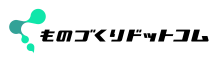
を導入しているのですが、どうもPDCAを回すのに役立っているとは思えず、現場にヒアリングしたのですが、そもそも10段階でリスク評価をしている事で、
対策を打つ、打たないの区別がつけづらいようです。思い切って、
①4段階FMEAに切り替える
②発生リスクを考慮した品質ロスコストを要対策、対策不要とし、対策したものについてはリスク評価を改定
とした方が、PDCAが回ると思われます。短段階FMEAを活用されておられる方
がおられましたら、実情とメリットをご教示頂きたいと思います。宜しくお願いします。

現場ですぐ使える品質改善技法の開発と普及活動を行っている高崎ものづくり技術研究所の濱田と申します。
RPN10段階の評価を4段階にすることで、確かに評価を簡素化することは可能となります。
RPN法は、相対評価法である為、評価点の高い方から対策していく方法が取られます。しかし、どこまでの点数を対策の対象とするかは、判断が明確になりません。つまり、発生頻度は少なくても影響の大きい不具合(人的、経済的リスク大)が相対評価の総合点数が低ければ、本来対策の必要なものが見過ごされてしまうという欠点があります。
RPN相対評価法を採用する限り、評価段階を少なくしても、基本的な考え方は変わらず、矛盾を残すことになります。
そこでご指摘の通り、発生リスクを考慮した品質ロスコストを対策要否の判断基準とする絶対評価を行うことが、市場の要求ににマッチした方法と考えられます。但し、品質ロスコストは、あくまでも消費者基準(市場における使用者の人的、経済的リスク)でなければなりません。
一方の設計工程や製造工程の失敗コストは、企業内部の勝手な事情であり、FMEAの対象ではありません。
設計工程、製造工程の不備を是正するための原因究明と未然防止対策を早急に講ずることが求められます。
リスク対策内容は市場のリスクの大きさに応じて、本対策、保護対策、情報提供の3ステップメソッドの考え方を取り入れることを提案致します。
|
高崎ものづくり技術研究所の濱田です。
おっしゃる通りだと思います。
最終製品を市場に出していない場合は、最終製品の製造企業が、市場でのリスクをアセスメントする必要があります。
しかし、これは下流側の(多分複数の)部品協供給メーカー、材料供給メーカーと共同で情報共有しながら、共通の手順を取り決めて実施する必要があります。しかし、実際にはこれを複数のメーカー間で運用するには困難が伴うと考えられます。
実際には、故障モードによって、実際起こりうる不具合内容をリストアップし、それは絶対に上流企業へ流出さないという対策を講じ、上流側でその対策の可否判断して頂くことになるのではないでしょうか?
上流企業ではその情報を基に、市場でのリスクを判断すればよいと思います。
下流側から流出が有り得るという仮定は絶対に行ってはならないと思いますが、いかがでしょうか。
|
誠に的を得たお考えと思います。
FMEAを実施する前提として、(工程)設計がしっかりと出来ていることが求められます。つまり、潜在不良が流出しない様、信頼性、安全性を考慮した設計を行い、結果をQC工程図としてアウトプットします。
設計に抜け漏れがないかどうかをFMEAで確認するのですから、左にQC工程図、その右に信頼性にモレがないかどうか、アセスメントの検証結果(発生度、影響度、検出度)を記入すればFMEAを実施したことになります。
|