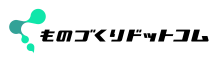
生産の60%は自動車メーカーのTier2として、ほぼ同仕様の製品をインラインで流していますが、受注量の減少に対応して自動車に限定しない特注品に注力しています。ここ7年ほどの積極的な営業の成果もあり、順調に受注量/金額を伸ばしていますが、慣れない多品種少量製品が増えたために管理工数の増大に苦しんでいます。
また購入部品のロットも小さいため、単価の上昇は相当のものがあり、なかなか黒字化ができない状況です。
多品種少量生産におけるコストダウン(原価低減)の方法がありましたら、ぜひご教授願います。
[これは運営者による仮想の(しかし、ありがちな)質問です]

5S/クリーン化の清水です。
多品種少量生産での ①管理工数大 ②生産ロットサイズ少→単価大 ③コストダウン方法(原価低減)についてお答えします。
私は特に専門技法等を持ち合わせていません。また該当工場や製品を見ていないので、想像し乍ら思い当たることを拾って見ます。
結論は小さな物や小さなことにも着眼し、改善の積み重ね、つまり、無駄取りと改善の繰り返しが最善策と考えています。
着眼点を以下に記します(順不同)。
1.多品種少量生産は、流動製品の切り替えが頻繁になります。
この場合切替え、段取ロスを如何に少なくするかもポイントです。
対策として考えられるのが、
(1)切り替え、段取り作業の標準化。効率良い切り換え方法を標準化し、誰でも同じように、しかも速く切り替えが出来るようにする。また更に良い方法は無いかの改善の繰り返し。
①方法は良いか 効率的か 切り替え時間は最短か 安全か
②作業動作に無駄が無いか 無理な動作はないか
③切替治具、工具は近くにあるか、幾つもの細かな作業はまとめられないか(切替えのワンタッチ化)
・段取作業をする場合、内段取りか外段取りか
内段取りは切替え時、ライン停止し切替え作業をする為停止時間が長い。生産ロス。
外段取りは、ラインを稼働しながら、次製品流動の段取りをラインの外でやるため、切替え時間が短縮でき生産ロスは少ない。
2)生産計画の範囲で可能な限り同機種を纏めて流動出来ないか。
①切替え回数の削減
・慣れた作業の繰り返しで作業能率の低下防止
作業能率の確認
②同作業でも機種により作業時間に差が出ていないか
・各工程の作業スピードの改善
各工程の作業量を山積み、山ならしして平準化する。工程間の手空き、溜まりの最小化
③受注の状況から先の生産計画が見込める場合、同製品の部品を機会損失(過剰在庫)にならない程度に纏め買い出来ないか。(購入単価ダウン)
2.工程間、ライン間の運搬方法に無駄は無いか。自動化出来ないか(活性分析等活用)
・作業、工程間の接続間を可能な限り短くする。
活性分析は可能な限り移動、運搬し易い状態にするかと言うことです。小さな着眼点ですが、改善の余地があります。
又、重量物を持ち上げる時、腰を傷める等の労働災害の未然防止にも役立ちます。
3.やり直し、手直しは無いか。製品流動に支障が出ていないか。
4.作業の引き継ぎ等に問題はないか。確認や見直し等のロス防止。効率的な引き継ぎ
5.工程設計全般見直し、無駄は無いか。小さな無駄も拾う。
6.製品設計、共通化出来る部品、原材料は無いか。作業性維持、原価低減。
7.納入部品、原材料は良いか。
ライン投入前に洗浄、手直ししていないか。隠れたコストの見える化。
8.省エネ面のチェック
①クリーンルーム内での作業なら局所クリーン化出来ないか、ノンクリーンルーム化出来ないか。
クリーンルームは、エネルギー費用の割合が高い。風量を落とす、局所化する等でコストの見直しを。
クリーンルーム化を過剰品質と判断、上記取り組み企業も多い。
・照明も適切に間引く。PCも節電モードに(画面の表示、明るさ)
・不要物排除。未使用のものに電源が入っている等。不要物を排除することで、空きスペースが発生したり、安全の向上にも繋がる。
雑然としていると作業ミスの誘発。事故、災害や作業ミスもコストに効いてきます。
・高熱の設備には熱飛散防止の工夫を。設備や空調の冷却コストが減る。逆に品質に影響ない場合、室温を高め設定し冷却コスト低減に貢献。
9.原価の分析はきちんとしているか。(管理、経理、設計、品質、技術、現場)
・減らせることは無いか。
・作業員の意識は高いか。小集団活動等を活用、テーマの共有、問題の提起してもらう。TOPダウンとボトムアップの関係が良ければ、作業員の会社を良くしようと言う雰囲気や参画意識が醸成され、小さな問題点への気づき、改善に繋げて貰える。
良く特性要因図の作成時、現場で実際を見ながらが効果的と言います。
作業者はやり難いこと、標準には無いがやり易い方法等に気が付いていることが多い。それを拾いたい。
管理や技術、品質部門が机上で考えるものとまた違った見方が出来ます。
余談ですが、私は会社在籍中は長くクリーン化を推進して来た。
その中で、情報を沢山持っているのは、現場のオペレータと掃除のおばさんでした。
掃除のおばさんは専門業者でしたが、こんなところまで見ている、気が付いていることに驚きました。
・無駄が出ている工程は把握できているか、その問題は把握されているか。その部品、材料 F(不良)コストは?
・不良は、速い段階で発見、除去されているか。最後まで手をかけ流動し、最後に初期に発生した不良も含め検査、出荷工程で排除していないか。余計な費用発生と数量不足。
・多品種少量生産は、納品数に対し投入がぎりぎりだと、不良発生時納品不足になる。又追加投入して不足を補おうとすると納期遅れが出る。従って安全を加味した投入になり、結果的に過剰生産になる。
これを同製品の少し先の注文も読めれば、一緒に生産する等してロスを抑えられないか。
10.製品品質の見直し。歩留まりを極限まで追い込む。目標は高い方が良い。
又付加価値を付け過ぎていないか。削れるものは無いか。逆に高付加価値をPR し売値を上げられないか。
11.作業の見直し。 作業そのものに着眼し無駄を見つけ、排除できないか。
・作業観察し、作業分解して無駄を見つける。動作が効率的か(動作経済の原則)、製品の流れに戻りはないか(製品流動や人の動きの流れ矢線化)、手直しやり直しは無いか。戻り作業は製品流動の流れを阻害し、後工程が手空きになる。納期確保の為の残業や休日出勤対応で間に合わせ、結果コストアップに繋がることの防止。
・細かな事だが、作業標準等の書類が手元に無く、必要になった都度遠くまで(管理職の周囲)見に行く、取りに行く動作が発生していたり、見に行くのが面倒で思い込みで作業をし、不良品を作ってしまったと言う事例もある。
管理職は、作業標準は頻繁に見ないのに手元に置きたがる。
・作業者の熟練度を上げる。兎角作業の遅い人ばかりに注目してしまうが速い人にも注目する。右肩上がりの習熟度が横這いになると、その人の能力は最大に到達したとか、熟練者とみなされノーマークになる。
この状態をプラトー(高原)と言うが、何かのきっかけで現状打破し、再び技能、能力が右肩上がりに転換することもある。
私は、長年現場を這いずり回っていたので、現場寄りの見方、考え方が中心です。
その中で小さなことでもいかに着眼し拾い出すか、積み上げるか。究極を目指すと言うアドバイスしかできません。
周囲の力を集め、より多面的に着眼と改善、その繰り返し、継続だと思います。
このこのことは手綱を緩めてはいけません。日々前進です。
|
製品設計、電子部品や半導体の生産システムの検討、治工具設計、ロボット開発などを実施してきた経験から感じたことを述べます。結論を一言で言えば、『あらゆる視点で、徹底的にムダを排除すること』になるかと思います。具体的検討項目は、次のようなことです。①製品在庫、仕掛在庫を減らす。②品質を作り込む。③設備稼働率を向上させる。④労働生産性を上げる。⑤標準化、共通化、トリミング等の設計変更等により、材料費を低減する。⑥海外生産も含めた内外作区分を見直す。⑦原価の視える化を意識的に実施し、従業員で課題を共有化する。⑧プロダクトミックスを考え1個当たり限界利益の大きい順に生産を優先させる。⑨ラインのボトルネックを探し出し、段取方法、治工具化、自動化、ロットサイズ見直し等で平準化する。⑩物流方法を見直す。
この場は、ものづくり革新ナビですので、手法についても少し具体例を提案します。主に自動車部品を扱っていることで、既に実施中とは思いますが、効果的手法の一つは、トヨタ生産方式を徹底的に実践することだとです。また、VE、TRIZのトリミングなどによる部品点数の削減、IEを駆使した工程改善も一定の効果が期待できます。さらに、生産ライン方式の最適案の選択は、重要施策になるでしょう。セル生産方式として、一人屋台方式やU字型ラインが検討に値します。例えば、日本での生産ならば、多能工の替りにフレキシブルロボットの導入なども有効かもしれません。さらに、最近の検討課題として、3D設計を導入したデザインレビュー、ITシュミレーションを駆使した生産管理改革や生産システム検討も、対応策と効果がすぐ判断できるため、効果的です。そして、施策の抜け漏れを防ぐのに効果をあげている筆者オリジナルのマトリクス分析法を紹介します。1つ目が、横軸に、生産・調達・作業を配置し、縦軸に、ヒト・モノ(材料)・機械等を配置したマトリクス表です。2つ目が、横軸に、生産・調達・作業を配置し、縦軸に、Q(品質)・C(コスト)・D(納期)を記述したマトリクス表です。各々のマトリクスの交点に、課題と対応策を抜け漏れなく議論して記述します。それらに優先順位をつけて実行に移します。
若い頃、前の勤務先とトヨタ自動車で互いの強みのスキルのノウハウを提供し合う異業種交流会を実施したことを補足しておきます。筆者たちは、大野耐一氏自身がまとめた社内教育用の分厚いテキスト(まだ市販されていない)をいただき、チームでトヨタ生産方式について分析、学習を重ね、トヨタ生産方式のノウハウを理解しました。今でも、大野耐一氏の言葉が参考になると思いますので、一つだけ紹介します。「手品・魔術には種があるように、この現場技術(トヨタ生産方式)にも種がある。種明かしをすれば、『ムダを排除--徹底的に--である。』→『ムダを排除するには、ムダを見つける目を養う。』→『見つけ得たムダの排除のしかたを考える。』の繰り返しである。いつまでも、どこまでも、たゆまずにである。」
回答者:ぷろえんじにあ代表 粕谷茂
|
高崎駿巧ビジネス コンサルティング・オフィスの浜田と申します。
多品種少量生産におけるコストダウンをどのように行うか?というご質問ですが、ここで御社の特殊性を考慮しなければならないと推察いたしました。
「創業35年、生産の60%は自動車メーカーのTier2として、ほぼ同仕様の製品を・・・」とのことですが、この業務と並行して、「慣れない多品種少量製品」が増えたとあります。つまり、同じ工場の中で全く違う2つの生産形態を、取らなければならないというところに難しさがあるような気がします。
それは、需要がある程度先まで読め、安定した生産が見込める今までの自動車業界の仕事と、需要が全く読めない特注品の新しい仕事では、管理のやり方を180度転換しなければならないからです。35年間慣れ親しんだ管理方法を捨て去り、新しい管理方法に頭を切り替えるには、現状のモノの作り方の固定観念を否定するところから始めなければなりません。
今まで、自動車業界の仕事を長年経験されてきたわけですから、ムダの排除、5S、在庫の削減などの工程の改善は徹底して進めて来られたと推察します。
■ここで、具体的に着目しなければならない点は
1.全く性質の異なる製品を混在して管理し、生産しなければならない事
2.「慣れない多品種少量の製品」が増え、管理工数が増大したこと
3.「小ロット購入部品」で、単価が上昇したこと
の三つです。
■これらの課題を踏まえた上で、私の工場改革案、3項目を以下に示します。
1.生産計画、調達計画、生産管理の方法を新たに構築し、リードタイムを短縮する
2.そのためには1の業務部門を強化し、将来的に自動車製品の業務部門と分離させる
3.セル生産方式を採用し、一個流し生産を行い、生産性を向上させる
■まず1ですが
現状の受注から、製造に至るプロセスの流れを見える化、問題点を浮き彫りにし、調達コストの削減、リードタイムの短縮を徹底的に行います。
・受注処理のどこに問題があるのか?
・もっと事前に受注時期、納期情報を得る方法はないのか(フォーキャスト等)?
・部品発注情報を発注先に早く伝えるにはどうしたらいいか?
・少ロット部品の調達でも、価格が上がらない発注方法(内示発注など)はないか?
・長納期部品の安全在庫をどのように持つか?
・平準化生産を行うために、生産計画、作業進捗管理をどのように行ったらいいか?
などの問題点・課題を抽出し、一つ一つ地道に解決していきます。特に部品納入業者には、無理やり要求を突きつけるのではなく、パートナーとして、互いに利益が出るようにアイデアを出し合うようにします。
■2について
これには、従来の発想を転換し、管理を分離する必要があるため、管理部門の専任化、別組織化を行う必要があります。80名の少数の組織ではありますが、改善を進めて行く過程で、少人化したスタッフを管理部門に回すなどのやりくりを行いながら進めます。
■3について
セル生産方式を採用して、一日毎の平準化生産計画のもとに、作業管理ができるように徐々に改善を行っていきます。それには、作業指示書(作業の標準化)、多能工化、ポカよけなどによる品質向上策も同時に進めなければなりません。そういった意味で、作業現場も自動車部品の組織と分離するなどの見直しが必要になってくると考えられます。
■最後に
35年間の組織風土を転換しなければならないのですから、経営者がトップダウンで改革の方針を示し、自らの決意を行動で示す必要があります。目に見えるハード面の改革より、ソフト(考え方、管理方法)の改革に重点を置かなければ、目に見えた効果が出ないと考えます。
それには、「改革プロジェクト」を編成し、半年、あるいは1年の長期計画で改革を徐々に進めていく必要があります。大事なことは、達成目標を明確に示すことです。目標を明確にしなまま進めると、手段が目的化し、途中で挫折してしまうケースが多いものです。
半年後、1年後にどうあるべきか?具体的に「リードタイム短縮50%」「生産性向上30%」など数値で目標を掲げ、原価低減によって、利益を確保する過程を見える形で提示し、毎月達成度をチェックしながら、計画の見直しなどのフィードバックを掛けていく「改革継続の仕組み」をしっかり構築していくことが重要です。
|