今回は4つのポイントのうちの3つ目、「ポイント③ 設計者の意識を高く保つ取組みを継続的に実施する」について解説します。
1.なぜ設計者の意識を高く保つ取組みが必要なのか
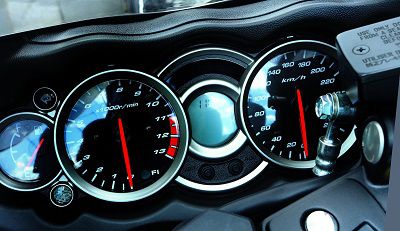
製品事故が発生しないからといって、設計者が褒められることはありません。リスクアセスメントをどれだけ入念にやっても、売上が大きく増えることもありません。多くの場合、設計者にとってリスクアセスメントは退屈で面白くない仕事です。リスクアセスメントは重要な考え方ですが、残念ながら完璧な手法だとは言えません。どうしても抽象的な部分だったり、推測に頼ったりする部分が残ってしまうからです。そういう意味で、リスクアセスメントは設計者の意識や考え方に影響を受けやすいと言えます。そのような状況の中で、長期に渡ってリスクアセスメントの効果を上げ続けるためには、設計者の意識を高く保つ取組みが重要だと考えます。油断をするとすぐに形骸化してしまいます。
実は、設計者の意識を高く保つことに最も役立つのは、自社で起こしてしまった製品事故やリコールです。それらへの対応は数か月から数年単位になることもあり、被害者にとっても自社・設計者にとってもつらい時期が続きます。設計者の頭の中には、製品安全の重要性が刻み込まれます。リコールなどの大きな不具合を経験したことがある設計者は、むしろリスクを取れなくなることが問題になるぐらいです。しかし、リコールや製品事故はそう頻繁に発生するものではありません(頻繁に発生している企業は経営危機に陥っているはずです)。リコールや製品事故に匹敵するような、設計者の意識を向上させる活動を実施していく必要があるのです。下記は製品安全や品質向上の話の時に、よく引用されることわざです。私も常に頭に入れておくように心がけています。
You can lead a horse to water, but you can’t make him drink.
(馬を水飲み場まで連れて行くことはできるが、飲ませることはできない)
【意味】
人が自分でやりたいと思わない限り、強制的にやらせることはできない
設計者が自らリスクアセスメントの必要性を認識することが、最も重要なのです。
2.設計者の意識を高く保つ取組みの事例
私は会社員時代に、自部門(20~30名の設計部門)の品質向上のコーディネーター役として様々な活動に取り組んで来ました。また、現在、製品設計コンサルタントとして、それらの経験を生かして同様の取組みを行っています。これまで実際に実施し、効果を上げている事例を一部紹介します。すべてを実施することは負荷が大きいかもしれませんが、できることから始めてみてください。
(1)失敗事例報告会
多くの企業で実施しているのではないでしょうか。この活動は、品質向上や設計者の意識向上のための、最も基本的かつ効果的な手段です。実際に発生した製品事故、製品事故にまでは至らなくても、事故につながる可能性のあったヒヤリハット事例などを全員で共有します。また、事例の共有だけではなく、なぜ起きてしまったのかについて、直接原因~根本原因まで深堀りします。
(2)他社のリコール・製品事故・PL裁判事例を学ぶ
自社の失敗事例だけではなく、他社の失敗事例を学ぶことも非常に効果があります。リコールや製品事故に関する情報は、下記のwebサイトで簡単に入手できます。学びやすい環境にあると思います。
■nite(製品評価技術基盤機構)
製品事故・リコール情報検索
■消費者庁リコール情報検索
■国民生活センター
事故情報データバンク
PL裁判は事例があまり多くないのですが、中身が詳細に開示されているので、非常に参考になります。公的機関のwebサイトで見ることができる判例も多いですし、PL裁判関連の専門書を数冊購入すれば、ほとんどの判例を網羅することができます。
(3)設計者自身が講師となる勉強会を行う
人は誰かに教える時に最もよく学ぶとマネジメントで有名なドラッカーは語っています。私もそう思います。このような記事を書く時、セミナー講演用の資料を準備する時などが、自分自身にとって最も効果的な勉強方法だと強く感じます。設計部門内で持ち回りにより、設計者が勉強会の講師役をする取組みが効果的です。普段の会議では眠そうな様子を見せる設計者も、自分が講師となると目の色が変わります。たった30分の勉強会なのに、自宅で10時間以上も準備してくる設計者もいます。12名が所属する設計部門で1回/月勉強会を開催すると、講師役が回ってくるのは1回/年です。それほど大きな負荷とは言えないでしょう。毎回製品安全やリスクアセスメントの話だと面白くないので、様々なテーマを織り交ぜながら実施すると、飽きずに継続させることができます。また、参加メンバーのスキル、興味などにも合わせて、テーマを選定することも大切です。
(4)理解度確認テストをする
失敗事例報告会や勉強会の内容などを、年に1回程度でよいのでテストをします。理解度のチェックという位置づけでも構いませんし、合格点を決めて認定制度にしてもよいと思います。若手設計者のスキルアップ目標にも使えます。私の過去の経験では、ベテラン設計者は若手設計者に負けるのが嫌なので、ベテラン設計者ほど勉強するという面白い状況もありました。
(5)設計KYT(設計危険予知トレーニング)
工場などの現場や交通事故防止などで、昔から取り入れられているKYTは、設計でも実施可能です。私も自社の失敗事例などを題材に取り組んできました。例えば、かつて失敗した図面を題材に、その図面にどのような心配点があるかを、参加者でディスカッションをします。リスクに対する知識や感度の高い設計者はすぐに心配点を抽出することができますが、そうではない設計者はなかなか見つけ出せません。レベルの高い設計者の発言などから、もっと学ばないといけないという意識の向上につながります。
(6)リスクアセスメントに若手設計者を積極的に参加させる
リスクアセスメ...