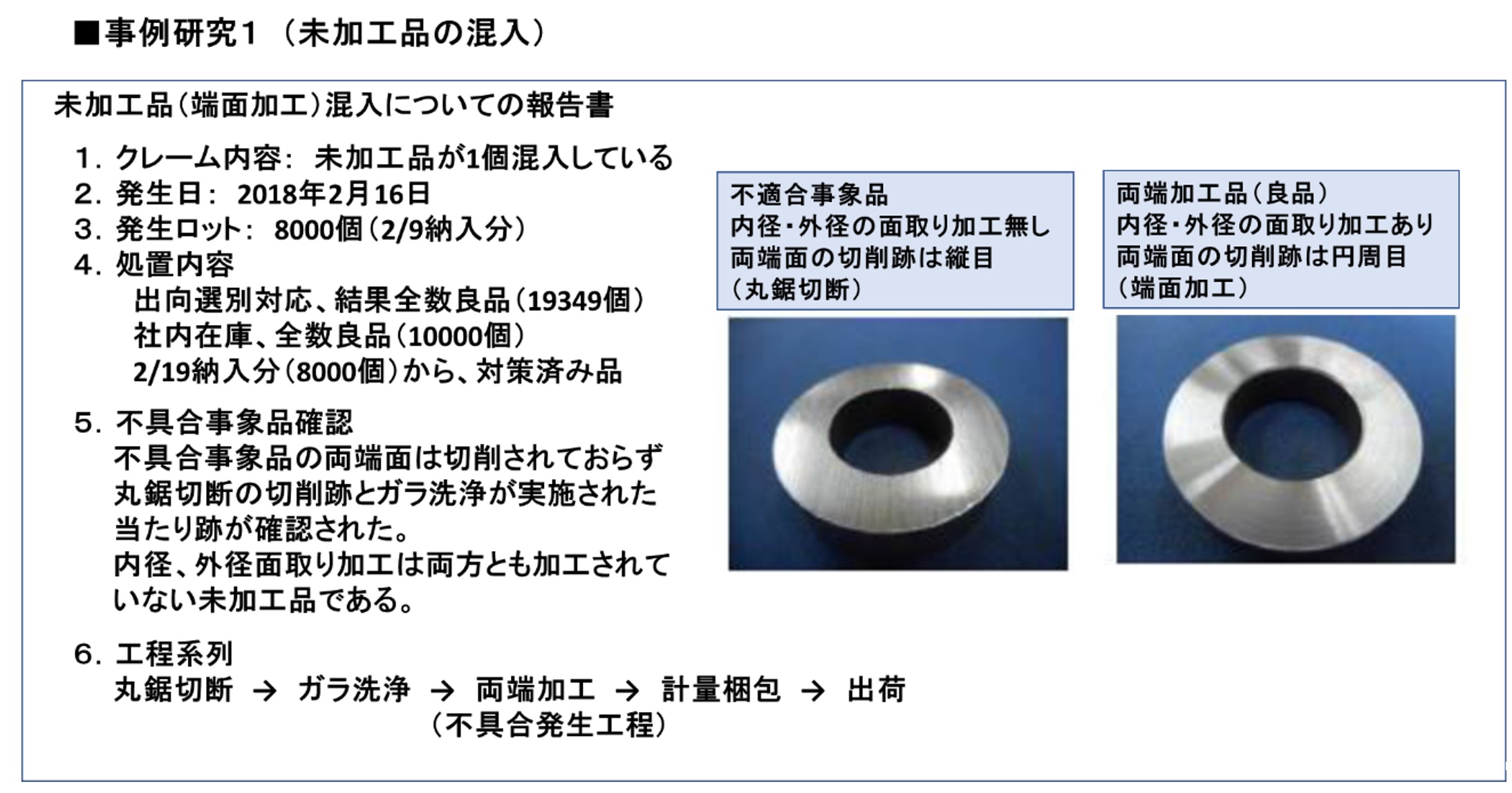
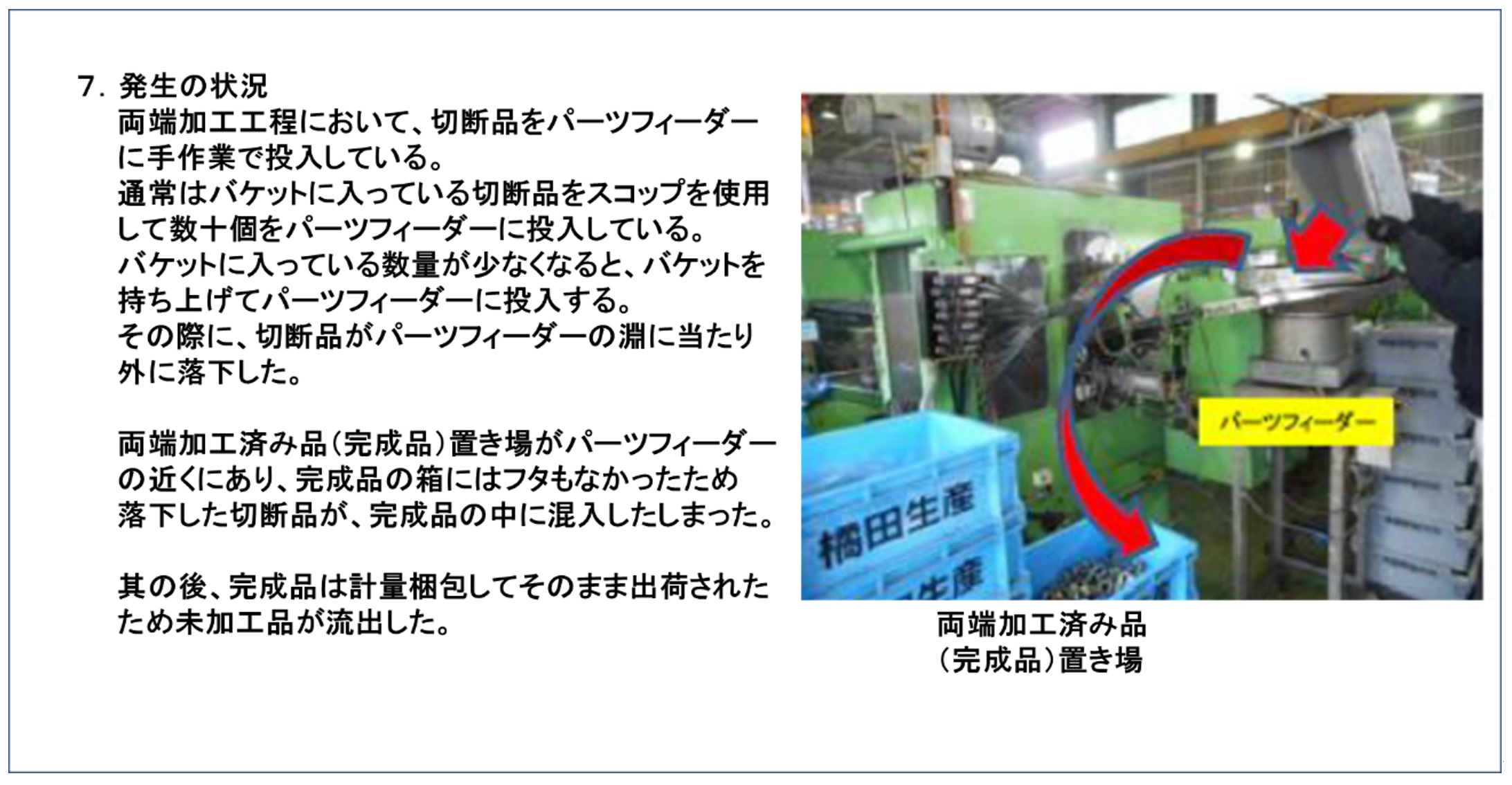
上記のクレームは、8000個のロットの加工部品の中に、未加工の部品が1個紛れ込み、そのまま出荷されてしまったというものです。
7項の発生の状況から、いくつかの管理上の問題点が浮かび上がってきます。完成品の箱に蓋をすれば解決するという単純な問題ではなく、作業者や管理者も含め、事前に検討すべき項目が抜けていた、ということに気が付かなければなりません。
では、実際にお客様に報告した対策書の原因究明と対策内容を検討してみます。
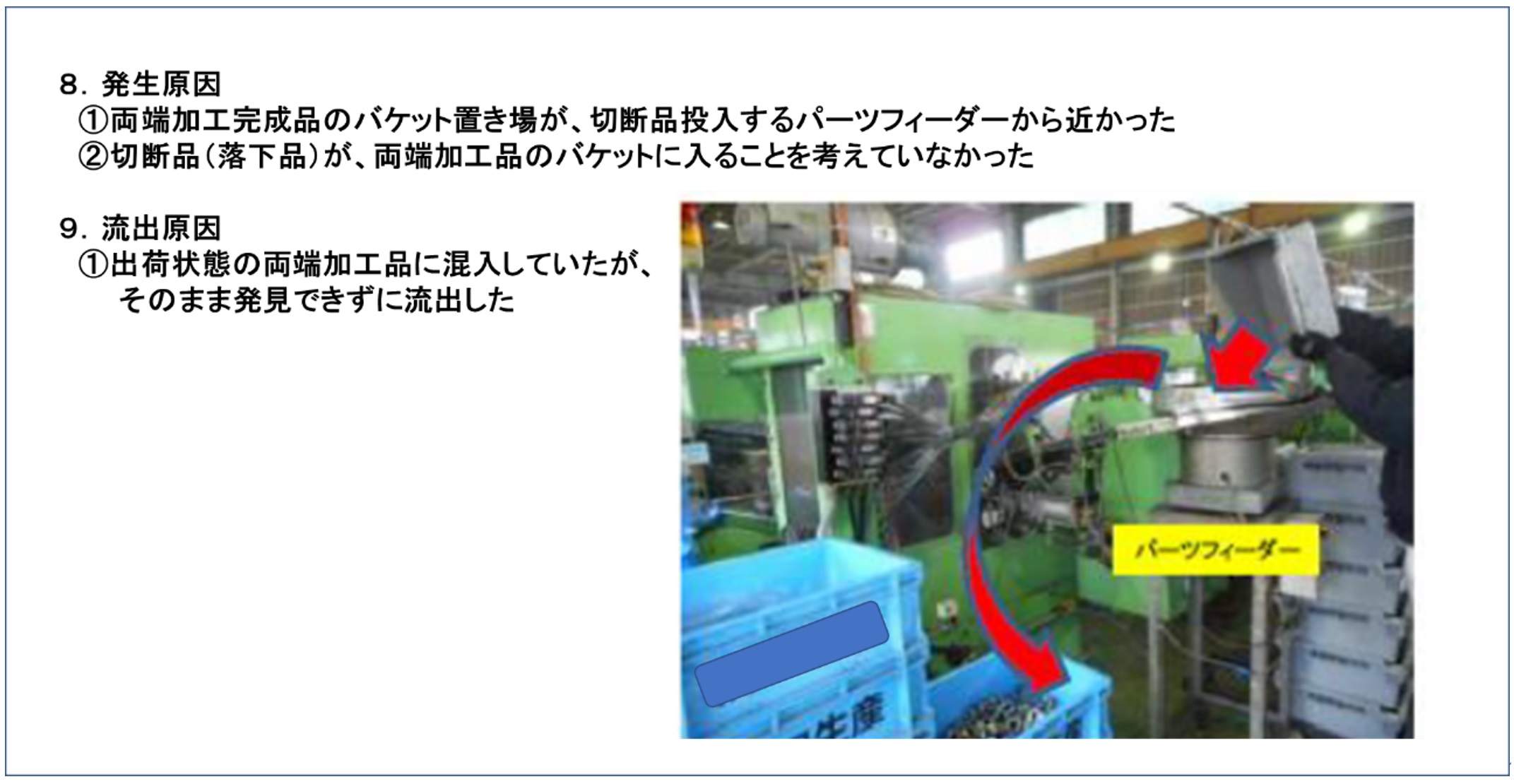
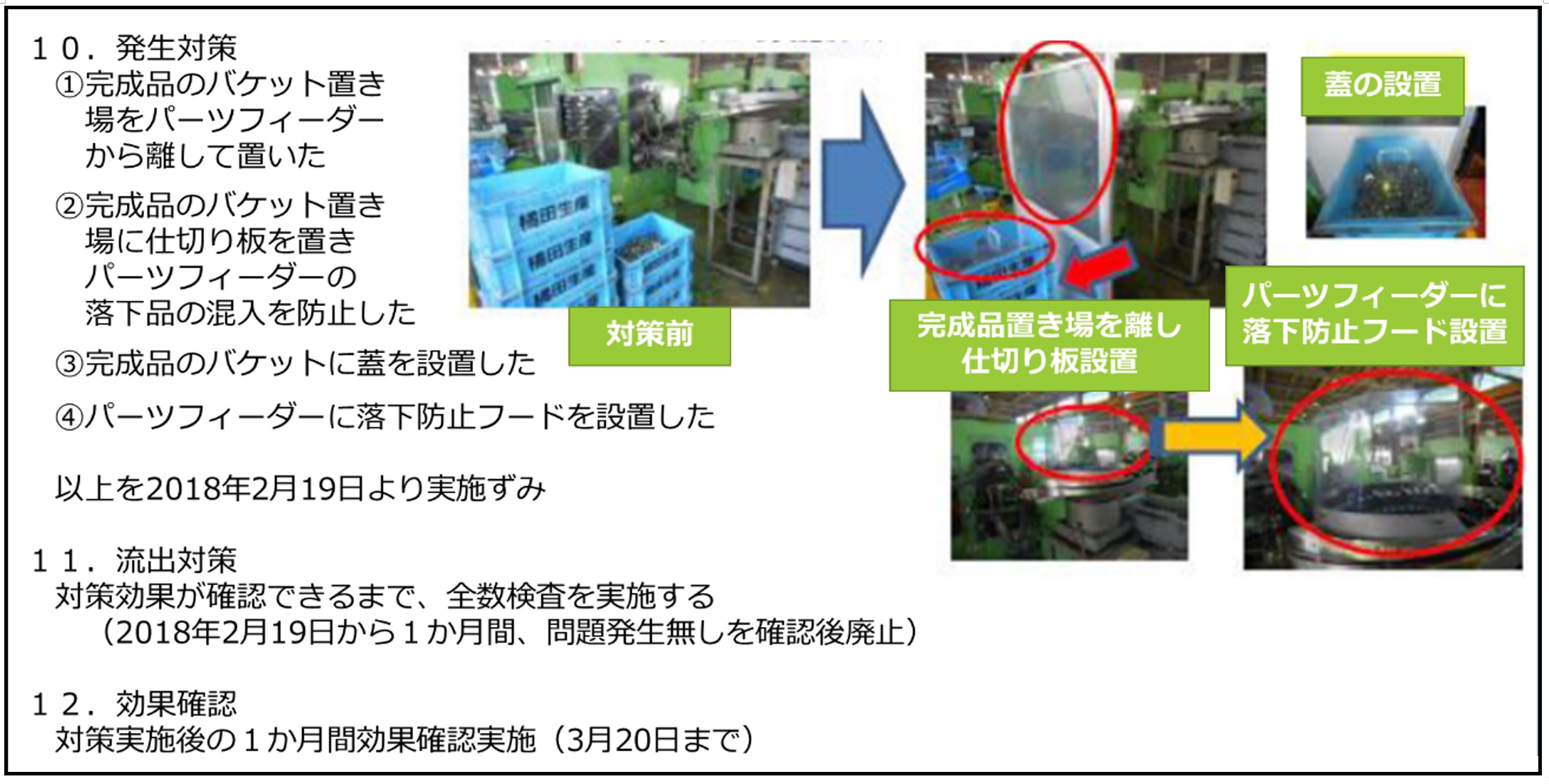
内容を見ると、一見「混入」の原因となったと思われる箇所に「混入防止の処置」が実施されており、今後は同じ問題は発生しなくなったと考える人も多いと思います。しかし、この対策内容では、まったく再発防止の効果は期待できません。
この報告書は、いったい何が問題なのでしょうか?
では、正しい対策内容を見てみましょう。対策書は以下の4つのステップで作成することを推奨します。
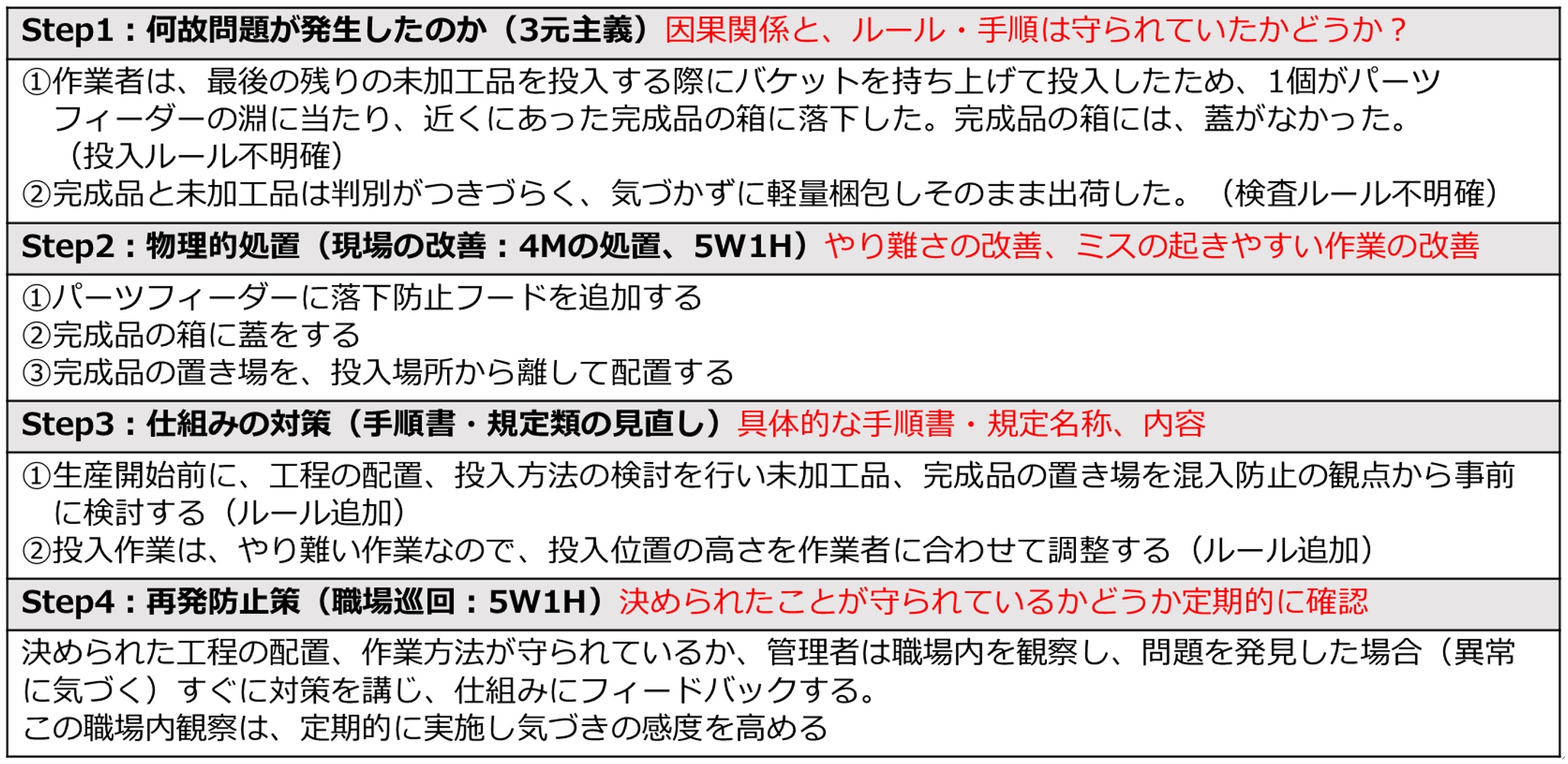
Step1:なぜ起こったのか(事実と因果関係)
モノの不適合に対しては固有技術の問題を論理的に追跡するトラブル・シューティングを行います。主な注意点は以下の通りです。
- 原因は頭で考えるのではなく、三現主義(事実)を基に因果関係を調べる
- 人の作業により発生した問題は、人の作業をよく観察する。特に作業指示書の指示内容と異なる作業を行っていないか確認する
- 作業環境、機械設備、治工具の配置、操作方法に問題がないか確認する。自分で実際に作業指示書通りに作業を行ってみて確認する
- 完成品が良品であることをどのように確認しているか?どのようなルールで判断しているのかを確認する
- 完成品、未加工品、不良品の配置、置き方などIN➯OUTの流れ、レイアウトがどうなっているか、どのようなルールで決められているか?あるいは決まっていないの」か?を確認する
では、今回の作業ミスについてはどうでしょうか?前述の4項(人的ミスの原因と是正処置)で解説した、2つの分類と4つの要因に当てはめて考えます。作業方法を曖昧にしておくと、作業者が勝手に楽な方向へ作業方法を変えてしまいます。
スコップを使用すべきところを、直接バケットを持ち上げて投入したために未加工品が落下し、完成品の中に混入してしまった、つまり作業者は、手順を守らなかった「モラル不足」に当たります。
スコップの作業がやり難いから、バケットを持ち上げて部品を投入する、これは作業者の立場から見ると合理的に見えますが、実は部品が外に落下し、また落下したことに気づかないという危険性もあります。安易な考えで、作業方法を変えてはならないということです。
Step2:物理的処置
ここでは、3つの処置が行われています。現場の立場では、一刻も早く現状の悪さをなくしたいという考えから、緊急的な処置を行います。そして、この内容でお客様に「対策完了」と報告します。しかしこれで問題は解決したと胸をなでおろすことはできません。
なぜ事前に防げなかったのか
一般に、この観点がどこの企業でもおろそかになり、結果として再発防止が図られないのです。なぜ起こったかは追求しても、なぜ防げなかったのかを追求しません。上記の事例のように、実際に完成品に蓋をするという発生防止対策が取られており、物理的な処置を行って、発生対策として済ませてしまう場合が非常に多いと思います。
これでは、もぐらたたきから永久に抜け出せないのです。上記のポカミスの事例では何故、スコップを使って投入しなかったのか?また、完成品が何故投入場所の近くに置かれていたのか?に注目する必要があります。
Step3 :仕組みの対策
完成品置き場は、未加工品投入場所に近く、落下、混入の危険性があるのに、それに気づかなかったので検討がされていなかった、またスコップによる投入作業がやり難い作業ということが見過ごされていたために、発生したクレームであると言えます。
つまり、生産前、あるいは生産中の早い段階で、このことに気づかなかった、気づくためのしくみ(ルール)がなかったことが「真の原因」と捉えることができます。
発生したから蓋をするではなく、発生する前に問題の有無を検討し、蓋が必要、スコップによる投入作業の見直しが必要、と早い段階で気づくことが重要な点であると言えます。
気づくためのツールとして、2つの例を紹介します。
【ヒューマンエラー予防処置評価シート】
起こり得るヒューマンエラーを、各工程に沿って抽出し、発生防止策、流出防止策を講じます。生産が始まる前に実施し、QC工程表に対策を盛り込むのです。起こりうるヒューマンエラーは、過去事例の蓄積データ、作業指示書の検証結果、作業者の作業を観察し、ミスの発生しやすい作業をピックアップします。
【作業観察と作業指示書へのフィードバック】
作業者の作業の様子を動画で撮影し、それを複数の有識者が何度も再生して観察し、ミスの起きやすい作業や、やり直しの多い作業を抽出します。その結果に基づいて、作業指示書や、動画マニュアルに改善策をフィードバックします。
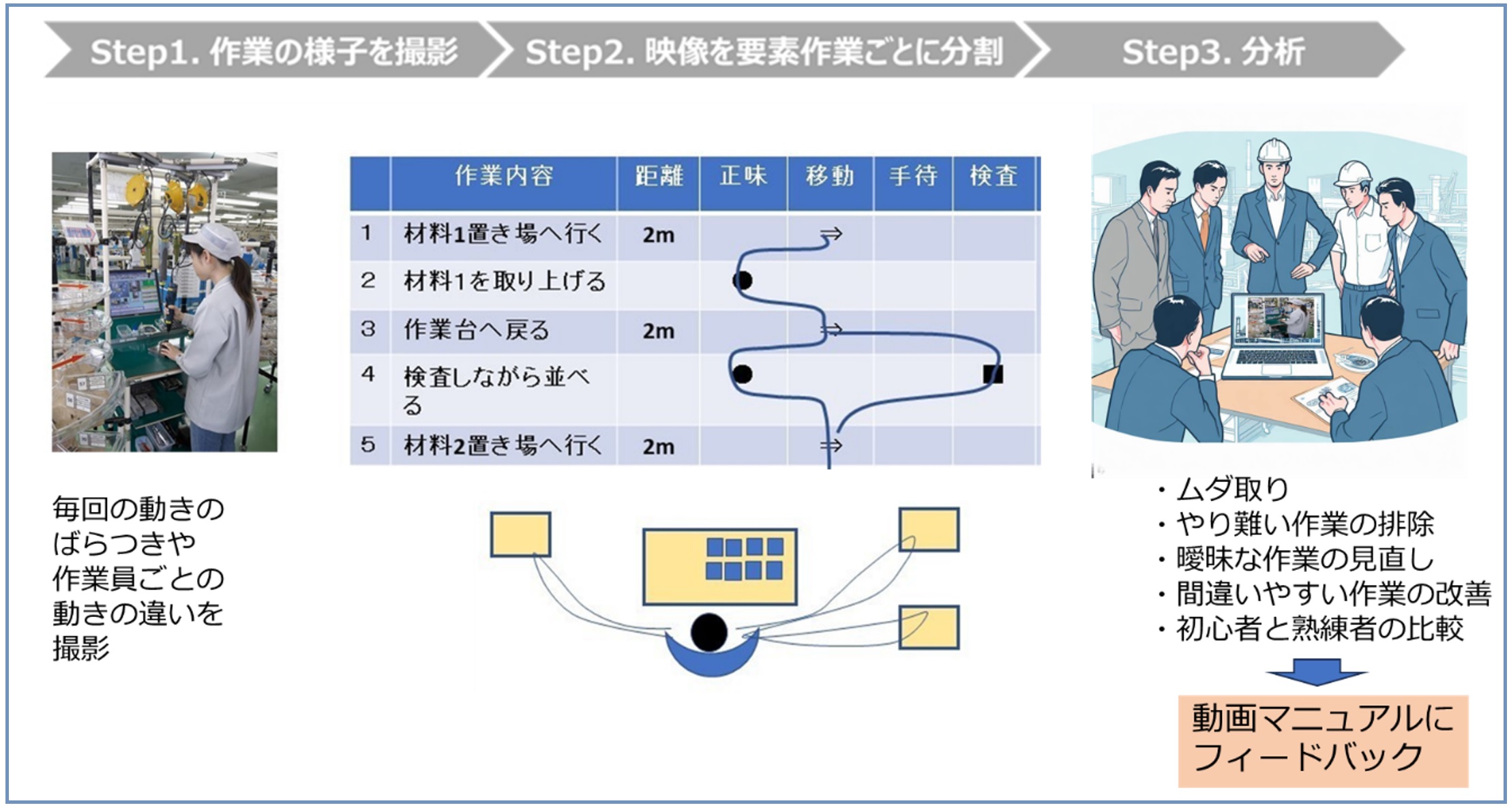
Step4 :再発防止策
規定類、手順書の見直しを行ったら、それが遵守されているか?やり難い点がないかどうか?日常業務の中で定期的に確認し、再発防止が確実なものとなっているかどうか管理者の目で観察することが重要となります。
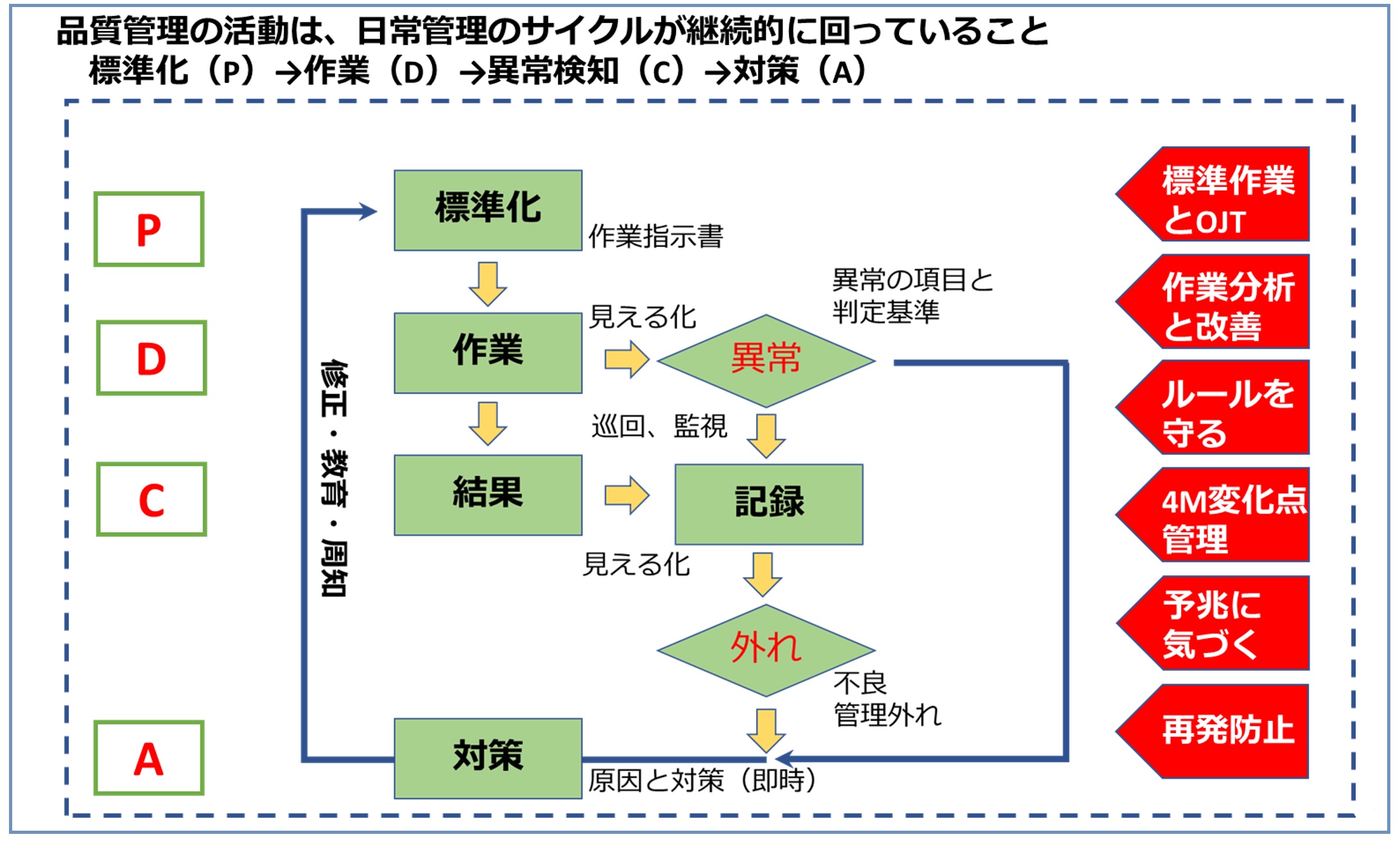
また、以下のようなヒヤリハット報告のルールを運用することも作業者の意識向上にもつながり、ミスの防止に有効な手段であると言えます。
【ヒヤリハット報告書】
作業中ミスを起こしそうになった内容を記録し、関係者で原因究明と対策を講じます。設計変更、工程変更などの初期品に対し実施し、結果をQC工程図へフィードバックします。
6. まとめ:品質改善のための重要ポイント
以上の解説から、「未然防止」の仕組み作りが大変重要であることが理解できたと思います。クレーム対策書は、Step1~Step4に従って作成することと、仕組みづくりの内容として、以下の①~③を盛り込んだ対策内容とすることで、ヒューマンエラー(ポカミス)は劇的に減少します。
しくみづくり①:工程事前検討のしくみ
- 5Mの管理項目を過去事例やお客様要求内容を重点項目として盛り込み、QC工程表の作成を行う
- ヒューマンエラー予防処置評価シート作成
- 本格生産の前に作業を実際に試行し、作業を有識者の目で観察し、ミスの起きやすい作業を抽出し改善する
しくみづくり②:日常業務のしくみ
- 管理者による巡回検査、ヒヤリハット報告等により気づきの感度を高める
- 問題を発見したら、速やかに作業手順書にフィードバックする。これは現場の責任で実施し、決して放置してはならない
しくみづくり③:再発を防止するためのルール順守のしくみ
- 自工程検査・・・作業者自らが確実に作業したかどうか確認する(指さし確認等)
- 自働化・ポカヨケ・・・人の作業を機械に置き換える
- 第三者検査 ・・・作業者以外の第三者の検査により、問題をフィードバック
- 巡回検査・・・とくに作業手順書改定後は改訂された通り作業を実施しているかどうかを管理者は現場で確認する
▼さらに深く学ぶなら!
「クレーム対策書」に関するセミナーはこちら!
※本記事を執筆した専門家「濱田金男」が提供するセミナー一覧はこちら!