1. QC7つ道具とは
QC7つ道具は品質管理の基本的ツールであり、次の7つを指します。
以前は層別の代わりに「グラフ」が入っていましたが、グラフは各種データを観る為のかなり一般的な手段として浸透しました。 そこでグラフに代わって層別が新たな7つ目のツールとして加えられました。
QC7つ道具はそれぞれ独立して使うよりも、いくつかを組み合わせて用いる方が効果的に情報を引き出し、結論を導く事に繋がります。QC7つ道具は統計的手法の基本と言う役割だけでなく、通常業務にも役立つツールです。主観を排除しデータに基づきアプローチを行う業務においては、分野を問わず利用が出来ます。
一方QC7つ道具は基本ツールではあるものの、本当に使いこなすのは簡単ではありません。ツールがどのようなものか、どうやって作成するかを説明できても、どの様に活用するかは簡単に身に付きません。QCサークル活動で、報告の為に無理やりQC7つ道具に当てはめているケースもありますが、本来まとめの段階だけでなく、情報整理や解析の段階で使用して欲しいものです。
職場の品質改善を効果的に進めていくには、「QC的ものの見方・考え方」「QC手法」「問題解決の進め方」の3つの道具に加え、それを使いこなす「問題解決力」が必要となります。
問題解決力の向上に不可欠な知識力、コミュニケーション力、解析力などを強化することで、現場力向上につながります。
2. QC7つ道具:特性要因図の正しい使い方
今回は、QC7つ道具:特性要因図の正しい使い方を解説します。
製造業では常識となっている「QC7つ道具」ですが、正しく理解して、実践している現場は必ずしも多くありません。QC7つ道具は単なる道具であり、その内容を理解していても使いこなせなくては意味がありません。つまり、何のために使うのか(目的)、データの収集・分析など、QC7つ道具に関わるQC問題解決の全体を理解する必要があるのです。
現場で問題が発生したときは、現場に行って、問題を起こした現物を見て、現実(現状)を知り、その確認したデータをどんなQC7つ道具を選定して解析するのかが重要です。
特性要因図は、形状が魚の小骨に似ている事からフィッシュボーンと呼称され、ある特性に対する原因を系統的に整理して関連付けるために使用します。QCサークル発表会などでよく見かけるQC7つ道具の一つです。特性要因図は、1960年代に石川馨氏よって開発され、クレームなど製品の品質特性に関連する要因を列挙する手法であるとともに、求められる製品の品質特性を得るためには、どのような項目を管理すれば良いかを漏れなく列挙するためのツールとして用います。
特性要因図は、結果(品質特性)に原因(要因)がどのように関係し、影響しているかを矢印で表した図のことです。主に品質問題を改善すると思いますから、その項目は結果なのか要因なのかを冷静に考えて見ましょう。特性要因図のスタート部分ですから、慎重に考えましょう。
特性要因図によって、品質との因果関係を突き止めることで、より具体的な課題が設定できます。テーマとして取り上げた項目は、改善したい項目ですからより具体的な表現にします。
ものづくりの現場などで作成する特性要因図は、主に中心線に対して、4Mを配置します。Man(人)Machine(機械・設備)Material(材料)Method(方法)です。この他測定系の問題も考えられる場合は、Measurement(測定)も加え、5Mとします。
特性要因図は、1960年代に石川馨氏よって開発され、クレームなど製品の品質特性に関連する要因を列挙する手法であるとともに、求められる製品の品質特性を得るためには、どのような項目を管理すれば良いかを漏れなく列挙するためのツールとして用います。
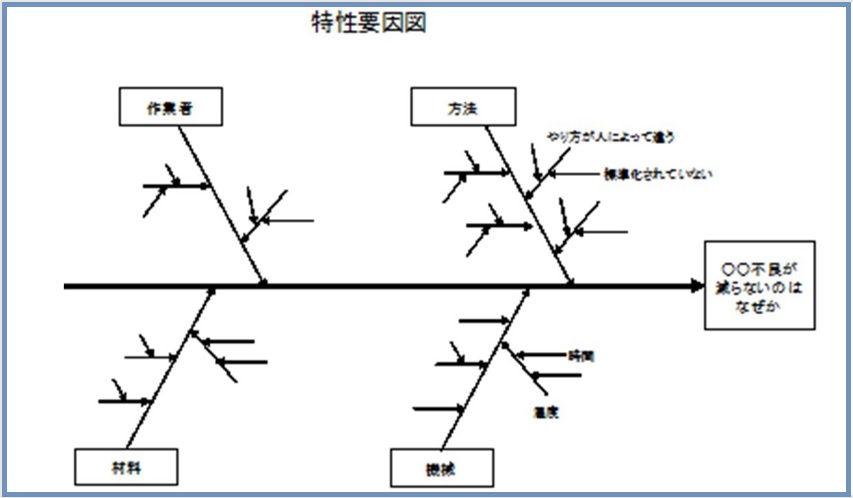
3. トラブルの原因調査
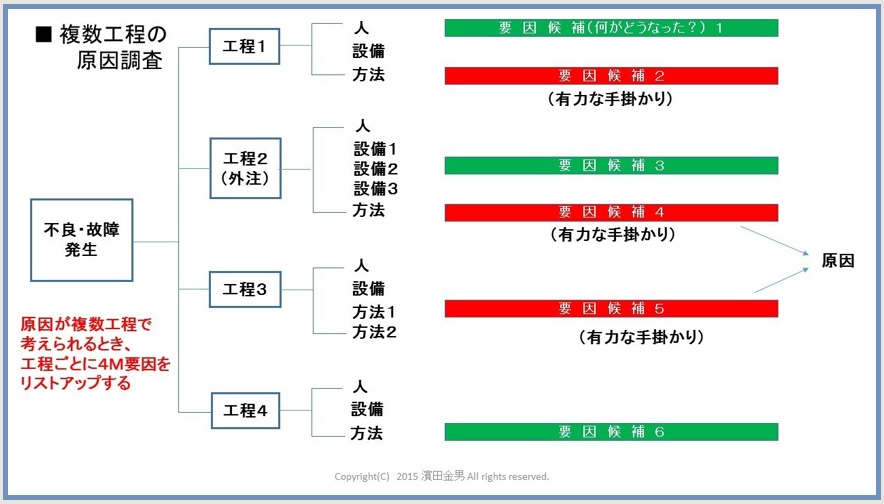
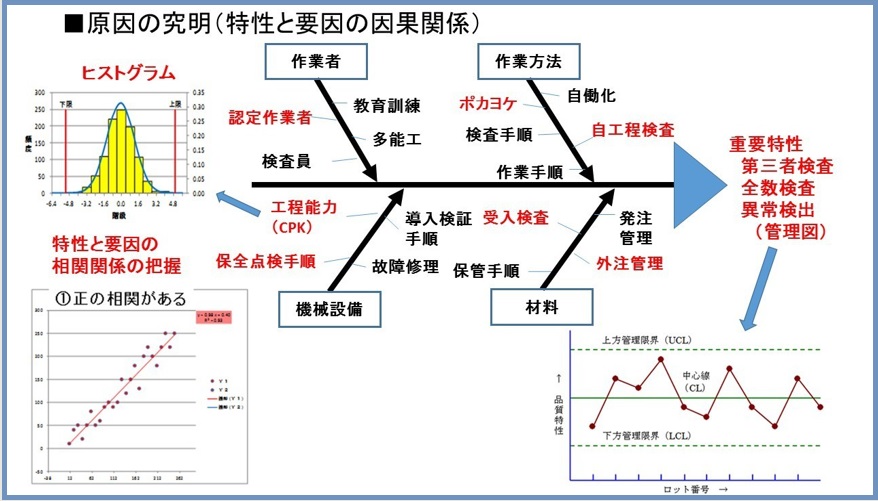