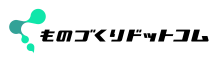
上司からはサイクルを上げろと言われますが、それは無理なので別の切り口を探しています。

装置産業の生産システム開発、設備設計、経済性工学セミナー講師などの経験から感じたことを述べます。この場は手法を主に紹介しているサイトですので、主に経済性工学の視点で整理したいと思います。
具体的なデータを提示していただければ、すぐどうすればよいかの答えは出せると思います。本質問内容では一般論で回答するしかないため推測での判断となってしまいますことをご容赦願います。ただ、生産性の低い機械で受注できていることを考えると、生産数が少ない等の理由で競合がないとか特殊なノウハウの必要な製品であることも考えられます。
上記を踏まえ、以下の2つの視点で考えてみます。
(1)サイクルタイムの速い機械と入れ替える
装置産業の場合には、生産性は機械のサイクルタイムでほぼ決定されてしまう例が多いと考えます。償却が終わっている機械ということですので、10年以上古い機械であることが推察されます。機械のサイクルタイムは、最新の機械と比較すれば、2培ぐらい違うのではないでしょうか。少なくとも30%最新の機械は速いと推測されます。
ここでは、分かりやすい数字にして結論を述べます。例えば、サイクルタイムの違いが30%だと仮定すると、8時間/日の稼働だとしても、10名の作業員の場合、約3名の省人化が可能となるわけです。この省人効果だけでも2000万円ぐらいの機械を購入しても4年程度で回収できてしまいます。装置産業の場合には、機械の稼働率が生産性に寄与しますので交代制勤務が一般的となります。そすることでさらに回収期間が早まります。
(2)別の切り口からの解決策
おそらく、現在使っている機械は単能機であるt思われるため、成形後のバリ取りや仕上げ処理等で人海戦術をやっておられる可能性もあります。そこで、簡単な治工具設計で生産性を上げることも可能だと考えられます。ただし、2交替、3交替とシフト勤務を導入すれば、見かけ上の生産性は上がりますが、最新機械を導入する場合と比較すると、大きな機会損失となってしまうことも考慮しなければならなくなることを付け加えさせていただきます。
ぷろえんじにあ 代表 粕谷茂
|
日本コストプランニング㈱間舘と申します。
まず、ご質問の内容を確認させていただきたいと存じます。
生産性という言葉ですが、具体的には、1日(定時間)の生産数量を増やしたいということでよろしいでしょうか?
運転サイクルは、食品包装容器を成形する機械のサイクルタイムとの認識でよいでしょうか?
上記がYESであることを前提に申し上げます。
成形機の稼働率を把握されているでしょうか?
一定時間(就業時間)内に成形機は、どれだけの時間稼働していますでしょうか?
つまり、設備機械の停止時間がどの程度になっているか、停止してしまう要因は何であるのかを整理することです。
これらについて、現状を把握することが必要です。
停止の要因には、何があり、どの程度発生しているのかを数値で掴まえることです。
そのうえで、停止要因への対策を実現性や経済性の面から検討し、改善計画を立てることです。
トヨタ自動車でも古い機械が現役で動いています。(40年以上前の機械が動いていました。)
この他にも、成形機の生産スケジュール(作業計画)の組み方や成形機の段取り時間を短縮するなどの方法が考えられます。
簡単ですが、別の切り口ということでご紹介させていただきます。
|
工場ですぐ使える品質改善技法の開発と普及活動を行っている高崎ものづくり技術研究所の濱田と申します。
新しい機械との入れ替えや、サイクルタイムを上げることができないという前提で改善案を考えてみます。
そこで登場するのが可動率です。
可動率とは、「設備を動かし、生産を行いたい時に、正常に動いてくれていた時間の割合」を指します。 例えば、設備を運転しようとしていた時間が8時間だと仮定します。しかし、実際にはトラブル等が発生し、動いていた時間は、6時間だったとします。その時の可動率は、6時間/8時間で計算され75%となります。トラブル以外に、注油点検、調整時間、切り替え時間、段取り時間なども機械の可動率を下げます。
まず可動率はどれくらいかを実測して把握し、可動率を下げている要因を洗い出します。その要因一つ一つを短縮するための改善を実施します。
また工場の能力はネック工程の能力以上には上がりません。しかしそのネック工程の機械がフル稼働していない場合も多いのです。ネック工程はどこか?その工程は100%可動しているか?に注目して改善を行っていくことをお勧めします。
|
クリーン化が専門の清水です。
減価償却がとっくに終わっているということですが、これは儲けが増大している、つまり安く製品が作れるということではないでしょうか。
運転サイクルをどう上げるかですが、“サイクルを上げると負荷に耐えられずすぐにエラーが出る”という部分が良く見えていないので、どのような問題がわかりません。
毎回出るエラーは同じでしょうか。エラーの内容を分類、分析することで、対応方法が見えてこないでしょうか。
直ぐに止まってもすぐに復帰できる内容にも見えます。すると部品交換等の発生は頻繁にはないということですね。
サイクルをエラーが出る直前までを上限にし(恐らく経験的な数字があると思います)、そこでできることはありませんか。
例えば、製品加工中のサイクルを上げても、除材、給材時設備が休んでいるとか、給油が必要だが、その時は設備を止めて実施しているようなことがあれば、自動給油化はできないのか。
段取りや切れ替え作業がるとすれば、それに時間が取られることなども考えられます。
段取り作業があるとすれば、内段取りを外段取りに変更し、時間の短縮が図れないか。また、切り替えロスを最小化できないか。
前後工程の製品加工ピッチと同期していないとか、距離が少し離れていて、簡単な移動など手作業が入る時に何らかのロスが生じることが無いか。それらを少しずつかき集め、停止しない範囲での最大のサイクルを保ちながら、ロスを減らせないかを考えて見るのも良いかもしれません。
大手メーカーでも、例え0.5秒のロスも改善しようと工夫、苦労しているところもあります。案外着眼の仕方で、改善できることがあるかもしれません。
記された内容では、状況が把握できませんでしたので推測で色々書きました。
私の思いついたことの羅列も、ご理解いただけないかもしれません。
着眼点を記します。
IE技法があります。作業の無駄を見つけて排除する。機械の稼働率を上げる内容です。上記羅列した項目を照らしてお考え下さい。
具体的には、
① 製品工程分析―停滞や運搬の減少 ここに設備の稼働が巻き込まれていないかです。
② 作業者工程分析―手待ちや移動の減少 停止した設備の復帰のために移動距離が長いとか。
③ 動作分析―無駄や無理な動作を減少させる。
この他にも色々ありますが、エラーが出るたびに復帰作業が必要だとすると、それをやる人が近くにいない。わずかでも移動時間があるとか、作業者が休憩時間に停止していて復帰遅れがある。或いは、担当外の人が復帰する時に時間がかかる。などがあるとすれば、作業の標準化も必要です。
色々な切り口から攻めて改善する。例えわずかでも積み重ねれば大きな改善になります。
また、パレート的に無駄、ロスを並べ、効果が大きい方から手を付けることも必要です。
上司がサイクルを上げるよう言ってきた時、多面的に分析した結果をもとに相談してみたらどうでしょうか。もしかすると、安易に考えているのかも知れません。
また、極限の状態であれば、それを知って貰い、一緒に考えてもらうことも良いと思います。
どのような雰囲気のやり取りなのかわかりませんが、感情でのやり取りではなく、データでものを言うことの方が説得力はあると思います。
このようなアドバイスしかできませんが、何か参考になる切り口でも見つかれば嬉しいです。
|