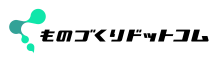
なお私は、このバックの企画開発は1年ほど前から担当になりましたが、この外注先での製造は何年にもなり、大きな問題もなく、協力関係もうまくいっております。
そんな外注先に、今回、新しい生地を作ってバッグを作ってもらうことにしました。
最初の試作は、問題なく出来上がってきました。特にその生地に問題はなく、工場からも、問題ありとの連絡はありませんでした。なお、試作数は一つです。
2回目の試作は、別の箇所の改良が目的でした。できあがった試作は最初の試作同様に、生地の問題はありませんでした。
しかし、その後、外注先から、その生地は使えないと連絡が来ました。製造上に問題があるとのことです。
その後、色々と対策を相談したのですが、外注先は、頑として製造不可とのことで、結局、その生地は採用できませんでした。
その生地は衣類には多用されているため、私は製造上問題ないと思っており、油断したかもしれません。
しかし、最初の試作の時に、製造が困難なのはわかっていたはずです。それを、2回目の試作の後に言うのはおかしいと思います。数を増やした場合にわかるような問題では無いはずです。
試作の段階で製造上問題がないか確認するのは、当然です。数を作って始めてわかる問題もあります。
教えていただきたいのは、初期の試作から生産前のパイロット的な試作をしていくのですが、それぞれどのような注意をすべきでしょうか。

いくつかのプロジェクトリーダー、新製品開発支援等の経験から、この質問に有効と考えられる意見を述べます。最近では企業と企業との連携や産学連携の動きが強まっています。このような連携をするときに忘れがちなのが、共同開発契約です。今回の質問の試作品のケースは、試作品の製造上の問題というより、共同開発契約書の未締結によって発生しているものと推測しました。研究開発のリスクマネジメントの一貫として、共同研究開発契約書作成のポイントを紹介します。
(1)研究開発の目的
目的が明確になれば、両者がその目的に向かって何をすべきか、なにを相手方に要求すべきかなどが自ずと明確になります。
(2)契約対象は何か
各当事者が 相手方に開示提供するものは何か、技術情報なのか、ノウハウ技術なのか、研究開発に使用される製品(サンプル)があるのか等を明確に記載する必要があります。
(3)情報・資料の相互開示
契約対象として開示提供を受けた情報や資料にアクセスできる人員を特定することも大切になります。また、秘密漏洩がないように開示提供された技術情報の保管も大切な業務となります。
(4)役割分担とその費用負担
共同で研究や開発をする際には、各当事者が何をするのか、その費用を誰が負担するのかを規定することも必要です。
(5)開発成果の取り扱い
契約上で最も重要な項目といえます。研究開発の過程または結果として生じた成果(技術、ノウハウ、発明等)の所属はどうするのか、この成果をどのように取り扱うのか、特許等の知的財産の取り扱いはどうするのか(共同出願か、単独出願か) 等必ず規定を設けるべきです。
(6)費用の負担
研究開発にかかわる費用の負担を明確にします。
(6)秘密保持条項
秘密情報の定義を明確にした上で、秘密情報を第三者に開示、漏えいしないよう、秘密保持の義務を規定します。秘密情報の保管・管理についていかなる義務が課せられるのかを明示します。
ぷろえんじに代表:粕谷 茂
|
品質マネジメントシステム関連を専門とする者ですが、ご質問に回答させていただきます。状況を整理すると以下のように理解します。
1.国内で機能性バッグの企画、開発を行い、試作、量産を外注。
2.外注先は、製造実績が何年もある。問題もなかった。
3.指定した布地はすでに量産実績がある。
4.指定した布地は2回の試作でも使って問題なかった。
5.外注先から、製造上の問題で使えないと連絡があった。
6.相談したが、外注先は製造不可の判断は変えなかった。
ポイントは、次の点にあると考えます。
製造上の問題とは、具体的に何か?(生産数量、コスト、品質)
試作段階までに外注先は、量産時点の数量、コスト、貴社からの
要求品質(バッグの生地として求められる評価項目等)を認識
していたのか?本当の理由は?
ご質問の「初期の試作、生産前パイロット試作における注意点」への回答
企画、設計開発から量産導入までには、ご説明のようにステップがありますが、外注先が量産を前提にする試作、量産準備ができるようなチェックリストを計画段階で準備します。そのチェックを企画段階、試作依頼の時、量産試作の時に自己評価してもらいフィードバックを受けるようにすることをお勧めします。つまり、節目を設定し、見積もりを出す時や、試作を依頼する時に段階的に双方で量産にむけてリスクの有無を確認することです。
チェックリストの内容は、Q,C,D(品質、コスト、生産数量)に係ることを盛り込みます。こうした活動は、「実現可能性検討」と呼ばれています。
また、最初のチェックは、外注先を訪問され、生産工程現場の状況も見ながら評価することが望ましいです。製造上の問題となった事象を早い段階でリスクとして検出し、対策を実施できる体制を維持することが注意点だと考えます。
|
工場ですぐ使える品質改善技法の開発と普及活動を行っている高崎ものづくり技術研究所の濱田と申します。
新製品の試作の場合、試作の位置付けを明確にする必要があると思います。つまり、試作の目的と、何を確認するための試作なのか?です。
依頼者は、量産するための製造可否判断を行うための試作と考えても、依頼を受けた側は、サンプル1個をとりあえず製作し、量産性のことは全く考えていないかもしれません。今回の事例は依頼側で当然と思った事がメーカー側ではそうではなかったという、お互いの目的が違っていたために起こった問題だと思います。
試作モデルの開発を通じて、「実際商品化した際に問題がないか?を総合的に判断する必要がありますが、その中で、メーカー側で何を確認するのか?事前に整合してから依頼する必要があります。
一般的には以下のような項目があげられます。
1.デザイン・機能・・・実物で確認評価
2.量産価格の予測・・・材料費と加工費はいくらかかるのか?
3.製造工程、品質・・・作り易さ(作業性の確認)
4.設備能力・・・新たな設備導入が必要か?金額はいくらか?
5.材料・・・供給性、価格安定性
しかし、中国や新興国で試作する場合はこれらを評価し、判定することは困難な場合が多く、リスクが伴うものと思われます。試作の時と、量産化した時とでは、全く異なった商品が出来上がって来て、一体何のための試作だったのか?といったことがしばしば発生します。
そこで新規性の高い商品の場合は、一旦国内で試作し、問題無しと判断したものを、工場にその工程、手順を伝え、量産試作する方法を取られたほうが良いと考えます。
今回は、2回目の試作とは言え、メーカー側から製造困難と通告があったため、不幸中の幸いだったと思います。
|