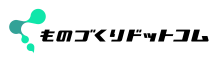
設備のメンテナンスと生産について質問がございます。
コスト・法律遵守するという相反する基本的な問題があるなかで。
設備メンテナンス及び5S活動に人員と時間を裂く余裕がありません。
20年にわたり設備を利用し生産を行っておりますが、老朽劣化が著しいなかで老朽化にともなう不良の発生などもございます(設備劣化のため不純物の付着など)。生産を続ける必要最低限の定期的なメンテナンスを行っていますが、それでは根本解決にならないのではという疑問もあります。
残念ながら現時点で弊社には設備を再構築する体力はありません。
弊社の伝統的な習いとして「まず生産」という強いながれもあります。
今後も直し直し現在の設備をつかうとした場合、生産量を若干セーブし生産に当てていた時間を少し削り定期的に「保守整備・5S」にあてるべきか悩んでおります。
以上、ご回答お待ちしております。

クリーン化を専門にしています、清水と申します。
私はクリーン化として、長年現場を這いずり回りました。その現場視点で気が付くことを記します。
現状、生産優先または生産のみに集中している感じを受けました。
ものづくりの会社では、必ずと言って良いほど設備を使っていますので、同じようなことで苦労されている中小企業も多々あります。
私が昔ある半導体関係の現場の管理者から聞いた話を紹介します。
ある日A設備が停止してしまった。長時間かけて原因を調べたところB部品が劣化、故障していました。
その部品を交換しようとしたが、社内に在庫がなかった。メーカーに部品を発注したところ、この部品は製造に時間がかかるので納期は2週間と言われた。従ってこの設備を含むラインは2週間止まっています。 という話でした。
今時こんなことをしていると、その管理者は首になるか、配置換えされるのが普通ですね。その間製品が作れない、つまり機会損失ですから。
私はセミナーや教育などでは、“生産設備や付帯設備の予防保全、延命化”をクリーン化の目的の一つとして紹介しています。
それは、設備を何もせず、生産だけに専念してしまうと上記の例のような問題が起きる。
しかし、定期的に巡回しクリーン化視点で設備を良く観察していくと、不具合が見つかる。すべての問題が発見されるわけではありませんが、発見の確率は向上します。
例えば部品の摩耗、発塵、劣化など色々な観点で観察し、不具合が発見されたときは、即修理、対応する。
ただし、その都度設備を停止できない場合は、その個所を拾い、また部品も用意しておき、次の保全計画に含めて一緒にやろうということです。
何もしないで、設備停止の都度、その場凌ぎの対応をしているのでは、設備は頻繁に故障を繰り返します。そして故障が多すぎて、もう新しい設備に買い替えるということになってしまいます。メンテナンスメンバーの悲鳴や愚痴も出ます。
ところがよく観察し、前記のように予防保全に努めると、故障が少なくなります。裏返すと設備の延命化に繋がるということです。
設備の延命化が進むと減価償却が進むことになり、安く製品が作れ、儲けが増大します。
ところが故障ばかりしていると、儲ける前に設備を買い替えるということになります。
これが続くと自転車操業のようになっていくことも考えられます。その状態を回避する、或いは体質を切り替える必要があります。
ここで必要なのは、人財育成だと考えます。
メンテナンスはそれに精通したメンバーがやるとしても、その仕事を管理職、経営者が良く観察し、指導したい。
“メンテナンス作業はどこからどこまでかを考えること、教えること”も大切です。設備が直った、動いただけで良いのでしょうか。
その場凌ぎが繰り返されると、故障頻度も改善されません。メンテナンスメンバーも忙しい環境から解放されません。
もしかするとその場凌ぎからまた設備が故障する。自分の仕事が増えてしまうと言った悪のスパイラルにはまっているのかも知れません。そして品質、生産に影響が出るかもしれません。設備を修理するだけでなく、品質、生産、安全のことも考えて対応してほしい。
経営者や管理職の方は、修理記録や設備の状況を見て、MTBF(平均故障間隔)が短いとすれば故障が多い設備だと見ることが出来ます。
すると生産は計画通りかということも気になりますし、異物などでやり直し手直しが必要となっても、これは生産計画には含まれていないはずです。
やり直し、手直しが発生すると、そこで製品が停滞し、次工程には流動されず手空きが発生したり、挽回のための時間外労働をしなくてはならないかもしれません。
納期遅延も発生し、お客様に迷惑をかけるかもしれません。
人手がないとのことですが、設備の巡回、観察や5Sについては、経営者、管理職の方が適時現場を見ることから始めても良いと思います。
単にぐるぐる回るのではなく、故障の多い設備、5Sなど着目する項目を決め実施したいです。継続することで、着眼点や問題点が見えてくると思います。
工場を巡回すると、作業者との会話もあると思います。それに終始してはいけませんが、情報のアンテナとして活用したい。
設備の汚れが酷いとか、故障が多い設備には、作業者も愛着が持てないかもしれません。
そして設備の扱いが荒くなる。故障が増えるという事例もありました。
もう一度整理しますと、
① 現場、設備を絞り込んで良く巡回することで、徐々に不具合が見つかる。これらを予防保全していく。 →設備故障が減り、延命化ができる。
このことは、経営者や管理職の方がまずやってみる。様々なものが見えて来ると思います。
② 不具合や異常を発見し、品質、生産、安全、利益貢献など幅広く見たり考えたりできる人を育てる。→多面的にものを見る人が増え、その人たちが設備の延命化や環境改善に貢献してくれる。そして、ものづくり基盤が強くなる。つまり悪いスパイラルを断ち切り、良いスパイラルに乗っていくということです。
人は材料ではなく、財産として育てたい。必ずや貢献してくれると信じて育成しましょう。
事例を紹介しながら、あるべき姿を羅列しました。
参考になれば幸いです。
|
類似の「めっき処理」に対するコンサルティング成功事例があります
めっき液に対する、均一化と
めっき処理・洗浄処理への物理刺激として
安価で低出力の「超音波追加を提案します」
具体例
超音波プローブ 5000-30000円 程度
ファンクションジェネレータ 6000-50000円 程度
追記
脱気マイクロバブル発生液循環装置の追加は大きな成果になっていますが
ノウハウが多く安易に推奨できません
興味があれば、お問い合わせください
|