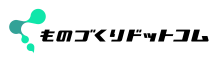
課題は取引先から供給される部品に荷姿変更です。セル生産方式を導入しており、多品種生産を行っております。システムはMRPです。荷姿のままセル台に資材をセットすること、つまりダイレクトチャージになります。①作業工数の2~3割を占めるピッキング作業を軽減し工数低減を行う。②取引先からの荷姿のまま、詰め替え作業なしでピッキングできる通函を作成する。③通函化の前後でピッキング工数の削減効果の検証を実施する。現状では、工程作業者は、通函を開梱後、一時保管(品目により別トレーに移し替え、資材棚に配置)して、作業指示に従い、セル台にセットするためのケースに、ピッキングして載せ替えております。開梱からセル台トレーに移し替え、ピッキングするまでの作業を削減することで多大なる工数削減に繋がります。同様の事例を取り組んでおられる事例がございましたらご教授お願い致します。

かなり以前になりますが、海外の自動車組立工場のロジスティックス部門に常駐していた際、日本→海外工場の自動車部品がCKD(コンプリートノックダウン:構成部品を箱詰めにして海外でプラモデルを組立てるようにして完成させる)方式で納入されていました。海外の製造現場ではまさにhebeさんと同じ方式による工数のムダ発生のため、それをカイゼンするべく、CKDのモジュール化に取り組んでおりました。これは現場での生産状況(車種・モデル)に合わせてのCKDによる供給を目指したものでした。
今回のhebeさんの製品・部材構成がどのようなものであるか分かりませんが、自社のセル生産現場への生産指示書の部品構成と部品納入業者からの納入部品はイコールであることが理想です。その際は、納入業者からの荷姿も考慮する必要があります。先のCKDの場合は決められた寸法の木枠箱内にムダなく詰め込みながらも現場の生産状況に限りなく同期した部品を詰めることが求められますように、納入業者から見れば他の部品(もしくは他社への部品)も併せて運送する必要がありますから、梱包・荷姿についての検討が要るかと思われます。
また、納入業者への発注業務では、例えば向こう3カ月先の需要予測を渡し、1か月前に内示発注、1週間前に確定発注などと、納入業者を巻き込んだ協働体制を構築することも大切なことと思われます。
ご参考になりましたら幸いです。
|