現在市販されている生産管理パッケージや
MRPパッケージの生産管理モジュールのほとんどは、
MRPという生産計画ロジックをベースにしています。
MRP(Material Requirements Planning:資材所要量計画)とは、約40年前に生産管理にコンピュータを活用するために実用化された生産計画生成ロジックです。
MRPは製品の生産に使う部材を、その部材が必要とする時期に合わせて調達するための必要量計算を行います。主要機能は「部品(材料)展開」「リードタイム逆算(バックワード)指示」「同一期間(タイムバケット)での必要部品の統合」などから成り立っています。
MRPをうまく活用すると、生産が必要とする時期に部材をジャストインタイムで手配することができます。このことで、在庫削減、リードタイム短縮、生産能力発揮といった面での改善効果が期待でき、工場の利益アップにつながっていくはずです。生産管理システムベンダーのカタログや提案書にはこうした導入効果が並んでいます。ところが実際の製造現場ではMRPがうまく機能することはほとんどありません。期待通りの効果が得られた工場も限られます。せいぜい指示伝票の発行の手間が減ったといった程度の作業改善がほとんどで、何千万円や何億円といったシステム投資に見合うものになっていないのが現状です。
なぜMRPは日本の工場ではうまく機能しないかというと、日本の工場ではMRPが機能するための前提条件となっている次の事項を実現するのが難しいためです。
〔 MRPが機能するための前提条件 〕 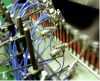
・部材を必要とする時期が明確になっている
・部品展開をするための部品表が整備されている
・部材の手配リードタイムが明確で精度が高い
・部材の欠品が起きない
日本の製造業は受注生産企業が多く、取引先の要望により必要時期(納期や生産計画)の変更は頻繁に起こりますので、時期の明確化は至難の業です。しかも取引先からの設計変更要求などにより部品表の作成や修整が間に合わないこともよくあります。
リードタイムは製造能力と製造数量との関係で変化します。とくに大量の部材が必要な場合は、リードタイムを明確に設定するということはできません。また、MRPでは欠品があるとその部材を使っているすべての製品の生産ができなくなるため、MRPを機能させるためにはある程度の安全在庫を積み上げておくことが求められます。とくに部品生産計画の作りにくいBTO生産企業にとっては深刻な問題です。
MRPにはこうした問題があるためそのまま活用することが難しく、日本企業では部品展開と手配(指図、内示)書発行用にしか使っていないMRP生産管理システムがほとんどのようです。この状態では経営改善効果を期待することはできません。リードタイム短縮も在庫削減も生産性向上も掛け声倒れになる可能性が高く、導入担当者は経営者から冷たい目でみられるかもしれません。
MRPの問題は、生産管理システムの機能だけを問題にしても解決はできません。対象製品の販売方法や生産方...