QC7つ道具は単なる道具であり、その内容を理解していても使いこなせなくては意味がありません。つまり、何のために使うのか(目的)、データの収集・分析など、QC7つ道具に関わるQC問題解決の全体を理解する必要があるのです。現場で問題が発生したときは、現場に行って、問題を起こした現物を見て、現実(現状)を知り、その確認したデータをどんなQC7つ道具を選定して解析するのかが重要です。
今回は、特異な違いを見つけて品質管理を分かり易くするQC七つ道具の層別/分類について解説します。
1. 層別とは
層別とは、与えられたデータを一群ではなく、属性で分類したグループごとに分析する事です。 例えばQC七つ道具のひとつ散布図を作成してみたら、2つの因子の間に相関はないように見えても、装置、作業者、作業方法、材料ロットなどで層別して分析してみると相関係数がぐっと大きくなることがあります。 またヒストグラムではデータが正規分布することが多いものですが、左右非対称な場合に層別の因子を導入を検討してみましょう。一定の条件を与えて事象をグルーピングすることで、現状や問題点を明確にするための手法です。目的としては、品質や生産性に関する影響度を把握することにあります。
例えば、構内物流において時間毎の荷量や種類などを明らかにすることで、運搬の頻度や治具の見直し、あるいはバラツキの原因を明らかにすることで平準化に向けた改善につなげることなどが可能となります。同じような視点で、出荷や入荷の物流の改善にも応用が可能です。
また、設備や工程に流されている製品の『層別』を行うことで、同じような製造上の特性を持つ製品の流れを集約することで段取り替えの負担を減らし、多品種少量生産に向けた改善の着眼点を得ることも可能です。これは、特に構造別分類・機能別分類などとも呼ばれ、トヨタ生産方式を応用した仕組みの見直しにもよく使われます。
品質面の特性(不良、歩留まり、色合い、硬度、香り等)や数量面(一定時間における取り扱い数量や完成品の出来高等)の特性で仕分ける項目を決めて仕分けることで、傾向やバラツキを把握、問題解決の着眼点を得るには有効な方法です。
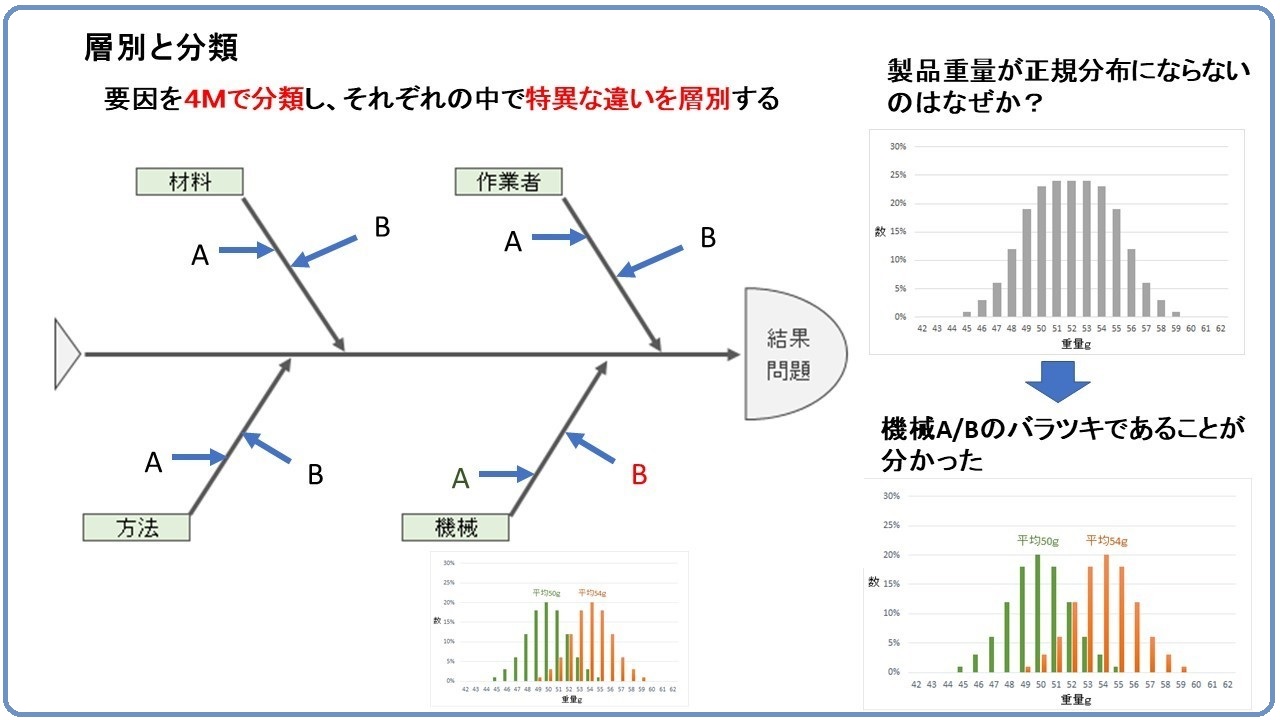
2. 分類とは
3. 層別、分類で重要な考え方
(5M)
② 材料別・・メーカー、購人先、ロット、購入時期など
③ 機械別・・機種、号機、型式など
④ 方法別・・作業方法、口ットなど
⑤ 検査測定別・・検査員、測定者、測定器、試験機、測定場所など
(5W1H)
② 環境条件別・・温度、湿度、作業場所など
③ 作業者・・個人、男女、年齢、経験年数、技能など
④ 方法・・作業方法、口ットなど
⑤ 材料・・メーカー、購人先、ロット、購入時期など
⑥ 目的・・不良をなくす、納期を守る、価格低減(QCD)
4. 層別のまとめ
層別のポイントは二つあります。一つ目はどの様な項目で切り分けるかという事です。もう一つはデータを取る時に後で層別解析が出来るように予め紐付けておくことです。
身長のデータは数値データに男女が紐付いていなければ男女別に層別出来ません。製造データであれば、どの装置で、どのラインで、どのシフトで作られたのか、情報が紐付けられていれば迅速...