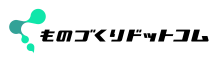
以前は材料配合比率による改善に関して実験計画法の適用法などご相談に乗って頂きありがとうございました。実務で使用するのが初めての中、アドバイスに沿って変数のスクリーニングや応答曲面法なども使用しながら一定の結果を得ることができました。
現在、鋳造凝固シミュレーション(CAEソフト)の解析パラメータを最適化して解析結果の精度向上をしたいと考えています。そこで、解析結果として計算される鋳物の温度分布や冷却速度分布と実測値の差を目的変数、各種解析パラメータを説明変数として、目的変数を最小化する最適化問題を解くことでパラメータの同定ができるのではないかと考えました。これら実験計画を立てる中で2点わからないことがあり、ぜひまたアドバイスを頂きたく質問を投稿しました。
・1点目が実際の実験とシミュレーション上の実験の違いについてです。解析に使用するパラメータ数が多く、このまま組み合わを探索するのは時間がかかるため、まずは解析結果への影響が大きいパラメータを絞り込むスクリーニング実験を検討しています。実際の実験であれば、各因子の分散分析の結果から分散比の大きい因子を選び出しますが、「シミュレーションでは実験誤差は0であり、分散分析ができないのではないか?できないとすると効果の有意性を判断する指標や基準は存在するのか?」というのが1点目の疑問です。
・2点目が実験計画の立て方、各因子の扱いについてです。解析パラメータは大きく以下の3つに分類されます。
(1) 金属材料、鋳型、中子材料などの物性値:密度、比熱、熱伝導率、液相線温度など
(2) 初期条件:溶湯温度、鋳型温度、雰囲気温度、注湯速度など
(3) 解析上使用するパラメータ:要素の長さなど物性値は同じ材料を使用する限り一定である一方、初期条件は毎回異なる値であり、製品毎に目標値も異なります。
今回パラメーターの合わせ込みをしたいのは材料物性値です。初期条件などはむしろ解析精度が実用レベルとなった後、最適な製造条件の設定を探索するのに使用するのが有用だと考えています。しかし着目するのが材料物性値だけとは言え、その他の変数もシミュレーション上ではなにかしらの値を代入しなくてはいけません。実機実験の場合は意図的に振り分けた因子以外の影響は実験誤差として扱えると思いますが、1点目の質問同様シミュレーション上では誤差が生じないため着目しないパラメーターの水準設定にも注意を払う必要があるのではないかと思います。「合わせ込みを行わないパラメーターの水準は固定値(代表値)1種のみでよいか?あるいは外乱として外側に割り付けるなどの対応が必要か?」というのが2点目の質問になります。
また、そもそもシミュレーションのアルゴリズムや評価手法が本当に正しいか?3Dモデルの定義やメッシュの切り方が適切か?という前提は確認する必要はあると考えています。その他にもシミュレーション特有の注意点などありましたら、ぜひご助言頂けたらと思います。よろしくお願いいたします。
補足1
熊坂先生へのコメント字数制限で途切れてしまいましたが、大量の水準設定に関しては幸い自前で対応できそうなのでこれを機に自動化プログラムを作成するように致します。

どなたもご回答をされないようですからSHIZUOKAの森がご参考になればという前提で回答とさせていただきます。
大変立派な文章であり、技術者としての素養が高い方と思いました。質問は大きく4個になっております。
1:実実験とシミュレーションの違い
シミュレータの初期設定は、実績のある製造での定数を代入して、応答(物性値)が同じになるようにシミュレータを調整します。この時関連する諸物性もほぼ実機近傍になるようにします。このとき製造実績のある3水準として直交表L36(本来ならカンファレンスC行列が妥当)に割り付けて諸特性を確認します。要因効果図からある程度の調整が可能です。このようにしてシミュレータを仕立てておきます。
2:実験計画の立て方
解析パラメータは3分類とありますが、原料組成、投入順番、工程条件のの3個が妥当かと思います。これらからL36(C行列がよい)の内側を割り付けます。狙い値での安定生産も実現したいので不安定要素として、組成ばらつきと温度ばらつきと反応時間を2水準毎のL4に纏めてノイズにします。
応答から、ノイズに影響されない条件(SN比、または図解法)で解析します。
3:1回目の条件
製造条件を入れて基準としてください。割り付け幅は小さくしてください。
4:アルゴリズム等は、1:でシミュレーションと実際が一致する組み合わせを最善としてください。
これで大丈夫かと思います。頑張って下さい。2017.2018のRQESに東芝機械の鋳物事例fがります。いい事例ですから参照してください。
|
追記です。
シミュレーションと実実験の合わせこみに実験的回帰分析という技法がります。田口の丸善(第3番)「実験計画法」第15章です。
ご参照ください。
|
近年の品質工学会の発表会ではCAEとの組み合わせ事例が多くなっています。品質工学のパラメータ設計手法は、実実験でも逐次実験に比べると圧倒的に効率的なのですが、制御因子8個をL18直交表に割付け、誤差因子を2水準、信号因子を3水準設定すると、108個のデータを集める必要があります。実験によっては測定まで含めて1日で108個完了するものもありますが、因子や水準によっては、数ヶ月を要することになり、現実的ではありません。最長でも数日で完了したいものです。
その点CAEは短時間で結果が出るため、品質工学との相性が非常に良いのです。是非挑戦を続けてください。
ご質問の分散分析ですが、確かに実験ばらつき、測定ばらつきがありませんから、誤差分散との比較である有意差検定はできませんが、実験因子の水準効果は分析可能です。検定しなくとも、水準効果が大きいものに注目してはどうでしょう?
ただし本実験の前に因子を絞り込むことには、若干の問題があります。予備実験の組み合わせでは効果がない因子も、ある因子との組み合わせで交互作用が発生する可能性があるからです。
折角CAEで多くの組み合わせを短時間で評価できるのですから、大きめの直交表を使って、より多くの因子を同時に分析してみてください。実実験ではL18あたりが現実的な最大サイズである一方、CAEではL36、L54、L108といった直交表使用が可能となり、実際に事例報告もあります。
もし1回あたりの計算時間が長くて、多数回実施に数ヶ月とか非現実的な時間がかかるようでしたら、メッシュを荒くするなどで計算時間を短くするように工夫してください。当然計算1件あたりの精度は悪くなりますが、例えばL108直交表であれば3水準因子の水準毎の繰り返し数が108/3=36回ありますから、実験全体としての精度はかなり良くなります。
むしろ大きな直交表を使う場合の問題は、パラメータ設定作業です。PCで数十個のパラメータを間違えずに、誤差水準を含め数百回設定し直すだけで、1回1分としても数百分となり、計算時間の数倍の時間がかかります。パラメータの設定を直交表どおりに自動で入れ替えて連続して結果データまで記録してくれるソフトウェアがありますので、導入を検討してみてください。
誤差因子については、森先生が提案するように、温度や設定条件などを使う手もありますが、CAEの場合は、全ての制御因子を上下に数%変化させて誤差因子とする方法がしばしば採用されます。これは実実験では絶対に不可能なCAEならではの方法で、有効性は高いものの、大きな直交表で実行すると千回を超える計算回数になりますから、前記自動実行ソフトの必要性がさらに上がります。
この辺りは日本規格協会の「品質工学応用講座」の「コンピュータによる情報設計の技術開発―シミュレーションとMTシステム 」に詳しいので参考にしてください。
|