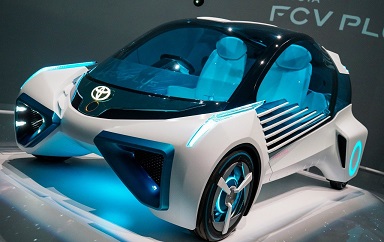
IATF 16949 は、ISO 9001に自動車用システムや部品の製造に必要となる業界固有の要求事項を追加した自動車産業のセクター規格です。APQPを解説する前に。IATF 16949についてです。
1.IATF16949のゴール
「品質マネジメントシステム」とは「品質方針、及び目標、並びにその目標を達成するためのプロセスを確立するための相互に関連する又は、相互に作用する組織の一連の要素」とISO9000に規定されています。重要なところは「…目標を達成するためのプロセスを確立する…」です。「ISO9000」は「製品及びサービス」など、様々なものが対象になり得ます。これに対して、IATF16949が目指すところは、自動車メーカーとそのサプライヤー、即ちB to Bの共通目的、それは安全性が確保され、リコールにならない品質の良い自動車を造ることです。日本製の自動車は、世界的にも故障しにくく、品質が良いと一般的にいわれています。しかし、運転するドライバーや自動車メーカーは、品質をどのように評価することができるのでしょうか?
2. APQPの背景と本質
1994年、北米自動車業界はISO9000シリーズ規格に各社の個別要求事項を加えたQS-9000と呼ばれる北米自動車産業界の品質マネジメントシステムを開発しました。APQPは、フォードモーターが他産業で使われていたプロジェクトマネジメントを応用し、サプライヤーの品質管理に運用していました。これをQS-9000に含めて業界標準としたのです。
APQPとはAdvanced Product Quality Planningの略で「先行製品品質計画」のことです。これはISO/TS 16949(ISO 9001をベースとした自動車産業向け品質マネジメントシステム規格)を構築、運用するために必須なコアツール(中心となる手法)の一つです。APQPは、自動車の品質マネジメントシステムTS16949の先行製品実現計画部分に対応し、運営管理の要領を規定しています。 製品実現のステップは①計画、②製品設計、③工程設計、④製品、工程の妥当性確認、⑤量産の5段階に分けられて、それぞれの段階での実施項目と入力、出力事項が定められており、プロジェクトのリスク低減が図られます。 実行する際には、コントロールプランの作成が必須であり、このプランを中心に管理が進められてゆきます。
コアツールと呼ばれるFMEA、SPC(統計的工程管理)、MSA(測定システム解析)はAPQPの計画にも組み込まれ、品質の作り込みに有効な手法(ツール)と位置づけられています。
PPAP(生産部品承認プロセス)は、サプライヤーが納入品質・デリバリー・要求事項への適合性をOEMメーカーに実証するための証拠書類と保証書(PSW)で構成されています。承認プロセスのステップが明確になり、コアツールをサプライヤー内で有効に活用できることで品質保証レベルを格段に上げられるのです。
3. APQPの実施ステップとは
2.製品設計と開発
3.工程設計と開発
4.設計と開発(製品・工程)の妥当性の確認
5.量産・評価・是正・改善