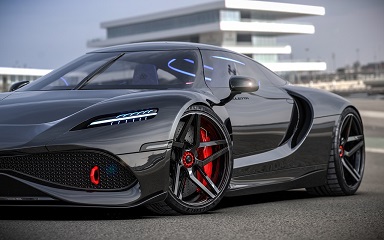
今日の製造業において、製品の表面処理は品質と機能性を左右する重要な工程です。その中でも、環境負荷の低減と高性能化を両立する技術として注目を集めているのが静電粉体塗装です。これは従来の液体塗料とは異なり、粉末状の塗料を用いることで、VOC(揮発性有機化合物)の排出を大幅に削減し、均一で美しい塗膜を形成します。持続可能な社会への移行が求められる現代において、静電粉体塗装はまさに常識を覆す技術であり、その可能性は多岐にわたります。今回は、静電粉体塗装の基礎から最新動向、そして未来への展望を解説します。
1. 静電粉体塗装の基礎とメカニズム
静電粉体塗装は、その名の通り、静電気の力を利用して粉末状の塗料を被塗物に付着させる塗装方法です。この技術の核心は、塗料が溶剤を含まない「粉体」である点にあります。塗装プロセスは、次のステップで進行します。まず、専用のガンを用いて粉体塗料に負の電荷を与え、霧状に噴射します。一方、塗装対象となる被塗物には正の電荷を印加するか、またはアースに接続することで、粉体塗料との間に電位差を発生させます。この電位差により、静電気的な引力が発生し、帯電した粉体塗料の粒子が被塗物の表面に効率良く引き寄せられ、均一に付着します。
この段階では、粉体は被塗物の表面に付着しているだけで、まだ固まっていません。その後、粉体が均一に付着した被塗物を高温の焼付炉に入れます。焼付炉内で加熱されることで、粉体塗料の粒子は溶融し、相互に結合して塗膜を形成します。冷却されると、強固で耐久性のある塗膜が完成します。このメカニズムにより、液体の塗料では困難であった複雑な形状の部品にも均一な厚みで塗膜を形成することが可能となり、液だれやムラの発生を抑制できるのが大きな特徴です。
2. 静電粉体塗装の多角的なメリット
実は、静電粉体塗装は私たちの身の回りの様々な製品で活躍しています。例えば、ガードレールや道路標識の支柱、公園の遊具、スチール家具、自動販売機の筐体、自動車のアルミホイールなどがその代表例です。これらの製品に共通するのは、屋外での使用に耐える高い耐久性と、美しい外観が求められる点です。
(1)環境負荷の低減
静電粉体塗装は、その特性から多岐にわたるメリットを提供し、多くの産業分野で採用が進んでいます。最も顕著なメリットの一つは、環境負荷の低減です。従来の液体塗料に含まれるVOC(揮発性有機化合物)は、日本の大気汚染防止法や、化学物質の排出量を国に届け出るPRTR制度においても規制の対象となっており、大気汚染や作業者の健康被害の原因となることが指摘されてきました。静電粉体塗装は溶剤を一切使用しないため、VOC排出量をほぼゼロに抑えることができ、環境規制の強化が進む現代において非常に有利な選択肢となります。
(2)高い塗膜性能
次に、高い塗膜性能が挙げられます。焼付によって形成される塗膜は、物理的・化学的に非常に強固です。耐候性、耐食性、耐薬品性、耐摩耗性に優れており、厳しい使用環境下でも製品の長期的な美観と機能を維持します。これにより、製品の寿命延長に貢献し、メンテナンスコストの削減にも繋がります。
(3)作業効率の向上とコスト削減
さらに、作業効率の向上とコスト削減も大きな利点です。粉体塗料は一回の工程で比較的厚い塗膜を形成できるため、多層塗りが不要なケースが多く、乾燥工程も短縮できます。また、オーバーミスト(被塗物以外に飛散した塗料)を回収して再利用できるため、塗着効率...
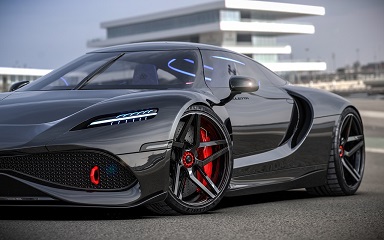
今日の製造業において、製品の表面処理は品質と機能性を左右する重要な工程です。その中でも、環境負荷の低減と高性能化を両立する技術として注目を集めているのが静電粉体塗装です。これは従来の液体塗料とは異なり、粉末状の塗料を用いることで、VOC(揮発性有機化合物)の排出を大幅に削減し、均一で美しい塗膜を形成します。持続可能な社会への移行が求められる現代において、静電粉体塗装はまさに常識を覆す技術であり、その可能性は多岐にわたります。今回は、静電粉体塗装の基礎から最新動向、そして未来への展望を解説します。
1. 静電粉体塗装の基礎とメカニズム
静電粉体塗装は、その名の通り、静電気の力を利用して粉末状の塗料を被塗物に付着させる塗装方法です。この技術の核心は、塗料が溶剤を含まない「粉体」である点にあります。塗装プロセスは、次のステップで進行します。まず、専用のガンを用いて粉体塗料に負の電荷を与え、霧状に噴射します。一方、塗装対象となる被塗物には正の電荷を印加するか、またはアースに接続することで、粉体塗料との間に電位差を発生させます。この電位差により、静電気的な引力が発生し、帯電した粉体塗料の粒子が被塗物の表面に効率良く引き寄せられ、均一に付着します。
この段階では、粉体は被塗物の表面に付着しているだけで、まだ固まっていません。その後、粉体が均一に付着した被塗物を高温の焼付炉に入れます。焼付炉内で加熱されることで、粉体塗料の粒子は溶融し、相互に結合して塗膜を形成します。冷却されると、強固で耐久性のある塗膜が完成します。このメカニズムにより、液体の塗料では困難であった複雑な形状の部品にも均一な厚みで塗膜を形成することが可能となり、液だれやムラの発生を抑制できるのが大きな特徴です。
2. 静電粉体塗装の多角的なメリット
実は、静電粉体塗装は私たちの身の回りの様々な製品で活躍しています。例えば、ガードレールや道路標識の支柱、公園の遊具、スチール家具、自動販売機の筐体、自動車のアルミホイールなどがその代表例です。これらの製品に共通するのは、屋外での使用に耐える高い耐久性と、美しい外観が求められる点です。
(1)環境負荷の低減
静電粉体塗装は、その特性から多岐にわたるメリットを提供し、多くの産業分野で採用が進んでいます。最も顕著なメリットの一つは、環境負荷の低減です。従来の液体塗料に含まれるVOC(揮発性有機化合物)は、日本の大気汚染防止法や、化学物質の排出量を国に届け出るPRTR制度においても規制の対象となっており、大気汚染や作業者の健康被害の原因となることが指摘されてきました。静電粉体塗装は溶剤を一切使用しないため、VOC排出量をほぼゼロに抑えることができ、環境規制の強化が進む現代において非常に有利な選択肢となります。
(2)高い塗膜性能
次に、高い塗膜性能が挙げられます。焼付によって形成される塗膜は、物理的・化学的に非常に強固です。耐候性、耐食性、耐薬品性、耐摩耗性に優れており、厳しい使用環境下でも製品の長期的な美観と機能を維持します。これにより、製品の寿命延長に貢献し、メンテナンスコストの削減にも繋がります。
(3)作業効率の向上とコスト削減
さらに、作業効率の向上とコスト削減も大きな利点です。粉体塗料は一回の工程で比較的厚い塗膜を形成できるため、多層塗りが不要なケースが多く、乾燥工程も短縮できます。また、オーバーミスト(被塗物以外に飛散した塗料)を回収して再利用できるため、塗着効率(実際に製品に付着した塗料の割合)は95%以上に達することも可能です。これにより塗料の無駄を最小限に抑え、材料費の大幅な削減に貢献します。塗装ブースの清掃も比較的容易であり、廃棄物処理コストも低減できます。
(4)複雑な形状への対応力
最後に、複雑な形状への対応力も注目すべき点です。静電気の作用により、カゴ状の部品や細かな凹凸のある部品に対しても均一に塗料が付着するため、品質の安定化に寄与します。これらの多角的なメリットが、静電粉体塗装の普及を加速させています。
3. 静電粉体塗装の課題
(1)色替えの難しさ
静電粉体塗装は多くの利点を持つ一方で、いくつかの課題も抱えています。その一つが、色替えの難しさです。特に多品種少量生産の現場では、頻繁な色替えが必要となるため、粉体塗料の清掃や交換に時間がかかり、生産効率が低下する可能性があります。この課題に対しては、塗料供給システムや塗装ブースの自動清掃機能の進化、カートリッジ式の塗料供給システムの導入などが進められています。これにより、色替え作業の時間短縮と効率化が図られています。
(2)塗膜厚の制御に関する課題
次に、塗膜厚の制御に関する課題です。静電気の性質上、被塗物のエッジ部分に電界が集中して塗料が集まりやすくなる「エッジ部効果(端面効果)」により、塗膜が厚くなる傾向があります。一方で、凹んだ部分や入り組んだ角の内側には電界が届きにくく、塗料が付着しにくい「ファラデーケージ効果」も発生しやすく、均一な塗膜厚を得るのが難しい場合があります。。この課題克服のためには、塗装ガンや粉体供給装置の制御技術の高度化、ロボットアームを用いた精密な塗装パスの最適化、そして塗料自体の流動性や帯電特性の改善が進められています。
(3)初期投資の高さ
また、初期投資の高さも導入障壁となることがあります。静電粉体塗装システムは、塗装ブースや焼付炉、粉体回収装置(サイクロンやバグフィルター)といった専用設備が必要となるため、液体塗装システムに比べて設備投資額が高くなる傾向があります。これに対しては、より費用対効果の高いシステムの開発、中小企業向けのリースやレンタルプログラムの提供、そして省エネルギー化によるランニングコストの削減がアプローチとして考えられます。
最後に、塗料の種類が液体塗料に比べて限定的であることも課題でした。しかし、近年では様々な機能性粉体塗料(例えば、抗菌性、防汚性、導電性など)の開発が進み、その選択肢は着実に広がっています。これらの課題に対する技術革新とシステム改善が進むことで、静電粉体塗装はさらに幅広い分野での適用が期待されます。
4. 電着塗装との比較――適材適所の表面処理
表面処理技術には様々な選択肢があり、静電粉体塗装と同様に優れた性能を発揮する技術として電着塗装が挙げられます。両者はそれぞれ異なるメカニズムと特性を持つため、適材適所で使い分けることが重要です。
(1)電着塗装
電着塗装は、被塗物を水溶性の塗料の中に浸し、電気の力で塗料を析出させて塗膜を形成する技術です。最大の特長は、被塗物の隅々まで塗料が均一に付着する「回り込み性」に優れている点です。複雑な内部構造を持つ部品や、狭い隙間にも均一な塗膜を形成できるため、自動車の車体内部や部品の防錆目的などで広く用いられています。また、水性塗料を使用するためVOC排出量が少なく、環境負荷も低いという共通点があります。
(2)静電粉体塗装
一方、静電粉体塗装は、前述の通り粉体塗料を静電気で付着させ、焼付けによって塗膜を形成します。電着塗装と比較した場合の利点として、厚膜形成能力が挙げられます。電着塗装は比較的薄い膜厚の形成に適しているのに対し、静電粉体塗装は一回の塗装で比較的厚い塗膜を形成できるため、耐食性や耐衝撃性など、より高い機能性が求められる場合に有利です。また、塗料タンクごと交換する電着塗装と比較して、原理的には色の切り替えがしやすく、多色展開に対応しやすい点も静電粉体塗装の強みです。
このように、電着塗装が内部の防錆や複雑形状への均一な薄膜形成に優れるのに対し、静電粉体塗装は一回の塗装で比較的厚い塗膜を形成できるため、耐食性や耐衝撃性など、より高い機能性が求められる場合に有利です。製品の用途、要求される機能、形状、生産量などを総合的に考慮し、最適な表面処理技術を選択することが、品質向上とコスト最適化の鍵となります。時には、両技術を組み合わせることで、それぞれの長所を最大限に活かすハイブリッドな表面処理も検討されます。
5. 静電粉体塗装の最前線と未来展望
静電粉体塗装は、その環境適合性と高性能から、常に進化を続けています。現在の最前線では、生産性の向上、機能性の付与、そして適用範囲の拡大が主なテーマとなっています。
(1)生産性の向上
生産性の向上では、高速塗装技術の開発が注目されています。これは、粉体塗料の供給速度や帯電効率を向上させ、塗装時間を短縮する技術です。また、AIを活用した塗装ロボットの最適化も進んでいます。AIが被塗物の形状や材質を認識し、最も効率的かつ均一な塗装パスを自動生成することで、熟練工の技術に依存することなく、高品質な塗装を安定して実現できるようになっています。これにより、人件費の削減と生産ラインの自動化が加速しています。
(2)機能性塗料へのアプローチ
機能性の付与も重要なトレンドです。単に保護や美観を目的とするだけでなく、塗膜自体に特別な機能を持たせる研究開発が活発です。例えば、抗菌・抗ウイルス性能を持つ粉体塗料は、医療機器や公共施設など衛生が重視される分野での応用が期待されています。自己修復機能を持つ塗料も開発されており、微細な傷であれば塗膜が自己修復することで、製品の寿命をさらに延ばすことが可能になります。さらに、導電性や電磁波シールド性を持つ粉体塗料は、電子機器分野でのニーズが高まっています。これらの機能性塗料は、製品の付加価値を高め、新たな市場を創出する可能性を秘めています。
(3)液体塗装が主流だった分野への進出
そして、適用範囲の拡大も進んでいます。従来の金属製品に加え、熱に弱い樹脂材料への低温焼付け技術が開発され、自動車部品や家電製品など、より広範な分野での粉体塗装の適用が可能になっています。また、木材やMDF(中密度繊維板)などへの粉体塗装も研究されており、家具や建材など、これまで液体塗装が主流だった分野への進出も視野に入っています。
未来に向けては、IoTやビッグデータ解析を組み合わせたスマートファクトリー化が加速するでしょう。塗装プロセスにおける様々なデータをリアルタイムで収集・分析し、最適な塗装条件を自動調整することで、品質のさらなる向上と不良率の低減が期待されます。また、環境への配慮は一層厳しくなるため、バイオマス由来の粉体塗料や、リサイクル性の高い塗料の開発も進むと考えられます。静電粉体塗装は、持続可能な社会の実現と、多様な製品の高機能化を支える基盤技術として、その可能性を広げ続けることでしょう。
6. まとめ
静電粉体塗装は、VOC排出ゼロという環境適合性、そして優れた塗膜性能を両立する画期的な技術です。静電気の力を利用して粉体塗料を効率的に付着させ、焼付けによって強固な塗膜を形成するそのメカニズムは、従来の塗装の常識を大きく覆しました。環境負荷の低減、高い耐久性、そして生産効率の向上といった多角的なメリットは、今日の製造業が直面する課題に対する有効なソリューションを提供しています。色替えや塗膜厚の制御といった課題は残るものの、技術革新により克服への道筋が見えており、機能性塗料の開発や低温焼付け技術の進展により、その適用範囲は着実に拡大しています。今後、IoTやAIとの融合により、さらにスマートで持続可能な塗装プロセスへと進化し、様々な産業分野において不可欠な技術となるでしょう。