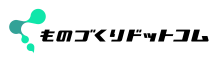
弊社の工場は、改善を行っても、数年すると元に戻ってしまう、担当者や管理者が変わると引き継がれない、何年かごとに同じ改善を繰り返している、という問題があります。歩留りや原価も良くなっては悪くなりまた良くなっては悪くなりの繰り返しです。
規定化しISO登録を行う、教育を行う(体系化されてはいません)、過去の改善を社内共有フォルダにて共有できるようにする等行っておりますが、本質的な組織改善にはなってきませんでした。(改善発表会は数年前までは行っておりましたが今は行っていません。)
尚、品質保証の観点からは、そのための専任者と従業員も大分増員し、ハードも整え、教育も繰り返し、トップからの発言も多く、決められたことが守られるよう、会社を挙げて推進されております。
この辺りの違いも焦点にしながら、本質的な要因を分析し、改善したことが継続しスパイラルアップし続ける組織つくりを行っていこうとしております。改善は、一旦火がついても、なかなか本人への待遇リターンもなく、いつしかやらなくなってしまうことも多いです。
本質的に大切なこと、肝となること、工夫事例等、ご教授頂きたいです。よろしくお願い申し上げます。

トリニティプログラムの野中と申します。 ご質問内容をみると典型的な改善がうまく進まないケースのようです。過去のものづくり改革経験からアドバイスさせて頂きます。
過去のものづくり改革支援経験から問題点を想定すると
(1)経営トップの指示が管理者に浸透していない(徹底されていない)。
担当者や管理者が変わると継続しないのはそのため。後戻りしていることを知らない、またはそのことそのものを許している。
(2)経営トップが工場を巡回し現場視察・意識向上に向けた取り組みを行なっていない。本来は週1回程度各職場を巡回し、改善活動のヒアリングと指導などを行なうことが必要です。
(3)会社全体・工場全体或いは各職場などであるべき姿、目指す姿が描けていない。 日々の改善は半年や1年後の目指す姿に向けた活動という意識が少なく、場当たり的。また あるべき姿・目指す姿と現状分析を行ない、改善の方向性と改善課題を整理する必要があると思われます。
(4)自律的な改善を行なう意識付けができていない。
改善はするべき、やるべき、でも担当者も変わったし誰もやらないし・・・。 という悪循環になっている。従業員が危機感をもって活動する意識が低い。
(5)改善は働き方改革の一つです。自らの仕事がやりやすく、作業環境を整備するものですが単にコスト削減などに視点がいっている。5Sの本来の趣旨が徹底されていない。
などが問題点として想定されます。
つまりスパイラルアップの改善を進めるためには、上記課題を解決する必要があると思われます。尚、上記課題は全てある工場では全て行なわれています。ご参考まで。
簡単ではありませんが、必ず達成することができます。
成功を祈念しております。
|
お問い合わせの問題を改善活動のとらえ方と認識して回答してみます。
1970~80年代の日本の改善活動は個人の幸せが会社の幸せ、そして国の幸せにつながるという暗黙の了解があった時代背景があります。戦後のゼロからの復興に日本人が一丸となりえた懐かしい時代です。功なり、Japan as No.1などというお世辞に浮かれている間に、失われた10年、20年・・となって来ています。確かに、日本人は戦後復興を奇跡的に成し遂げました。しかし、その後が続かないのが、今の日本の最大の問題であると思います。
そこで、かつての改善活動の遺産を今に再興するためにイアデアを如何に紹介しますのでご検討ください。なお、ハウツー(How to)ではなく、ハウホワイ(How why)、ハウファット(How what)の視点での回答として、ご検討ください。
改善活動とは、「仕事を通じた学習の場創りである。」という認識です。人は何で学ぶのか?という疑問を原点に、「幸せな人生を送るために」、そのためには、1日の三分の一の時間を占める、仕事んついて、「良い仕事をするために」、そして良い仕事の結果として「良い製品やサービス」が提供される。この連鎖を前提に、組織が改善活動をマネジメントする。
以上の前提から、改善活動の主体である現場の個々人がどのような夢(ありたい姿)を描いているのか。その一方で、組織が目指す夢(ありたい姿)はどのようなものか。これは、社是、社訓、ミッションなどで表示されている。この2つ、個人のありたい姿と組織のありたい姿の共感点を見出し、これをつなげるための工夫をすることが改善活動を指導、展開する職責を持つ人間の使命と考えてはどうでしょうか。
以上が自らを変革し、組織を変革する人材育成のコンセプトになります。その解決法は各社、各自が工夫することで組織のイアイデンテイテイ(独自性)が生まれると思います。
やらされ改善からやるぞ改善に変革するための1アイデアを紹介しました。
|
現場ですぐ使える品質改善技法の開発と普及活動を行っている高崎ものづくり技術研究所の濱田と申します。
改善活動がなかなか良い方向に回っていかないという悩みは多くの企業で共通的に見られる現象と考えられます。
私は、大きくは2つの問題があると考えます。
まず一つ目は、他の先生の回答例でもご指摘のあるように、会社全体・工場全体のあるべき姿が描けていない、経営トップの指示が浸透していない、という問題です。
二つ目は、改善活動の必要性は理解するが、日常業務が忙しいので、そちらを優先してしまうというものです。つまり、日常業務と改善活動は別物であると考えてしまっていることです。そこで、身の回りの簡単な項目を改善してお茶を濁してしまう、部分最適な改善に終始するため、一つ目の理由と重なって、本質的な改善が進まないのです。
しかし、会社全体・工場全体のあるべき姿を描き、経営トップから明確な指示を出せばいいと考えてもこれは現状では困難な場合が多いと思います。経営者の責任にしてしまうことは簡単ですが、経営者の立場で考えると、「あるべき姿」を描くために必要な「現状の姿」がはっきりと捉えることができないのです。現状の姿を捉えることで、課題が見え、あるべき姿の設定と現状とのギャップ、強化すべき項目が初めて明らかになってくるのです。
例えば「生産性向上30%」という目標を掲げても、社員はどのような動きをすればいいか、皆目見当がつきません。
つまり、日常の企業活動が見える化され、経営者に正確な情報がタイムリーに入る体制が整っているのか?というと、どうもそうとも言えません。管理層以下、現場の第一線の社員まで、仕事の状況、課題を見える化して、経営層にまで届くような仕組みを作らない限り、経営者に指示を仰いでも、明確な方針は示せないことになります。
従って、改善活動の必要性は理解するが、どこに目標を定めて改善を進めていくかが不明確であること、また日常業務が忙しいという理由から、業務改善の活動自体の優先順位はそれほど高いものではなくなり、社員自身にとっては「自分たちでできることをやり、改善活動はこれで終わらせよう」という流れを作ってしまうことになります。
そこで、経営者も第一線の社員も、企業の活動の最終目的は何か?またそのために自部門はどのような目的でどのような業務を行って利益や、生産性向上に寄与するのか?そのために自分は何をなすべきかをよく考えることが重要です。
そう考えたときに、現状の業務はどうなっているか?本当に利益に貢献する業務を行っているだろうか?ムダはないだろうか?と、業務フローを作成し検証する必要性が生まれます。
そもそも製造業の一番の目的は顧客の望む商品、サービスを提供し適正な利益を得ることです。そして、社内を見ると生産活動のムダを省いて生産性を上げることです。これは、間接部門も直接部門も共通した目的で、活動を行っているはずです。
日常の仕事に流されていると、ついこの基本を忘れがちになります。まず全員が、自らの仕事の現状を直視し会社の目的に沿っているかどうかを検証することから始めるべきではないでしょうか?
|
多くの企業の安全衛生教育の手伝いをさせて頂きている中で、継続的な取り組みについては各企業が苦労されているところです。「品質」などとは、多少の相違はあるかと思いますが、各種活動がうまくいかない会社によくある特徴を示しますので、参考にして頂ければと思います。
まず、初めに確認したいことは、トップからの発言が多いといいますが、
本当の意味での改善という事にどれだけの思いをもっているのでしょうか。ワーカーは管理者の思いなど簡単に見抜いていますし、管理者の方はトップの思いも見透かしている事が多いです。経営者は管理者の、管理者はワーカーの「知識レベル」と「意識レベル」が絶えずそれぞれの上を
行っているのかが重要になります。
ワーカーのヤロウというタイミングの際に管理者(会社)のタイミングが合わない(特にその時の会社の優先順位が普段から言っている、行っていることと違う)場合は継続が出来なくなります。その際、ワーカーは「自分がやらない理由を管理者にの責任」にします。その、ワーカーを見たとき管理者は「自分が出来ない理由をワーカーの責任」にします。この繰り返しをマンネリ化として片づけている会社が非常に多いです。その部分を再度見直し、管理者、ワーカー双方が認識を新たにする事が大切です。
次に、5Sでもよくありがちなことですが、目的と手段の設定があいまいな場合が多いです。きれいにすることが目的ではなく、手段として使うことによって、目的は「〇〇です」というように改善発表を行うことが目的になっていては何も進んでいきません。「○○を良くすること」が目的であって、そのための手段として「○○活動」を行っていくというような、趣旨説明を丁寧に教育すると良いのではないでしょうか。
教育を行う際に気を付けなければいけないことは、教えられる側は、まったくの白紙の状態ではない事に注意しなけれあいけません。各ワーカーにはそれぞれに変えたくない色、はじめからもっている色があります。また、担当者が変わると元に戻るとのことですが、前任の担当者がつけた色と、新たな管理者が付けようとしている色が違うと、戸惑いも出てきます。教育について体系化されていないとのことですが、対象や時間、内容等、教育計画を立てることが必要ではないでしょうか。
|