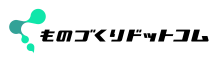
昨今の世間の早い流れにより、コンシューマー製品においては技術の目覚ましい発展に伴い、著しい変化・進歩がありますが、弊社の関連する業務放送機器においても、時代の流れに応じた顧客ニーズを満足させられる機器の提供や新しい運用の提案がすばやくできるような開発のし方をごく小集団で模索しております。
そのなかで、私の課題として”品質”があります。
キーワードは、「顧客ニーズ」と「すばやく」です。
顧客ニーズについては、製品を開発設計する技術者自らが現場や市場、顧客のところに赴き、現場環境や運用の実際を 現在および将来的な技術視点をもって観察・ヒアリングすることによって、顕在していることのみならず、潜在しているニーズを導き出していき、早い段階で具現化モデルを製作して現場での評価をしていただき、ブラシアップを重ねてニーズの満足度を高めていく開発をするということを試みています。
そして、”品質”の課題としてあるのは、「設計品質」です。把握したニーズの具現化したものをすばやく顧客に届けるため、また、評価とブラシアップを繰り返すサイクルのなかで、設計期間をできるだけ短くしながらも、設計品質をおろそかにできないという点です。
設計品質を担保するための手法は、いろんな方法があるようですが、いずれも 時間や手間がかかる、ゲート機能が生じる、学問的な視点になる など、精度を高めようとすればするほど ”すばやく”に相反することになると感じています。(現実、弊社での通常の開発プロセスではいろんな手法やツールにて問題となっている面があります)
そこで、まず対象として想定することをある特定の市場やごく限られた運用がされる環境で使用される製品に絞り、その限られた環境で使用するのに問題の無い設計品質を確保するために、最低限必要なことやどのようなことをすれば良いか を悩んでおります。
以上、ざっくりとした、判りにくい内容で、質問になっていないとは思いますが、アドバイスなどいただければ と思います。
よろしくお願いいたします。

時代の流れに応じ、顧客ニーズに沿った製品の提供や新しい運用方法の素早い提案ができるような開発体制の必要性を、最前線の開発担当者として肌で感じておられる内容ですね。
ご質問に対して一般論としての回答をまとめました。実際には、御社の現状を詳細に把握したうえで、改めて対策を講じていく必要があると考えられます。
1.全社テーマとしての提言
「技術者自らが現場や市場、顧客のところに赴き、現場環境や運用の実際を観察・ヒアリング」され顧客ニーズを把握することに努めているとありますが、環境変化に応じて、今までの設計スタイルの変革が求められており、全社的な取り組みが必要と思われます。このような重要なテーマについて、「ごく小集団」での取り組みではおのずと限界が見えてきます。
ボトムアップで改善を進めることも重要ですが、同時に現場の危機意識を会社全体の危機意識として捉えられるよう、管理層、経営トップに提案していくことも必要と考えます。
2.モデルケースとしての試行
”設計品質課題”として、「顧客ニーズの把握」と「スピード」をキーワードに上げておられます。そのことから、固有技術そのものよりも、老舗メーカーとして、長年積み重ねられた従来からの開発体制、開発設計プロセスが、時代に合わなくなって来たものと思われます。
まず、第一ステップとして、ある特定の分野の製品に絞り、限定された環境下で使用上問題の無い設計品質を確保することを目標としたいと言うお考えには賛成です。この製品群をモデルケースとして、まず成功させることが大事ではないかと思います。
では具体的にどのような設計手法の改善策があるのかを考えてみたいと思います。
3.標準化ユニットの顧客への提案
顧客ニーズは様々ですが、そのニーズに個別に応えて設計図面を作成していては、いくら設計工数を掛けても対応はできません。また、設計期間も短縮は難しく、品質的にも安定性を欠くものとなるでしょう。
営業部門、設計部門共同で、顧客ニーズを分類し、製品のシリーズ化とオプションユニットの品ぞろえによって、自社標準品の利点を顧客に提案する営業活動を行うように持っていくことも一つの方法です。これが顧客に受け入れられれば、顧客ニーズに素早く対応でき、品質も同時に確保することが可能になります。
4.設計プロセスの標準化
個別受注型、多品種少量生産の製品において、「標準化」「共通化」設計は重要なキーワードと考えられます。製品の構成要素を共通化するには、設計プロセスを標準化することが重要です。まず属人的な設計手法から脱却し、開発部門全員の力を結集する開発体制に持っていきます。
設計プロセスの標準化の一つの目的は、流用設計を可能とすることです。新たな顧客ニーズに基づく個別の製品でも、キーとなる機能や構造の70%以上を流用可能とすることです。そのキーとなる機能や構造を素早く検索、流用できるような設計プロセスを構築していきます。
それには以下の4つの考え方を設計プロセスに組み込みことを検討します。
・一つの製品は機能単位の標準ユニットの組み合わせであること
・図面の構成は製造工程順序を考慮した階層構成であること
・すべての部品、ユニットが、紐づけされていること
・部品の標準化を図ること
では、一つ一つ見て行きましょう。
4.1一つの製品は機能単位の標準ユニットの組み合わせであること
基本機能ブロックごとに一つのユニットにまとめ、必要な各機能ユニットを組み合わせることで一つの製品に仕上がるという考え方をとります。機構部は機構担当の設計者が、エレキ部はエレキ担当の設計者がと、別々に図面を起こすのではなく、一つの機能完成品としてのユニット構造が組み上がる図面構成とします。
この機能ブロックごとのユニットは、顧客によって基本的に機能や構造の変更は行わず、そのまま、どの顧客の製品にも組み込むことができる共通の基本単位として設計します。
この基本機能ブロックの設計には、過去に蓄積された、または埋もれている貴重な技術を結集する必要があり、大きな負担を強いられることが予想されますが、開発部門総力で、モデル機種を設定し、計画的に進めることで、乗り切ることができると考えます。
標準ユニット設定後は、新たな機能ユニットの設計、あるいは共通性を損なう機能の変更などを行う場合、設計審査、信頼性評価などのステップを踏み、設計部門および品質保証部門の認定を行う事とします。
4.2図面の構成は製造工程順序を考慮した階層構成であること
この標準ユニット群を品ぞろえすることによって、どの顧客の製品にも共通して組込みが可能となるため、見越し生産が可能となり、顧客固有の部分の軽微な設計、部品手配だけで済むようになり、設計工数・期間の削減、納入リードタイムの大幅な短縮が可能となります。
部品、アッセンブリー、サブユニット、ユニットと、階層構造の図面体系とする事によって、部品の手配、製造スケジュールも立てやすくなります。
4.3すべての部品、ユニットが、紐づけされていること
設計部門は、各顧客向けの製品仕様書、構成品表を作成し、その製品に必要な構成要素をすべて紐づけします。どのユニットを組み合わせるのか?顧客固有の指定部品はなにか?などをすべて図面から解かるようにします。
顧客別製品仕様書は、各顧客ごとに作成されますが、そこに紐づけされたユニットは標準化されたものとなります。
4.4部品の標準化を図ること
部品を標準化することで、現状の部品点数は大幅に集約されます。部品を決めることが、設計の方法や方式まで影響することになり、標準化が進み易くなります。回路や機構が一定の方向に統一され、各部門やプロセス全体のベクトルも方向性が一致します。
部品標準化は、概略以下の手順で進めることになります。
・実績のある部品について標準部品のデータベースを構築する
・設計に際し、できるだけ登録済みの標準部品の中から選定する
・新たに標準部品に選定する場合は一定の審査を行う
・標準部品は定期的に価格、調達面で見直し、充実と定着を図る
この考え方の導入は、個別型受注製品で、多品種少量生産品の品質を高めるための第一歩の考え方です。
私が以前所属していた会社では、このような設計、製造プロセスがほぼ完成されており、受注型製品の設計から製造プロセスに至るまで、見事に考えが統一されていました。
会社を離れ、様々な企業の開発・製造プロセス接して、今まで何ら疑問に思わず、当たり前のように思っていたことが、実は世の中でも最も進んだすばらしい考え方なのだ、ということを再認識させられました。
以上、的を得た答えになっているかどうかわかりませんが
ご意見やご質問など、お聞かせ願えれば幸いです。
|
質問者様からのコメントを頂き、大変ご苦労されている様子が伺えます。
「標準化や流用設計の枠を越えるケースで進めていくにあたって、いよいよ新たな視点で品質を確保する方法をも試行していく必要が出てきたものです」とある通り、標準化は容易ではない事が解ります。
私が以前所属していた会社では、部品点数約1万点の電子機器を製造販売していました。顧客は大手、および全国各地方に存在する100社あまりで、顧客ごとに図面を起こしカスタマイズ設計を行う必要がありましたが、これを17のユニットに分割し、標準化を図りました。
1万点の部品から成るBOMは10階層にも及びますが、約8000点の部品を17の標準ユニットに完全に分割しました。顧客固有のカスタマイズ設計部分は、外観色、ロゴマーク、操作部の配置、表示文字、操作キーの種類、保守用パネルなどの周辺機能に限定されます。
これを可能にしたのは、営業部門と顧客仕様とりまとめ部門(社内ではとりまとめ設計と呼ばれていました)が中心となり、機構設計、エレキ設計、ソフト設計、生産技術、開発購買、保守部門までを加えたプロジェクトにより、顧客要求仕様検討し、標準化を図った結果、機能、価格、納期の点ですべての顧客の支持を得られたのです。
出来るだけ顧客要求を取り入れながら、時には、自社の標準機能に納得して頂くことも必要になってきます。
その結果、国内市場トップシェアを確保、ブランドを築くことができました。
このことは、手法を導入すれば解決すると言うものではなく、顧客要求と自社が提供する製品・サービスの関係で解決すべき問題を相当期間掛けて試行錯誤しながら個別に解決していくしかない事を物語っていると思います。
|
ざっくりとした、分かりにくい内容と書いてありますが、決してそんなことはありません。
非常に重要で、かつ、どこの企業でも抱えている基本的な内容だと思います。
つまり、「高い」設計品質を、「短期間」で「確実」に作り上げるには、どうすれば良いか、という経営課題です。
この課題を、製品開発の5ステップで考えてみましょう。
1. ニーズの把握
2. ニーズを満たすための技術アイデアだし
3. 技術アイデアの確からしさの評価
4. 対策が必要なら設計変更し、再評価
5. 評価結果がOKなら、設計終了
多くの企業の製品開発は、このような5つのステップで進めていると思います。
この中で、開発期間短縮のボトルネックになるのは、どこでしょうか。どのステップに一番時間がかかるのでしょうか。
1~2ステップは、技術者の興味があるところですから、スムーズに進行する場合が多いと思います。アイデアがないなら別ですが、ご質問の内容からは技術アイデアが出ないので困っているわけではなさそうです。
しかし、3~4ステップは、実際にはなかなか進みません。進まないというより、一回で完全な評価が出来ず何回も繰り返絵さなければなりません。結局、時間がかかるのです。
質問の中でも、「評価とブラシアップ」という言葉が使われていましたね。まさに、この繰り返しをしているように見受けます。ここに悩みの本質があります。
つまり、評価結果の不十分さと多くの手間ひまが、開発期間短縮の一番のネックになっているのです。
一言で言うと、問題のない設計品質を素早く達成するには、設計品質の出来栄えを素早く確実に評価することが重要なのです。理想的には、評価とブラシアップは一ラウンドで終了させたいはずですね。効率的で評価結果も確実な評価手法が必要なのです。
でも、はたして、そんなことが出来るのでしょうか。
できます。品質工学は、この課題を解決するために考え出された方法論ですから。
量産後に遭遇するであろう様々な条件(つまり問題の発生原因)を使って、設計段階で設計品質の実力を短期間に評価してしまう方法です。
具体的には、製品の基本的な機能(働きや動き・プロセスなど)が周囲の意地悪な条件で影響を受けていないかを測定します。つまり、問題が発生しやすいかどうかという性質、逆に言えば安定性を測定するのです。
温度や湿度、経年劣化や汚れなどの周囲条件の影響を受け難ければ、信頼性が高いと言って構わないでしょう。
このようにして安定性を評価すれば、たとえば劣化時の不具合問題の発生しやすさ(問題発生の可能性)も予測可能になります。したがって信頼性テストを実施しなくても、信頼性を評価することが出来ますので、時間のかかる寿命や信頼性のテストを省略できます。
さらに、従来のテスト法よりこの方法の方が、評価がより確実に行えることも分かっています。評価に時間がかからないので、従来よりも数多くの条件を網羅した評価ができるので、評価の抜け漏れが少なくなるからです。つまり一回のテストで評価終了となる可能性が高くなります。
この考え方は、従来の常識からは外れているので、素直に納得できない人も多くいるのも確かです。しかし開発現場の実践で悩んでいる人は、「合理的な」考え方だと理解してくれる人が多いですね。実際に実施して成果もあげています。
これ以上の詳しい説明は、この紙面ではできないので、興味を持たれましたら、問い合わせください。
または、以下の書籍を参照ください。
日科技連出版社 「タグチメソッドのはなし」 2300円 長谷部光雄著
|
品質マネジメントシステムでは、製品の要求事項を決定する為に次の事項を明確にすることを要求しています。
・顧客が規定した要求事項。これには引渡し及び引渡し後の活動に関する要求事項を含む。
・顧客が明示していないが、指定された用途又は意図された用途が既知である場合、それらの用途に応じた要求事項。
・製品に適用される法令・規制要求事項。
・組織が必要と判断する追加要求事項すべて。
製品の設計を進める上で必要となることは、次の事項です。
・機能及び性能に関する要求事項
・適用される法令・規制要求事項
・適用可能な場合には、以前に類似した設計から得られた情報
・設計に不可欠なその他の要求事項
これらの要求事項が曖昧であったり、相反するものがないようにしなければならないのです。
顧客の潜在・顕在のニーズや期待は多岐にわたります。それを全て満たすことはできないと思います。優先順位又は、妥協する機能があるはずです。優先順位の付け方や妥協する機能の選択が「高機能な製品」になるか、そうならないかの違いと考えます。
設計品質が少なくとも、顧客やその他の関係者の満足を満たさない事態を避けるために次のことを検討します。
a)起こり得る不満の発生及びその原因の特定
b)不満の発生を予防するための、製品が具備すべき機能・仕様の内容の評価
c)必要な機能・仕様の決定及び設計仕様に反映
d)とった処置の結果を設計図書に記載
e)とった不満発生防止の予防対策の有効性の評価・確認
顧客のニーズや期待を中心に優先順位の高い機能や仕様を決定します。設計者自身が顧客と面談し把握しているのであれば、自ら評価ができますが、担当営業からの意見を聴取することも必要とされます。
ISO9001:2015年の改訂(ISO9001:2014DISで確認)で、事業を取りまく状況を捉え、利害関係者のニーズや期待を把握し、これらの事柄から機会やリスクを決定し、その製品に特有のプロセスを明確にして対応することとなっています。
|
直感的には、設計品質を高めたいとの質問ですので、ロバスト性向上を図るための品質工学、試作回数削減による開発リードタイム短縮を図るシミュレーション等の開発プロセスツールを導入することがベターと感じました。しかし、「設計品質担保の手法は、時間や手間がかかり、精度を高めようとすればするほど ”すばやく”に相反する」との矛盾を指摘されております。そこで、上位概念に移行してこの課題をブレークスルーしたいと思います。製品企画から技術開発・生産システム開発、開発プロセスツール指導等の経験から、別の視点で、コメントさせていただきます。絞られた特定事業分野が不明のため、やや一般化した回答にならざるを得ないことをお許しください。
(1) 設計品質変革するためには
結論を一言でいえば、品質の源流部分を管理することです。言い換えれば、実績に裏打ちされた「あるべき姿(真の目的)」を考えることです。筆者の35年の実務経験のデータベースから実践可能な具体案を提示すると、次のようになります。優先順位3項目に絞って解説したいと思います。。これらは、開発効率を変革する方法でもあります。
①開発した人がそのまま量産まで担当する(多能工化する)
⇒ 初めから量産性を考慮するため、開発期間は1/2になる(井深大)
②コンカレントエンジニアリングを実践する
⇒ 生産技術者が開発段階から参画し、横ぐしをの役割をさせる
③リスクマネジメントを実施する
⇒ 特定分野の場合、起こり得るトラブルを列挙するのは、比較的容易である
④開発プロセスツール等の活用
⇒ 3DCAD、シミュレーション、QFD、TRIZ、品質工学、プラットフォームの標準化、フェールセーフ、フールプルーフ、FMEA等を選択して活用する
⑤高度技術保有のコンサルタントを活用する
⇒ 自社で、すべての高度な専門性を保有するのは至難の業となるため、外部資源も有効活用する
(2) 多能工化(プロジェティスタ)の実践
「開発した人がそのまま量産まで担当する」は、大先輩であるの井深大氏の直伝です。筆者もいくつかのプロジェクトで実践し、有効性を証明してきました。他社で実施しているところが少ないため、社員の動機づけや差別化施策にもなります。最近、PC電池の発火事故、ガス湯沸かし器や石油温風ヒーターの発火事故、洗濯機の発火事故、自動車のリコール問題など、品質問題が多発しています。考えられる原因として、技術の高度化、複雑化、技術や生産のアウトソーシング化、生産の海外展開などが複雑に絡み合っていると考えられます。イタリアでは、スペシャリストやエキスパートではない「プロジェティスタ」というキャリアモデルが存在しているそうです。プロジェティスタとは、マーケティング、企画、デザイン、開発、生産のビジネスプロセスに関与して、クリエイティブ業務を遂行するイタリア版超多能工リーダーのことです。
(3) コンカレントエンジニアリングの活用
これは、コンピュータ支援技術( CAD、CAE 等) を用いて、開発から生産までの仕事を並列的に処理し、製品開発から生産までのリードタイム(期間)を短縮したり、品質向上、コストダウン等をはかる考え方です。実際には、関係する部門から人を集めて開発チームを構成しています。仕事の進展に合わせチームリーダーや仕事の場所、やり方を変えていきます。ボトルネックとなるところを迅速に検出し、チーム内で全ての決断を下してボトルネックを解消していきます。必要に応じて、設計技術者や生産技術者が相手の部署に駐在して不足な情報を補い、仕事を加速するわけです。開発した人がそのまま量産まで担当することができない場合の次善の策になると考えます。ここで、横ぐしを通す役割に最適な人材として、生産技術者を推薦しています。なぜなら、ものづくりの全体像を俯瞰できる立場に一番近いからです。
(4) リスク・マネジメントの活用
質問のように、特定分野に限定すれば、起こり得るトラブルを列挙するのが、比較的容易となるためです。ここでは、実践的な重点管理項目(重大領域)とその選び方も紹介します。これは、優先順位順となっています。
①作成した計画の中で、最も危険な領域はどこか?
②もし失敗したら致命的なところは?
③スケジュールの厳しいところは?
④全く経験のないところは?
⑤複数部門と関係するところは?
⑥スケジュール変更の可能性のあるところは?
⑦予算的に厳しいところは?
⑧責任があいまいなところは?
⑨指示・連絡のステップが多いとこtろは?
⑩環境変化の影響を受けそうなところは?
回答者:ぷろえんじにあ代表 粕谷茂
|