【連載の目次】
1. QC7つ道具 (その1) ヒストグラム
2. QC7つ道具 (その2) パレート図
3. QC7つ道具 (その3) 特性要因図 ←今回の記事
4. QC7つ道具 (その4) 管理図
5. QC7つ道具 (その5) 散布図
6. QC7つ道具 (その6) チェックシート
7. QC7つ道具 (その7) 層別
品質管理はもちろん、あらゆる職種・業種の問題解決やデータ処理の実践に非常に有効な手法である「QC七つ道具」。エンジニアやビジネスマンにとって、必要不可欠な知識と知りながら、「手間や時間がかかりそう」、「難しそう」と、つい避けてきたという方も多いのではないでしょうか。
実は、各要素の作り方、解析用の手順を知れば、データ処理も決して難しくはありません。品質管理や改善活動に不可欠な「QC七つ道具」を習得して、初心者の方にも簡単にデータ処理や品質管理を効率よく実践することができます。また、「QC七つ道具」の基礎知識を身につければ、検定・推定、実験計画法、多変量解析、信頼性工学などの高度な各種手法もスムーズに学習できてビジネスに役立てます。
QC7つ道具は単なる道具であり、その内容を理解していても使いこなせなくては意味がありません。つまり、何のために使うのか(目的)、データの収集・分析など、QC7つ道具に関わるQC問題解決の全体を理解する必要があるのです。現場で問題が発生したときは、現場に行って、問題を起こした現物を見て、現実(現状)を知り、その確認したデータをどんなQC7つ道具を選定して解析するのかが重要です。
今回は、ある特性に対する原因を系統的に整理して関連付けるために使用するQC七つ道具の特性要因図について解説します。
1.特性要因図とは
前回のQC7つ道具、その2 パレート図に続いて解説します。
特性要因図とは、特性(結果)に対して、どのような要因が関係、影響しているかをツリー状に表わした図で、広い視野で要因を拾い上げるのに有効です。その形状から「フィッシュボーン」とも呼ばれます。 課題解決にあたっては、ついつい少数の目についた要因で実験、対策を進めがちですが、思わぬところに重要な要因が隠れていることが往々にしてあります。 対策に入ってしまうと多大な時間、費用が発生しますので、はやる気持ちを抑えて関係者の知見を特性要因図に列挙、整理し、優先順位を付けたうえで問題解決、実験に入るのが解決の早道になります。
特性要因図を英語では、Cause and Effect Diagram とか、形状が魚の小骨に似ている事からフィッシュボーンと呼称され、ある特性に対する原因を系統的に整理して関連付けるために使用します。QCサークル発表会などでよく見かけるQC7つ道具の一つです。特性要因図は、1960年代に石川馨氏よって開発され、クレームなど製品の品質特性に関連する要因を列挙する手法であるとともに、求められる製品の品質特性を得るためには、どのような項目を管理すれば良いかを漏れなく列挙するためのツールとして用います。
図1のように、一次要因に対し二次要因、三次要因として何が考えられるかを掘り下げて行きます。 原因を掘り下げていくことにより大要因に関連する中小の要因を見つけ出し関係性を整理する事が出来ます。
不良などが発生した場合、その考えられる要因を列挙して、その中から原因を特定します。その際、不良現象(不良特性)を頭に、要因(原因と考えられる項目)を列挙します。列挙する場合に漏れがないよう、例えば工程の4Mまたは5Mに分類、それぞれを太骨にし、要因を小骨で表します。
解析ツールとしては、必ずしも特性要因図のフォーマットにする必要はなく、ツリー状の系統図に表すことがあります。特性要因図は、課題解決で深堀すべきポイントを把握するために欠かせません。例えば、ヒストグラムや管理図、散布図などでデータの特徴を理解し、次にパレート図や特性要因図などで深堀すべきポイントを掴むために使用したりします。
図1.特性要因図
特性要因図は定量的解析が主なQC7つ道具の中で唯一定性的な言語データを扱います。
2.特性要因図の使い方
特性要因図を作成するときは、まずある不適合を引き起こす現象を考えます。 次にその現象を引き起こすであろう要因やそれに関連する子・孫要因の関係を整理し突き詰めていく事により現象の元となっている関連因子が浮かび出て来ます。その後に、特性要因図の中から効果がありそうな要因をピックアップして対策を検討するのです。
特性要因図だけで原因が正しいかどうかを特定できません。 過去に実績があって解っている場合を除けば可能性がある要因について熟考し、効果的且つ検証可能と思われるものに対して更なる調査や解析、実験を行い確認して行く事になります。
特性要因図の作成は”MECE“な思考で漏れなくあらゆる可能性を網羅するのに効果的なワークフローであると言えます。例えばスリップ事故の原因を掘り下げてみてみます。
表1.あるスリップ事故に対する要因抽出結果
一次要因 | 二次要因 | 三次要因 |
---|---|---|
人要因 | ハンドル操作ミス | 運転中通話の片手運転 |
前方不注意 | ||
急ブレーキ | オーバースピード | |
対向車認知遅れ | ||
ワイパー操作 | 弱にして運転 | |
車要因 | タイヤライフ | 摩耗により溝が無い |
スリップ防止機能弱 | ALBシステム無 | |
スリップデフ無 | ||
環境 | 雨天 | 路面がぬれ摩擦低下 |
路面状況 | 砂泥上の降雨で滑りやすかった | |
対向車 | カーブで接近してきた | |
運転計画 | ルート | カーブの多い細い裏道を選択 |
時間 | 到着時間までの余裕が無かった |
(1)特性にはQCD(Quality Cost Deivery)に関連して次のようなものがあります。
- 品質に関するもの 長さ、重量、欠陥数、不純物量、耐熱性
- コストに関するもの 原材料費、副資材費、メンテナンス費、人件費、倉庫費
- 納期に関するもの 工数、生産日数、納入日数、装置スループット
- その他 交通事故、労働災害、離職率、有給取得率
(2)要因には一般的に4Mと呼ばれるカテゴリーを主の枝骨として分類します。
- Material 材料、もの
- Machine 機械、設備、計器
- Method 方法
- Man 人的関係
3.特性要因図作成の注意点
特性要因図を作成する時は、一人では出てこないアイデアを多く捻出する為に、関連部署複数人でブレインストーミングを利用して行うことが効率的です。 大きな白紙に付箋紙で思いつく要因を書き出して、アイデアが出尽くした後で特性要因図の形に整理する方が、滞らず良いでしょう。 その時に類似の要因は束ねて整理しながら行います。
作成時の注意点としては、要因を掘り下げすぎて関連が曖昧になったり、複数の要因にまたがる子要因を出しすぎて複雑化しすぎたりと、何を目的として作成していたか解らなくなりがちな事です。
特性要因図の作成に慣れないうちは、図2のように4Mを基本として行うとほぼ万遍なく要因を思いつく事が出来ます。 一度完成したら、さらに現場を回って不足や見直すポイントが無いかをチェックすると、会議室だけで完結させるよりも完成度が高くなります。
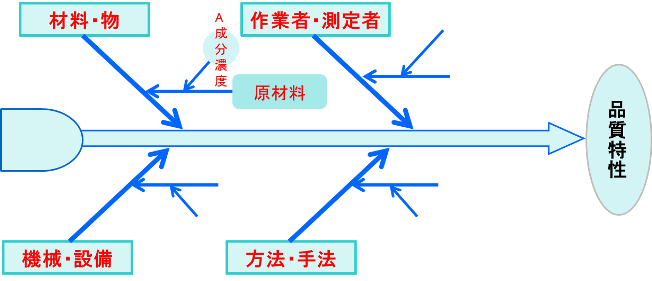
図2.4Mを配置した特性要因図
特性に対する効果ある要因を見つけ出したらそれを制御する子要因との関係を別の解析手法を用いて分析してみます。
特性要因図は、ある結果に対する原因を漏れの無いよ...